વિદ્યુત-તાપીય (electrothermal) ઉદ્યોગો
February, 2005
વિદ્યુત-તાપીય (electrothermal) ઉદ્યોગો : વિદ્યુતના ઉપયોગ દ્વારા પ્રાપ્ત થતા ઊંચા તાપમાનની મદદથી વિવિધ રાસાયણિક પદાર્થો બનાવતા ઉદ્યોગો. સામાન્ય વ્યાપારિક દહન-ભઠ્ઠી (combustion furnace) દ્વારા લગભગ 1700° સે. જેટલું તાપમાન મળી શકે છે; જ્યારે ઘણી રાસાયણિક પેદાશો મેળવવા તેનાથી વધુ 4,100° સે. જેટલું તાપમાન આપતી વિદ્યુતભઠ્ઠી(electric furnace)ની જરૂર પડે છે. ઊંચા તાપમાનની બેવડી અસર થાય છે : તે પ્રક્રિયાની ઝડપ વધારે છે અને સમતોલન(equilibrium)ના નવા સંજોગો પ્રસ્થાપિત કરે છે. આને કારણે વિદ્યુતભઠ્ઠી દ્વારા અગાઉ જે જાણીતા ન હતાં તેવાં સંયોજનોનું ઉત્પાદન થઈ શક્યું છે; દા. ત., સિલિકન કાર્બાઇડ અને કૅલ્શિયમ કાર્બાઇડ. અન્ય ભઠ્ઠીઓ કરતાં વિદ્યુતભઠ્ઠીનું વધુ ચોક્કસ રીતે નિયંત્રણ થઈ શકવા ઉપરાંત તેમાં ઉષ્મીય ઘટ ઓછી હોવાથી ઉષ્માનું વધુ સંકેન્દ્રણ થઈ શકે છે. ચીમની વાયુઓ(flue gases)નો અભાવ અને ઉષ્માસ્રોત અને ગરમ થતા દ્રવ્ય વચ્ચેની ઊંચી તાપમાન-પ્રવણતા(gradient)ને કારણે આ સાનુકૂળ પરિસ્થિતિ સર્જાય છે. વળી દહનભઠ્ઠી કરતાં વિદ્યુતભઠ્ઠી વધુ સાફ (cleaner) અને પ્રચાલનની દૃષ્ટિએ પ્રમાણમાં સરળ હોય છે. સામાન્ય રીતે તે ઊંચા ઍમ્પિયરેજ (amperage) અને સાધારણ વોલ્ટેજના પ્રત્યાવર્તી વીજપ્રવાહ (a.c.) વડે ચાલે છે. [વીજાપઘટની (electrolytic) ઉદ્યોગોમાં એકદિશી વીજધારા (સૂલટ વીજપ્રવાહ, direct current) વપરાય છે.]
વિદ્યુતભઠ્ઠીઓના પ્રકાર : વિદ્યુત વડે ચાલિત ભઠ્ઠીઓના પ્રકાર આ પ્રમાણે છે : (i) ચાપભઠ્ઠી (arc furnace), (ii) પ્રેરણભઠ્ઠી (induction furnace), (iii) અવરોધ-ભઠ્ઠી (resistance furnace) અને (iv) પ્લાઝ્મા-ભઠ્ઠી (plasma furnace).
(i) ચાપભઠ્ઠી : આવી ભઠ્ઠીમાં સામાન્ય રીતે ગ્રૅફાઇટ અથવા કાર્બનના બે કે વધુ વીજધ્રુવો વચ્ચે અથવા વીજધ્રુવો અને ભઠ્ઠીમાંના ભરણ (charge) વચ્ચે વિદ્યુતચાપ વડે ગરમી પેદા કરવામાં આવે છે. ભઠ્ઠી સામાન્યપણે ઉચ્ચતાપસહ (refractory) દ્રવ્યના અસ્તરવાળી નળાકાર કવચ (shell) જેવી હોય છે. જ્યાં ગઠ્ઠા(ingots)ના સ્રોત તરીકે ચાપભઠ્ઠી વપરાતી હોય ત્યાં કેટલીક કંપનીઓ દ્વારા રોલિંગ-મિલ (rolling-mill) પ્રચાલનો માટે પણ આ ભઠ્ઠીનો ઉપયોગ થાય છે. વિશ્વમાં ઉત્પાદિત થતા પોલાદનો 20 % જેટલો જથ્થો વિદ્યુતચાપ અને પ્રેરણભઠ્ઠીઓ વડે બનાવવામાં આવે છે. સામાન્ય રીતે આવાં પ્રચાલનો બૅચવાર કરવામાં આવે છે. નિમગ્ન-ચાપ (submerged arc) શાફ્ટ-ભઠ્ઠીઓ(shaft furnaces)ના પ્રચાલનમાં ભઠ્ઠીના મથાળેથી ઘન ભરણું ઓરવામાં આવે છે, જ્યારે તળિયે એકઠી થતી દ્રવીભૂત પ્રાવસ્થાઓનું અવારનવાર અંશનિષ્કાસન (tapping) કરવામાં આવે છે. આવી ભઠ્ઠીઓ તત્વરૂપી ફૉસ્ફરસ અને કૅલ્શિયમ કાર્બાઇડના ઉત્પાદન માટે ઉપયોગમાં લેવાય છે.
