પોલાદ : લોખંડ (Fe) અને ૦.૦2થી 1.7% સુધી કાર્બન (C) ધરાવતી મિશ્રધાતુ. પોલાદના ગુણધર્મો પર કાર્બન ભારે અસર કરતું તત્ત્વ હોઈ તેનું પ્રમાણ ૦.૦1%ની ચોકસાઈ સુધી દર્શાવવું આવશ્યક છે. ભરતર (cast) લોખંડમાં સામાન્ય રીતે 4.5% C હોય છે. જોકે લોખંડમાં કાર્બનની મિશ્ર થવાની સીમા 6.67% ગણાય છે. કાર્બન ઉમેરવાથી લોખંડ મજબૂત અને સખત પણ બરડ બનતું હોઈ કાર્બનના પ્રમાણને જાળવી રાખવું આવશ્યક છે. પોલાદ જે પ્રકારના ઉપયોગમાં લેવાનું હોય તેને અનુરૂપ ગુણધર્મો તેમાં લાવવા લોખંડ અને કાર્બન ઉપરાંત અન્ય ધાતુઓ પણ ઉમેરવામાં આવે છે. તેમાં સિલિકોન, ફૉસ્ફરસ અને સલ્ફર જેવાં તત્ત્વો પણ હોય છે.
પોલાદની નીચી કિંમત અને ઉષ્મા-માવજતની તેની સાનુકૂળતાને કારણે તેનું ઉત્પાદન મોટા પ્રમાણમાં થાય છે. જુદા જુદા સંવિરચન (fabrication) માટે તેને નરમ કરી શકાય છે. વળી પછીથી સખત પણ બનાવી શકાય છે. આ માટે પોલાદના બે પ્રકાર કારણભૂત છે : α-આયર્ન (ફેરાઇટ) તથા ϒ-આયર્ન (ઑસ્ટેનાઇટ). આ ઉપરાંત એક મિતસ્થાયી (metastable) પ્રાવસ્થા (phase), માર્ટેન્સાઇટ પણ હોય છે. નીચા તાપમાને લોહના પરમાણુઓ કાયકેન્દ્રિત (અંત:કેન્દ્રિત) (body centered) જાલક ફેરાઇટ સ્વરૂપે હોય છે. તેનું રૂપાંતરણ થતાં તે સ્ફટિકમય ફલક-કેન્દ્રિત (face centered) જાલકમાં (ઑસ્ટેનાઇટ રૂપમાં) ફેરવાય છે. આ બંને સ્વરૂપો નરમ, તન્ય તથા ઓછી પ્રબળતા(low strength)વાળાં હોય છે. આમાં ફેરાઇટ ચુંબકીય છે, જ્યારે ઑસ્ટેનાઇટ બિન-ચુંબકીય (nonmagnetic) છે. ગરમ કરવાથી ફેરાઇટ (તથા સિમેન્ટાઇટ, Fe3C) ઑસ્ટેનાઇટમાં પરિવર્તન પામે છે. તેમને ઠંડા પાડતાં ફરી મૂળ સ્થિતિ પ્રાપ્ત કરે છે. માર્ટેન્સાઇટ અંત:કેન્દ્રિત સમચતુષ્ફલકીય સંરચના ધરાવે છે. તે પોલાદને વધુ સખ્તાઈ તથા સામર્થ્ય બક્ષે છે, પણ બરડ બનાવે છે.
પોલાદમાં કાર્બન ઉપરાંત અન્ય તત્ત્વો ઉમેરી વિવિધ પ્રકારનાં પોલાદ બનાવવામાં આવે છે. સામાન્ય રીતે પોલાદ બે પ્રકારનાં હોય છે : (1) સાદું કાર્બન-પોલાદ (plain carbon steel), (2) મિશ્રધાતુ-પોલાદ (alloy steel).
(1) સાદું કાર્બન પોલાદ : આ પોલાદ આર્થિક રીતે પરવડતું હોઈ તેનું ઉત્પાદન સૌથી વધુ થાય છે. તેમાં ફૉસ્ફરસ (P), સલ્ફર (S), સિલિકોન (Si) તથા મૅન્ગેનીઝ (Mn) પણ હોય છે. S અને P અશુદ્ધિ રૂપે આવે છે. Si વાયુનિષ્કાસક (degasifier) તરીકે ઑક્સિજન દૂર કરવા તથા નિપિંડ (સિલિકા) (ingot) સુદૃઢતા વધારવા ઉમેરવામાં આવેલ હોય છે. Mnને FeSની વિપરીત અસર દૂર કરવા ઉમેરવામાં આવે છે. તે પોલાદની બરડતા ઘટાડે છે.