(ii) પ્રેરણભઠ્ઠી : ધાતુ જેવા સંવાહક પદાર્થો માટે આવી ભઠ્ઠીનો ઉપયોગ થાય છે. અહીં ભરણ(charge)માં ઉદભવતા પ્રેરિત વીજપ્રવાહ વડે વિદ્યુત-ઊર્જાનું ઉષ્મામાં રૂપાંતર થાય છે. ભઠ્ઠી એક પ્રકારનું ટ્રાન્સફૉર્મર ગણી શકાય કે જેમાં પ્રાથમિક ભાગ તરીકે શક્તિસ્રોત સાથે જોડેલ તાંબાનાં જાડાં ગૂંચળાઓ; જ્યારે દ્વિતીયક (secondary) ભાગ તરીકે ધાત્વીય ભરણ હોય છે.
પ્રેરણભઠ્ઠીઓનું પ્રચાલન 60થી 5,00,000 હર્ટ્ઝ(Hz)ની આવૃત્તિએ થાય છે; પણ વ્યાપારિક ધોરણે વપરાતી વિદ્યુત-તાપીય વિધિઓમાં 6,000 Hzથી ઊંચી આવૃત્તિ ઉપયોગમાં લેવાતી નથી. આવૃત્તિ જેમ વધારવામાં આવે તેની તાપન-અસર નીચી ક્ષેત્ર-પ્રબળતા(field strength)એ મળે છે. આથી નીચી આવૃત્તિવાળી ભઠ્ઠીમાં ભરણું લોખંડના અંતર્ભાગ (core) આસપાસ મૂકવામાં આવે છે; જ્યારે ઊંચી આવૃત્તિવાળી ભઠ્ઠીઓમાં આવા અંતર્ભાગની જરૂર પડતી નથી.
(iii) અવરોધ–ભઠ્ઠી : જરૂરી ઉષ્મા પેદા કરવા માટેનો વિદ્યુત-અવરોધ ભરણ-દ્રવ્ય પૂરો પાડે તો ભઠ્ઠીને પ્રત્યક્ષ-તાપિત અવરોધ (direct-heated resistance) પ્રકારની અને જો ઉષ્મા ઉત્પન્ન કરવાના હેતુથી ભરણમાં ઉચ્ચ-વીજઅવરોધવાળું દ્રવ્ય ઉમેરવામાં આવે તો તેને અપ્રત્યક્ષ-તાપિત ભઠ્ઠી કહે છે. ઘાણ-પ્રચલિત અવરોધ-ભઠ્ઠીઓ સિલિકન કાર્બાઇડના તથા ગ્રૅફાઇટ વીજધ્રુવોના ઉત્પાદન માટે વપરાય છે. લંબ શાફ્ટવાળી અવરોધ-ભઠ્ઠીઓ (vertical shaft resistance furnaces) ઍલ્યુમિનિયમના ઉત્પાદન માટેના કોષના કૅથોડની રચના માટે જરૂરી એવા સંવાહી (conductive) કાર્બનના ઉત્પાદન માટે ઍન્થ્રેસાઇટના નિસ્તાપન (calcination) અર્થે ઉપયોગમાં લેવાય છે. વીજરાસાયણિક ઉદ્યોગમાં ચાપ અને અવરોધ-ભઠ્ઠીઓ વધુ વપરાય છે.
(iv) પ્લાઝ્મા–ભઠ્ઠી : પ્લાઝ્મા-ચાપભઠ્ઠી એ વિદ્યુતીય રીતે ગરમ કરવામાં આવતી વાયુભઠ્ઠી (gas furnace) છે; જે 3,730°થી 4,730° સે. સુધીનું તાપમાન ઉત્પન્ન કરે છે. આમાં કોઈ પણ વાયુ વાપરી શકાય છે. બે વીજધ્રુવો વચ્ચે સતત પ્રજ્વલિત ચાપ વચ્ચેથી વાયુને પસાર કરવાથી તે આંશિક આયનીકરણ પામે છે. આ ગરમ આયનીકૃત વાયુ(પ્લાઝ્મા)ને પ્રક્રિયાકક્ષ(reaction chamber)માંથી પસાર કરવામાં આવે છે. લોહ-અયસ્કના અપચયન માટે આનો ઉપયોગ સૂચવાયો છે; પણ તેની ઊંચી કિંમતને લીધે તેનો વ્યાપારી ઉપયોગ ઓછો થયો છે. આમ છતાં પર્યાવરણના નિયંત્રણ તેમજ વ્યાવસાયિક સલામતી તરફ વધેલો ઝોક લક્ષમાં લેતાં ઊંચી કિંમતને ઓછી અગત્યની ગણવામાં આવે છે.
વિદ્યુત-તાપીય વિધિ દ્વારા ઉત્પાદિત થતા કેટલાક પદાર્થો નીચે પ્રમાણે છે :
1. કૃત્રિમ અપઘર્ષકો (abrasives) :
1891 પહેલાં વપરાતા હીરા, કોરંડમ (corundum), એમરી (emery), માણેક (garnet), ક્વાર્ટ્ઝ, (quartz), કીસલગુર (kieselguhr) અને રૂજ (rouge) જેવા બધા અપઘર્ષકો કુદરતી નીપજો હતી. એ જ વર્ષે ઈ. જી. અચેસને ઘરે બનાવેલી વિદ્યુતચાપભઠ્ઠીમાં માટીના કઠોરીભવન (ઢીભવન, hardening) કરવાના પ્રયત્ન દરમિયાન સૌપ્રથમ કૃત્રિમ અપઘર્ષક ઉત્પન્ન કર્યો. તેમણે જોયું કે આ નવા કઠોર, જાંબલી સ્ફટિકો સિલિકન કાર્બાઇડના છે. આ સ્ફટિકો કાચને કાપી શકે તેવા કઠોર હોઈ અચેસને તેમને કાર્બોરંડમ(carborundum)ના વ્યાપારી નામે 1 કિલોના $ 1940ના ભાવે વેચેલા. સિલિકન કાર્બાઇડની એક અન્ય બનાવટ ક્રિસ્ટૉલૉન(crystolon)ના નામે વેચાય છે. સૌથી વધુ વ્યાપક પ્રમાણમાં વપરાતો સંગલિત (fused) ઍલ્યુમિનિયમ ઑક્સાઇડ નામનો અપઘર્ષક એ વિદ્યુત-તાપીય ભઠ્ઠીમાં બનાવાય છે. કૃત્રિમ રીતે બનાવાયેલા સૌથી કઠોર પદાર્થોમાંનો એક એવો બોરૉન નાઇટ્રાઇડ અથવા બૉરેઝૉન (borazon) પણ વિદ્યુત-તાપીય નીપજ છે.
આધુનિક સરાણ (grinding) – ઓજારોની ઉત્ક્રાંતિની શરૂઆત કૃત્રિમ અપઘર્ષકોની શોધ અને ઉત્પાદનથી થઈ. આ ઓજારો મોટરગાડીઓ, વિમાનો, વિવિધ પ્રકારનાં યંત્રોના સંખ્યાબંધ ભાગોને બહુ ચોક્કસ (precise) ઘાટ આપવા માટે અત્યંત અગત્યનાં છે. ઘસારો (wear) ઓછો લાગે તે હેતુથી ધાતુકર્મી (metallurgist) દ્વારા જે વધુ અને વધુ સખત મિશ્રધાતુઓ વિકસાવાઈ છે : તેમાંની ઘણીને આ કૃત્રિમ અપઘર્ષકો વડે ધાર્યો આકાર આપી શકાય છે. સિલિકન કાર્બાઇડ અને ઍલ્યુમિના (ઍલ્યુમિનિયમ ઑક્સાઇડ) – એ ઈંટ અથવા ઢીલા (loose) દ્રવ્ય રૂપે ઉચ્ચ તાપસહ પદાર્થો તરીકે પણ વપરાય છે.
સિલિકન કાર્બાઇડ : આના ઉત્પાદન માટેના કાચા પદાર્થો સિલિકા (silica) (SiO2) અને કાર્બન છે. કાર્બન પેટ્રોલિયમ કોક(coke)માંથી મેળવાય છે; જ્યારે રેતીમાં 98થી 99.5 % સિલિકા હોય છે. ઉત્પાદન સાથે સંકળાયેલી પ્રક્રિયાઓ નીચે પ્રમાણે છે :
SiO2(c) + 2C (amorph) → Si(c) + 2CO(g) Δ H = + 606 kJ
Si(c) + C (amorph) → SiC(c) Δ H = 127.7 kJ
સમગ્ર પ્રક્રિયા : SiO2(c) + 3C (amorph) → SiC(c) + 2CO(g) Δ H = + 478.3 kJ
આકૃતિ 1માં સિલિકન કાર્બાઇડના ઉત્પાદન માટેની ખંડ-આકૃતિ દર્શાવી છે. રેેતી અને કાર્બનને લગભગ 1 : 3ના મોલર ગુણોત્તરમાં મિશ્ર કરી 12થી 24 મી. લંબાઈ, 3 મી. કે વધુ પહોળાઈ, અને 2થી 3 મી. ઊંચાઈ ધરાવતી દ્રોણિકા (trough) જેવી ભઠ્ઠીમાં મૂકવામાં આવે છે. તેમાં જો લાકડાનો વહેર ઉમેરવામાં આવ્યો હોય તો તે ભરણની છિદ્રાળુતા વધારે છે અને બાષ્પનું પરિવહન (circulation) તથા ઉત્પન્ન થતા કાર્બન ડાયૉક્સાઇડનું નિર્ગમન શક્ય બનાવે છે. દ્રોણિકાના છેડે વીજધ્રુવો હોય છે, જે ગ્રૅફાઇટના કેન્દ્રીય તાપમાન
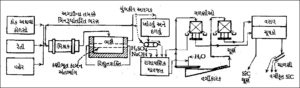
સિલિકન કાર્બાઇડના ઉત્પાદન માટે ક્રમદર્શી રેખાચિત્ર
(central heating) માટેના અંતર્ભાગ સાથે જોડેલા હોય છે. ભઠ્ઠીની દીવાલો સ્ટીલની ફ્રેમમાં બેસાડેલી છૂટી ઉચ્ચ-તાપસહ ઈંટોની બનેલી હોય છે. ભરણનો બાહ્ય ભાગ અલગક (insulator) તરીકે વર્તતો હોઈ ભઠ્ઠીમાં ઉષ્માની ઘટ વધુ પડતી થતી નથી. જેમ જેમ સિલિકન કાર્બાઇડ બનતો જાય તેમ તેમ ભરણની વાહકતા વધતી જાય છે અને આથી વોલ્ટેજમાં ઘટાડો કરીને વીજશક્તિ જાળવી રાખવામાં આવે છે; દા. ત., શરૂઆતમાં વીજધ્રુવો વચ્ચે 230 Vએ 6,000 Aનો પ્રવાહ વહેતો હોય તો અંતે તે 75 Vએ 20,000 Aનો હોય છે. શરૂઆતમાં અંતર્ભાગ 2,040° સે. સુધી ગરમ થાય છે, પણ પછી તાપમાન ઘટીને 1,600° સે. જેટલું થઈ જાય છે. ભઠ્ઠીની બહારની ધારો લગભગ 1,370° સે. જેટલા તાપમાને રહે છે. ભઠ્ઠીનું તાપમાન અતિશય ઊંચું ન જવું જોઈએ; કારણ કે તેમ થતાં સિલિકન કાર્બાઇડનું વિઘટન થઈ સિલિકન અને ગ્રૅફાઇટ ઉત્પન્ન થતાં સિલિકનનું બાષ્પીભવન થાય છે.