સાદા કાર્બન-સ્ટીલની કેટલીક મર્યાદાઓ છે. તેનામાં અધિકતમ પ્રાબલ્ય, કઠોરક્ષમતા (hardenability), કાટ-પ્રતિરોધકતા, શ્રાંતિ-પ્રતિરોધ (fatigue resistance) અને સરકણ(creep)પ્રતિરોધ જેવા ગુણ નબળા અથવા ઓછા હોય છે. આ પ્રકારના પોલાદ પર કાર્બનની અસર વધુ થતી હોય છે. તેને ત્રણ ભાગમાં વહેંચવામાં આવે છે :
(i) ઓછા કાર્બનવાળું પોલાદ (૦.3%થી ઓછો કાર્બન), (ii) મધ્યમ કાર્બનવાળું પોલાદ (૦.3થી ૦.7% કાર્બન), (iii) વધુ કાર્બનવાળું પોલાદ (૦.7થી 1.4% કાર્બન). જેમ કાર્બનનું પ્રમાણ વધે તેમ તનન-સામર્થ્ય અને કઠિનતા વધે, પરંતુ શતાંશ પ્રતાન ઘટે. ઓછા કાર્બનવાળું પોલાદ પ્લેટો, પતરાં, સ્ક્રૂ, ચાકીઓ, તાર વગેરે માટે; જ્યારે મધ્યમ કાર્બનવાળું પોલાદ ગાડીના પાટા, શાફ્ટ, સ્પિન્ડલો, દાંતાચક્રો, બૉઇલરની પ્લેટો વગેરે માટે વપરાય છે. વધુ કાર્બનવાળું પોલાદ સ્પ્રિંગો, ડાઇબ્લૉક, ક્લચ-પ્લેટો, છરી, છીણી, ફરશી (chisel), આંટા પાડવા માટેના ટૅપ વગેરે માટે વપરાય છે.
(2) મિશ્રધાતુ-પોલાદ : સાદા પોલાદના ગુણધર્મો સુધારવા માટે તેમાં નિકલ (Ni), ક્રોમિયમ (Cr), મૅન્ગેનીઝ (Mn), કોબાલ્ટ (Co), ટંગ્સ્ટન (W), વેનેડિયમ (V), મોલિબ્ડેનમ (Mo), સિલિકોન (Si) વગેરે તત્ત્વો ઉમેરવામાં આવે છે. આવા પોલાદને મિશ્રધાતુ પોલાદ (alloy steel) કહે છે. આથી સાદા પોલાદની નબળાઈઓ દૂર કરી શકાય છે. ખાસિયતો અને ઉપયોગો પ્રમાણે મિશ્રધાતુ-પોલાદનું નીચે પ્રમાણે વર્ગીકરણ કરવામાં આવે છે :
(i) મુક્ત કર્તન પોલાદ (free cutting steels) : આવું પોલાદ Mn અને S ધરાવે છે. તેનું કર્તન સહેલાઈથી થઈ શકે છે.
(ii) મશીન-નિર્માણ પોલાદ (machine structure steels) : પોલાદમાં સામાન્ય રીતે ૦.2થી ૦.5% C, ૦.35થી 1.9% Mn, ૦.5થી 4.5% Ni, ૦.3થી 1.5% Cr અને ૦.2થી ૦.7% Mo હોય છે. આ પોલાદ શાફ્ટ, સ્પિન્ડલ, દાંતાચક્ર, વાલ્વ, સ્પ્રિંગ, બેરિંગની રિંગો વગેરે મશીનોના ભાગ બનાવવા માટે બહોળા પ્રમાણમાં વપરાય છે.