પ્રક્રિયા માટે લગભગ 36 કલાકના તાપન અને કેટલાક દિવસોના શીતન(cooling)નો સમય જરૂરી છે. ઠંડા પડ્યા પછી સિલિકન કાર્બાઇડના સ્ફટિકોને દૂર કરવામાં આવે છે. 75 ટન(t)ના ભઠ્ઠી-ભરણ (furnace charge)માંથી 11.3 ટન (t) જેટલી નીપજ પ્રાપ્ત થાય છે. મોટા સ્ફટિકોને ખાંડી, ધોઈ, પછી સલ્ફ્યુરિક ઍસિડ અને કૉસ્ટિક સોડાની માવજત આપી સાફ કરવામાં આવે છે. સ્ફટિકોને ચાળી વર્ગીકૃત કરવાથી પરિષ્કૃત (finished) નીપજ 6-જાલાક્ષિ(mesh)થી માંડીને બારીક પાઉડર રૂપે મળે છે. ભરણનો વણવપરાયેલો બાહ્ય ભાગ નવા ભરણ સાથે મિશ્ર કરી ફરીથી ઉપયોગમાં લેવામાં આવે છે. મોઝ (Mohs) માપક્રમ ઉપર કાર્બોરન્ડમની કઠિનતા 9 મોઝ (હીરાની 10 મોઝ) છે.
સંગલિત (fused) ઍલ્યુમિનિયમ ઑક્સાઇડ : એલન્ડમ (Alundum) અને એલોક્ઝાઇટ (Aloxite) જેવાં વ્યાપારી નામો ધરાવતા સંગલિત ઍલ્યુમિનિયમ ઑક્સાઇડના અપઘર્ષકો બનાવવા માટેનો કાચો માલ અશુદ્ધ બૉક્સાઇટ (લાલ બૉક્સાઇટ) છે. તેમાં રહેલી અશુદ્ધિઓ (મુખ્યત્વે લોહ અને સિલિકન ઑક્સાઇડ) અંતિમ નીપજોના ગુણધર્મોને અસર કરતી હોઈ તેમનું યોગ્ય નિયંત્રણ જરૂરી છે. ભઠ્ઠીમાં ઓરતાં પહેલાં ઍલ્યુમિનિયમયુક્ત દ્રવ્યનું નિસ્તાપન જરૂરી છે.
આ માટેની ઊભી (ઊર્ધ્વ, vertical) ચાપ-અવરોધ (arc-resistance) ભઠ્ઠી પોલાદના લગભગ બે મીટર ઊંચા વર્તુળાકાર કવચની બનેલી હોય છે. તે 1.5 મી. જેટલા વ્યાસવાળા ક્રુસિબલ-કાર્બનના પાયા પર રહેલી હોય છે. ભઠ્ઠીની બહારની સપાટી પાણી વડે ઠંડી રાખવામાં આવે છે; જેથી દીવાલને અડીને આવેલ બિનસંગલિત (unfused) ઍલ્યુમિના ભઠ્ઠીને ઉચ્ચતાપસહ અસ્તર પૂરું પાડે છે. કાર્બનના ગોળ વીજધ્રુવોને ભઠ્ઠીમાં નીચે ઉતારી તેમની અને સંગલિત ભઠ્ઠી-ભરણ વચ્ચે વિદ્યુતચાપ ઉત્પન્ન કરવામાં આવે છે. સંગલન સામાન્ય રીતે શરૂઆતની બૅચ(ઘાણ)ના ઉપરના ભાગે ખાઈ (trench) જેવું બનાવી, વિદ્યુતવહન માટે તેને ગાંગડારૂપ (coarse) કોક વડે ભરી દઈ શરૂ કરવામાં આવે છે. રેતીમય (silicious) અશુદ્ધિઓને ધાતુમળ (slag) રૂપે દૂર કરવા માટે લોહની કતરણ (borings) ઉમેરવામાં આવે છે. ખાઈના સામસામેના છેડાને અડે એ રીતે વિદ્યુતધ્રુવોને નીચે ઉતારવામાં આવે છે. ઍલ્યુમિનાના સંગલનની શરૂઆત થતાં તે વીજપ્રવાહનું વહન કરે છે અને શરૂઆતનો કોક ઝડપથી વપરાવા માંડે છે. ભઠ્ઠીમાં ઉમેરાતા ભરણનો નમૂનો નિસ્તાપિત બૉક્સાઇટ (59 %), કોક (2 %) અને લોખંડનો ભંગાર (9 %) ધરાવે છે. વીજચાપ વચ્ચે ભરણ જેટલું જલદી પીગળે તેટલી ઝડપથી તેને ઉમેરતા જવામાં આવે છે. પીગળેલું ઍલ્યુમિના વીજપ્રવાહનું વહન કરે છે અને મોટાભાગના આયર્ન અને સિલિકાનું અપચયન થઈ ભારે મિશ્રધાતુ બનાવે છે, જે તળિયે બેસે છે. સંગલિત ઍલ્યુમિનાનું સ્તર જેમ જેમ ઊંચું આવે તેમ તેમ વીજધ્રુવોને ઊંચા લઈ જઈ ભઠ્ઠી ભરાઈ જાય ત્યાં સુધી વધુ ને વધુ ભરણ ઉમેરતાં જવામાં આવે છે. તે પછી વિદ્યુતપ્રવાહને બંધ કરી દઈ સમગ્ર દળ(mass)ને નિયંત્રિત સંજોગો હેઠળ એવી રીતે ઠંડું કરવામાં આવે છે કે ઇચ્છિત ગઠનવાળું દ્રવ્ય મળે. જોકે આ દ્રવ્યની કઠિનતા મોઝ માપક્રમ ઉપર કોરન્ડમ જેટલી 9 હોય છે; પણ તેનું બંધારણ ફોલ્લાવાળું (blebbular) હોય છે. આથી તેમાંથી બેરિંગ જેવી વસ્તુઓ બનાવી શકાતી નથી. આથી ઠંડા પડેલા ગઠ્ઠાઓ(ingots)ને સિલિન્ડરી દલિત્ર(roll crusher)માં ભાંગી, રાસાયણિક દ્રાવણો વડે ધોઈ, ચાળવામાં આવે છે. આ પછી તેમાંથી અપઘર્ષક ચક્રો, કાગળો અને ચૂર્ણો બનાવવામાં આવે છે અથવા નિસાદન (sintering) દ્વારા તેમને ઉચ્ચતાપસહ એવા ઘાટ આપવામાં આવે છે. એમરી એ (Fe2O3વાળું) અશુદ્ધ કોરંડમ છે. ધાર કાઢવા તથા પૉલિશ કરવા માટેનાં પૈડાં (સરાણ) બનાવવા તે વપરાય છે.
કૃત્રિમ કોરંડમ અથવા નીલમ (sapphire) : ઘડિયાળો અને આધુનિક સાધનો માટે જરૂરી એવાં સખત (hard) બેરિંગો (bearings) માટે જોઈતા કૃત્રિમ કોરંડમ અથવા સફેદ નીલમ જેવા પદાર્થો વર્નેયુઇલ પ્રવિધિ દ્વારા શુદ્ધ ઍલ્યુમિનાને હાઇડ્રોજન-ઑક્સિજન જ્યોત વડે 1925° સે.એ પિગાળીને સ્ફટિકીકરણ દ્વારા બનાવવામાં આવે છે. તારા (star) તથા પારદર્શક માણેક (ruby) અને નીલમ જેવાં ઘણાં રત્નો પણ આ પ્રવિધિ વડે બનાવવામાં આવે છે. તેમાં બીજી ધાતુ જેવી કે આયર્ન, કોબાલ્ટ, નિકલ, ક્રોમિયમના ઑક્સાઇડ ભળતાં તે રંગીન માલૂમ પડે છે.
બોરૉન કાર્બાઇડ : 1934માં નોર્બાઇડ(Norbide)ના નામે પ્રથમ બજારમાં આવેલો આ ઘણો સખત અપઘર્ષક છે. ઊંચા તાપમાને વિદ્યુતભઠ્ઠીમાં બોરૉન અને કાર્બનના મિશ્રણને ગરમ કરવાથી તે મળે છે :
4B + C → B4C.
બોરિક ઑક્સાઇડ(B2O3)નું કાર્બન-અવરોધવાળી ભઠ્ઠીમાં કોક વડે 1600° સે. જેટલા તાપમાને અપચયન કરવાથી પણ તે મળે છે :
2B2O3 + 7C → B4C + 6CO.
આ રીતે મળતી નીપજ લગભગ 99 % B4C ધરાવે છે. ચૂર્ણિત અપઘર્ષક તરીકે તથા વાલુકાક્ષેપણ (sandblasting) માટેનાં નોઝલ (nozzle) જેવાં ઢાળિત (molded) આકારોની બનાવટ માટે તેનો ખાસ ઉપયોગ થાય છે.
બોરૉન નાઇટ્રાઇડ : બૉરેઝૉન એ બોરૉન નાઇટ્રાઇડનું સમઘન (cubic) સ્વરૂપ છે. 1650° સે. તાપમાને અને 6.9 GPa (ગિગાપાસ્કલ) દબાણે સામાન્ય ષટ્ફલકીય (hexagonal) બોરૉન નાઇટ્રાઇડ આવા સમઘન સ્વરૂપમાં ફેરવાય છે. હવામાંના નાઇટ્રોજન સાથે 700° સે. તાપમાને બોરૉન સંયોજાતાં બોરૉન નાઇટ્રાઇડ બને છે :
2B + N2 → 2BN
તેની કઠિનતા હીરા જેટલી હોય છે અને તેના લાભ એ છે કે ઉપચયનનો સારી રીતે પ્રતિરોધ કરી શકે છે.
2. કૅલ્શિયમ કાર્બાઇડ : આનું પ્રથમ ઉત્પાદન આકસ્મિક થયેલું. 1892માં ટી. એલ. વિલ્સન વિદ્યુતભઠ્ઠીની મદદથી ચૂના અને ડામર-(tar)માંથી ધાત્વીય કૅલ્શિયમ બનાવવાનો પ્રયત્ન કરતા હતા; પણ મળેલી નીપજ કૅલ્શિયમ જેવી ન જણાતાં તેમણે તેને બાજુના ઝરામાં ફેંકી દીધી. તેમણે આશ્ર્ચર્ય સાથે જોયું કે આમ કરતાં મોટા જથ્થામાં દહનશીલ વાયુ ઉત્પન્ન થયો હતો.
કળીચૂનો (quicklime) (3 ભાગ) અને કાર્બન(2 ભાગ)ના મિશ્રણને વિદ્યુતભઠ્ઠીમાં 2,000°થી 2,200° સે. તાપમાને ગરમ કરવાથી કૅલ્શિયમ કાર્બાઇડ ઉત્પન્ન થાય છે.
CaO(c) + 3C → CaC2(l) + CO(g) DH = + 466 kJ/મોલ
કાર્બનના સ્રોત તરીકે કોક, ઍન્થ્રેસાઇટ, અથવા પેટ્રોલિયમ કોક વપરાય છે, પણ સામાન્ય રીતે કોક વધુ ઉપયોગમાં લેવાય છે. તે વધુ સઘન (compact), ઓછા ભસ્મ-અંશ(ash content)વાળો, નીચું પ્રજ્વલનબિંદુ (ignition point) તથા ઊંચા વિદ્યુતઅવરોધવાળો હોવો જોઈએ. આથી ભઠ્ઠીમાંના ભરણનો જથ્થો ઊર્જાના વહનનો ભારે પ્રતિરોધ કરશે. આ ઊર્જા સંકેન્દ્રિત થતાં તે ઝડપી અને સંપૂર્ણ પ્રક્રિયામાં પરિણમશે. આમાં ફૉસ્ફરસ ન હોવો જોઈએ; કારણ કે તે કૅલ્શિયમ ફૉસ્ફાઇડ ઉત્પન્ન કરે છે; જે પાણી સાથે પ્રક્રિયા કરી ફૉસ્ફિન નામનો ઝેરી વાયુ મુક્ત કરે છે. કળીચૂનો મેળવવા 97 % કૅલ્શિયમ કાર્બોનેટ ધરાવતા ચૂના-પથ્થર- (limestone)ને બાળવામાં આવે છે. મૅગ્નેશિયા, સિલિકા અને લોહ જેવી અશુદ્ધિઓ ઉત્પાદનમાં મુશ્કેલી ઊભી કરે છે અને ઓછી શુદ્ધ નીપજ આપે છે.
કાર્બાઇડ ભઠ્ઠી એ ખરેખર ચાપ-પ્રતિરોધ-ભઠ્ઠી નથી પણ તે ચાપ-ભઠ્ઠીમાંથી વિકસાવાઈ છે. ભઠ્ઠી પોલાદના કવચની બનેલી હોય છે અને તેની બાજુની દીવાલો સામાન્ય અગ્નિસહ ઈંટો(firebriek)ના અસ્તરવાળી; જ્યારે તેનું તળિયું કાર્બનના ખંડો (blocks) અથવા ઍન્થ્રેસાઇટ વડે ઢંકાયેલું હોય છે; જે અત્યંત ગરમ, આલ્કેલાઇન પરિસ્થિતિ સામે ટકી શકે છે. મોટાભાગની ભઠ્ઠીઓમાં ત્રણ ફેઝ(ત્રિક પ્રાવસ્થા, three phase)વાળા વીજપ્રવાહનો ઉપયોગ થાય છે. કવચમાં ત્રણ ઊભા વીજધ્રુવો લટકાવેલા હોય છે. આમાં જે સુધારા થયા છે તેમાં સંવૃત (closed) ભઠ્ઠી કે જેમાં પ્રક્રિયામાં ઉદભવતો બધો જ કાર્બન મૉનૉક્સાઇડ એકઠો કરી તેનો ઉપયોગ કરવામાં આવે છે તે તથા સોડરબર્ગના સતત સ્વ-પક્વ (self backing) વીજધ્રુવોનો સમાવેશ થાય છે. આને લઈને ઊંચી ક્ષમતાવાળી ભઠ્ઠીઓ શક્ય બની છે. ભઠ્ઠીઓની ક્ષમતા-પરાસ (capacity range) 18થી 65 MJ અથવા વધુ હોય છે. 90 MJની ત્રણ ફેઝની અંશ-નિષ્કાસન(tapping)-ભઠ્ઠી રોજના 180 ટન જેટલા માલનું ઉત્પાદન કરે છે. એક ટન કાર્બાઇડ માટે અંદાજે 860 કિગ્રા. ચૂનો, 590 કિગ્રા. કોક, 16 કિગ્રા. વીજધ્રુવ-લૂગદી (electrode paste) અને 108 MJ જેટલી ઊર્જા વપરાય છે. ભઠ્ઠીમાં ચૂનો અને કોક સતત ઉમેરતાં જવામાં આવે છે, જ્યારે પ્રવાહી નીપજને 5 ટન ક્ષમતાવાળા ભરતર લોખંડના દ્રુતશીત-પાત્રો (chill pots) દ્વારા સતત અથવા આંતરે-આંતરે બહાર કાઢી લેવામાં આવે છે. કાર્બાઇડને ઠંડો કરી, ભાંગી, ચાળી, માપ પ્રમાણે અલગ કરી 4.5થી 100 કિગ્રા. ક્ષમતાવાળાં સ્ટીલનાં પીપોમાં પૅક કરવામાં આવે છે.
3. ફૉસ્ફરસ : ફૉસ્ફરસનું ઉત્પાદન વિદ્યુતભઠ્ઠીમાં અપચયન પ્રક્રિયા દ્વારા કરવામાં આવે છે. આ માટે કૅલ્શિયમ ફૉસ્ફેટ Ca3(PO4)2; રેતી (સિલિકા) (SiO2) અને કોક(C)ના મિશ્રણને ભઠ્ઠીમાં ઓરવામાં આવે છે. તેનાં કાર્બનના બે વીજધ્રુવો વચ્ચે વિદ્યુતચાપ પસાર કરતાં 1,300° સે.થી 1,500° સે. જેટલું ઊંચું તાપમાન મળે છે. આ તાપમાને મિશ્રણ સુવાહક બને છે અને ભઠ્ઠીમાં ધ્રુવો વચ્ચે વીજપ્રવાહ વહી શકે છે. કૅલ્શિયમ ફૉસ્ફેટ અને રેતી વચ્ચે પ્રક્રિયા થતાં કૅલ્શિયમ સિલિકેટ અને ફૉસ્ફરસ પૅન્ટૉક્સાઇડ (P2O5) બને છે. P2O5નું કાર્બન વડે અપચયન થતાં ફૉસ્ફરસ ઉત્પન્ન થાય છે.
Ca3(PO4)2 + 3SiO2 + 5C → 3CaSiO3 + 2P + 5CO
ફૉસ્ફરસની બાષ્પ અને કાર્બન મૉનૉક્સાઇડને ઠંડા પાણીમાં પસાર કરવાથી ફૉસ્ફરસ ઘન-સ્વરૂપે મળે છે. ધાતુમળ (slag) તરીકે ઓળખાતો કૅલ્શિયમ સિલિકેટ ભઠ્ઠીના તાપમાને પ્રવાહી રૂપે હોવાથી તેને બહાર કાઢી લેવામાં આવે છે. તેને બેલાસ્ટ (ballast) તરીકે વેચવામાં આવે છે.
જો કાચા માલ તરીકે ફૉસ્ફેટી ખડક (phosphate rock) વાપરવામાં આવ્યો હોય તો પ્રક્રિયા નીચે પ્રમાણે થાય છે :
CaF2 · 3Ca3(PO4)2 + 9SiO2 + 15C → CaF2 + 9CaSiO3 + 6P + 15CO.
4. સિલિકન : સિલિકા (શુદ્ધ રેતી) અને કોકના મિશ્રણને વિદ્યુત-ભઠ્ઠીમાં ગરમ કરતાં કાર્બન દ્વારા સિલિકાનું અપચયન થઈ સિલિકન મળે છે :
SiO2 + 2C → Si + 2CO
જો કોક વધારે પ્રમાણમાં હોય તો સિલિકન કાર્બાઇડ (SiC) ઉત્પન્ન થાય છે (Si + C → SiC).
સંગલિત (fused) સિલિકા અથવા કાચમય (vitreous) સિલિકા : રાસાયણિક ઉદ્યોગોમાં બાંધકામ માટેના દ્રવ્ય તરીકે તે ઘણો ઉપયોગી પદાર્થ છે. ઊંચા તાપમાને સિલિકન ટેટ્રાક્લોરાઇડના તાપ-અપઘટનથી અથવા ક્વાર્ટ્ઝ કે શુદ્ધ રેતીને પિગાળીને તે બનાવાય છે. આ માટે વિદ્યુતભઠ્ઠીમાં સંવિરચન (fabrication) તાપમાન સુધી તેને ગરમ કરવામાં આવે છે.
સંશ્લેષિત ક્વાર્ટ્ઝ સ્ફટિકો : ઉષ્ણજલીય (hydrothermal) પ્રવિધિ વડે 1 M સોડિયમ હાઇડ્રૉક્સાઇડમાં બનાવેલા સિલિકાના અતિસંતૃપ્ત (supersaturated) દ્રાવણમાંથી આ મેળવી શકાય છે. આ માટે દ્રાવણને બીજ-સ્ફટિક-ક્વાર્ટ્ઝ(seed crystal quartz)ની પ્લેટોના સંપર્કમાં 206 MPaના દબાણે, 400° સે. જેટલા તાપમાને ત્રણ અઠવાડિયાં સુધી રાખવામાં આવે છે. વિશિષ્ટ પ્રેષતાપન યંત્રો-(autoclaves)માં તેમને વિકસાવવામાં આવે છે. તેમાં દ્વિક્ષેત્રી (two zones) વિદ્યુતીય તાપન-પ્રણાલી હોય છે. ઊંચા તાપમાનવાળો ભાગ ક્વાર્ટ્ઝની નાની ચીપો(chips)ને દ્રાવણમાં લઈ જવા માટેના વિલયન(dissolving)-ક્ષેત્ર તરીકે અને બીજો તેનાથી લગભગ 55° સે. ઓછા તાપમાનવાળો ભાગ ક્વાર્ટ્ઝની બીજ-પ્લેટો પર સ્ફટિકોના વર્ધન માટે વપરાય છે. રડાર, સોનાર (sonar), ટેલિવિઝનનાં ટ્રાન્સમિટરો અને ટેલિફોન-સંચાર માટે આ સ્ફટિકો અગત્યના છે.
5. કૃત્રિમ ગ્રૅફાઇટ અને વીજધ્રુવો : 1896માં ઈ. જી. અચેસને કૃત્રિમ ગ્રૅફાઇટ બનાવવાની પ્રથમ સફળ પ્રવિધિ શોધેલી. ભઠ્ઠીમાં કોક અથવા ઍન્થ્રેસાઇટ-કોક અથવા પેટ્રોલિયમ-કોક અને રેતીના મિશ્રણને લેવામાં આવે છે. કાર્બનના વીજધ્રુવો દ્વારા વિદ્યુત પસાર કરતાં તાપમાન 3,000° સે. જેટલું થાય છે. આ તાપમાને કોક અને રેતી વચ્ચે પ્રક્રિયા થઈ પ્રથમ, આગળ જણાવ્યા પ્રમાણે, કૅલ્શિયમ કાર્બાઇડ ઉત્પન્ન થાય છે. આ સિલિકન કાર્બાઇડનું વિઘટન થવાથી ગ્રૅફાઇટ રૂપે કાર્બન છૂટો પડે છે :
SiO2 + 3C (કોક) → SiC + 2CO
SiC → Si + C (ગ્રૅફાઇટ)
અપરરૂપી પરિવર્તન માટેની પ્રક્રિયા નીચે પ્રમાણે દર્શાવી શકાય :
C (amorph) → C (ગ્રૅફાઇટ) ΔH = −10·5 kJ
આ માટે વપરાતી ભઠ્ઠીનો અંતર્ભાગ (core) જેનું ગ્રૅફાઇટીકરણ કરવાનું હોય તેવા કોકનો બનેલો હોય છે અને તેની ફરતે વિસંવાહન (insulation) માટે રેતી, કોક અને લાકડાનો વહેર ભરેલો હોય છે. ભઠ્ઠીનું તળિયું અને છેડાઓ કૉંક્રીટના હોય છે. હવા સાથે સંપર્કમાં રહેતાં વીજધ્રુવો બળી ન જાય તે માટે તેમનું તાપમાન ઘટાડવા છેડાના ભાગમાં શીતન-નળીઓ આવેલી હોય છે. બાજુની દીવાલો છૂટા ખંડો (blocks) અને પ્લેટોની બનેલી હોય છે અને દરેક વખતે તેમને તોડી પાડવામાં આવે છે. દ્રવ્યનું સરેરાશ ભરણ 23,000થી 90,000 કિગ્રા. જેટલું હોય છે અને તેના વીજ-અવરોધને કારણે 3,000° સે. સુધીનું તાપમાન શક્ય બને છે. જેમ જેમ કોકનું ગ્રૅફાઇટીકરણ થતું જાય તેમ તેમ અવરોધ-ઘટનાને લીધે વોલ્ટેજ 200 Vથી ઘટીને 40 V થાય છે. ઊંચા તાપમાનને કારણે મોટાભાગની ધાત્વિક અશુદ્ધિઓનું બાષ્પીભવન થઈ જાય છે. ઉત્પાદનના એક ફેરા (cycle) માટે 22 જેટલા દિવસ લાગે છે. (ભઠ્ઠીમાં ભરણું ભરવા માટે 1 દિવસ; વિદ્યુતપ્રવાહ ચાલુ રાખવાના 4થી 5 દિવસ; શીતન (cooling) આશરે 14 દિવસ; ખાલી કરવા માટે 2 દિવસ). શીતન બાદ ભઠ્ઠીને તોડી પાડી તેમાંથી ગ્રૅફાઇટીકરણ પામેલો કાર્બન બહાર કાઢી લેવામાં આવે છે. વિસંવાહી રેતી, કોક અને કૅલ્શિયમ કાર્બાઇડ જેવાં સંદૂષણ ફરી ફરીને વપરાય છે. 1963 પછી ભઠ્ઠીમાં એકદિશી વીજપ્રવાહ(D.C.)નો ઉપયોગ પણ થવા માંડ્યો છે.
અસ્ફટિકીય (amorphous) કાર્બન વીજધ્રુવોના ઉત્પાદન માટે પેટ્રોલિયમ કોક કે ઍન્થ્રેસાઇટ કોકને ખાંડી ગરમ સ્થિતિમાં ડામર-બંધક (pitch binder) સાથે મિશ્ર કરવામાં આવે છે. મળતા નરમ દ્રવ્યને બહિ:સ્ફુટિત કરવામાં આવે છે અથવા વીજધ્રુવના આકારમાં ઢાળવામાં આવે છે. આ કાચા વીજધ્રુવોને ત્યારબાદ વાયુ-પ્રજ્વલિત (gas fired) અથવા વિદ્યુતભઠ્ઠીમાં 950° સે. તાપમાને પકવવામાં આવે છે.
6. મિશ્રધાતુઓ : મિશ્રધાતુ (alloy) એ બે અથવા વધુ ધાતુઓનું ઘન દ્રાવણ (solid solution) છે; જેમ કે, લોહ-મિશ્રધાતુઓ (iron alloys) એ લોહયુક્ત ધાતુઓનું ઘન દ્રાવણ છે. ફેરો-ઍલૉય એ પોલાદ ઉદ્યોગ માટે આવશ્યક એવો ધાત્વિક અપરિષ્કૃત (raw) દ્રવ્યોનો સમૂહ છે. તેના ઉત્પાદન માટે નિમગ્નિત ચાપ (submerged arc) ભઠ્ઠી વપરાય છે. ફેરોસિલિકન બનાવતી આવી ભઠ્ઠી લગભગ 7.9 મી. વ્યાસ ધરાવતી 3 મી. ઊંડી હોય છે અને તેમાં કાર્બનના ત્રણ વીજધ્રુવો મૂકવામાં આવે છે. દર કલાકે તે 1.8 મૅટ્રિક ટન જેટલી મિશ્રધાતુ ઉત્પન્ન કરે છે. થોડા થોડા સમયને આંતરે ભઠ્ઠીના મથાળેથી સિલિકા, કોક અને લોખંડની કતરણ (turnings) ઉમેરવામાં આવે છે. ભઠ્ઠીને તળિયેથી અવારનવાર ફેરોસિલિકનને બહાર કાઢી લેવામાં આવે છે. જરૂરી ઉષ્મા ભરણના વીજાવરોધ અને વિદ્યુતચાપ દ્વારા આપવામાં આવે છે. ઢાળકામાં ઠારેલી મિશ્રધાતુને ખાંડી યોગ્ય માપના ટુકડામાં ફેરવવામાં આવે છે. કોક સિલિકાનું સિલિકનમાં અપચયન કરે છે, જે આયર્ન સાથે ભળી ફેરો ઍલૉય બનાવે છે :
SiO2 + 2C → Si + 2CO.
તેના પ્રકાર પ્રમાણે ફેરોસિલિકન 47 – 52 % કે 73 – 78 % સિલિકન ધરાવે છે. ફેરોમૅન્ગેનીઝ, ફેરોક્રોમિયમ, ફેરોમોલિબ્ડેનમ, ફેરોવેનેડિયમ, ફેરોટાઇટેનિયમ વગેરે અન્ય લોહયુક્ત મિશ્રધાતુઓ છે.
આવી રીતે અન્ય ધાતુઓની મિશ્રધાતુઓ પણ બનાવી શકાય છે.
પ્ર. બે. પટેલ