(iii) ઓજારી પોલાદ (tool steels) : આ પ્રકારના પોલાદમાં મુખ્યત્વે Cr, W, Mo અને V ઉમેરવામાં આવે છે. તેને લીધે ઉચ્ચ તનન-સામર્થ્ય સાથે ઉચ્ચ કઠિનતા અને ઉચ્ચ ઘસારા-પ્રતિરોધ (high wear resistance) મળી રહે છે. આ માટે જરૂરી ઉષ્મા-માવજત (heat treatment) આપવામાં આવે છે. આ પોલાદ ત્રણ પ્રકારનું હોય છે : શીતકાર્ય ઓજારી પોલાદ, ઉષ્ણકાર્ય ઓજારી પોલાદ અને હાઇસ્પીડ પોલાદ. તે અતિશય સખત હોવાથી ડાઇ તથા વિવિધ સાધનો બનાવવા વપરાય છે. તે ઘસારા સામે પ્રતિકાર તથા આંચકા-પ્રતિરોધ (shock resistance) કરનારું છે અને ઊંચા તાપમાને સખત રહે છે. તેમાં જરૂરિયાત મુજબ ૦.35થી 3×5% C, 3% સુધી Mn, 2% જેટલું Si, 4.25% જેટલું Ni, 12% Cr, 5% V, 18% W, 9.5% Mo તથા 12% સુધી Co ઉમેરવામાં આવે છે.
(iv) લોહચુંબકીય પોલાદ (magnetic steels) : આ પોલાદ બે પ્રકારનું હોય છે : સખત લોહચુંબકીય અને નરમ લોહચુંબકીય. સખત લોહચુંબકીય પોલાદ સ્થાયી લોહચુંબક માટે, જ્યારે નરમ લોહચુંબકીય પોલાદ ટ્રાન્સફૉર્મરના કેન્દ્રભાગ (core) તથા મોટરના ધ્રુવો (poles) માટે વપરાય છે. પોલાદની સામાન્ય અને ચુંબકીય સખતાઈ વચ્ચે સંબંધ છે. જેમ સામાન્ય સખતાઈ વધારે તેમ ચુંબકીય સખતાઈ પણ વધારે. નરમ પોલાદ ચુંબકીય દૃષ્ટિએ પણ નરમ હોય છે. સ્થાયી લોહચુંબકત્વ માટે ઍલ્યુમિનિયમ, કોબાલ્ટ, નિકલ, ક્રોમિયમ, ટંગ્સ્ટન વગેરે ઉમેરવામાં આવે છે. આ પ્રકારનું AlNiCo પોલાદ ઘણું જાણીતું છે.
ટ્રાન્સફૉર્મર, ડાઇનેમો અને મોટરના ધ્રુવો માટે વપરાતા નરમ લોહચુંબકીય પોલાદમાં 3થી 4% જેટલું સિલિકોન હોય છે. આથી તે સિલિકોન-પોલાદ પણ કહેવાય છે.
(v) સ્ટેઇનલેસ સ્ટીલ (stainless steels) : લોખંડમાં 12 % કે તેથી વધુ Cr ઉમેરવાથી આ પ્રકારનું પોલાદ બને છે. તેમાં Ni, Mo, Cu વગેરે પણ ઉમેરવામાં આવે છે. ક્ષારણ તથા ઉપચયન-પ્રતિકાર માટે તે જાણીતું છે. તેનો આ ગુણ ક્રોમિયમને આભારી છે. ઑક્સિજન ક્રોમિયમ સાથે સંયોજાઈ અપ્રવેશ્ય (imprevious) ઑક્સાઇડ બનાવે છે. Cr2O3નું આ પાતળું પડ મજબૂત, ટકાઉ અને ક્ષારણ-પ્રતિકારક હોય છે. ડેરી, રસાયણ-ઉદ્યોગ, કટલરીની ચીજો, વાઢકાપનાં ઓજારો, તેમજ ઘરવપરાશનાં વાસણો (18 : 8 Cr-Ni પોલાદ) વગેરેમાં આ પોલાદ વધુ વપરાય છે. જો કાર્બનનું પ્રમાણ વધે તો વાસણોમાં તિરાડ પડે છે.
સ્ટેઇનલેસ સ્ટીલ ત્રણ પ્રકારનાં હોય છે : માર્ટેન્સાઇટ સ્ટેઇનલેસ સ્ટીલમાં 12થી 18% Cr અને ૦.1થી 1.2% C હોય છે. ફેરાઇટિક સ્ટેઇનલેસ સ્ટીલમાં 12થી 27% Cr, 4.5% સુધી Al, ૦.35% સુધી C હોય છે તે ઑટોમૉબાઇલના ભાગો બનાવવામાં વપરાય છે. ઑસ્ટેનિટિક સ્ટેઇનલેસ સ્ટીલમાં 16થી 26% Cr, 6થી 22% Ni ઉપરાંત C, Mo, Ti, Cu, Mn પણ ઉમેરવામાં આવે છે.
(vi) ઉષ્મારોધક પોલાદ : સામાન્યત: ફેરાઇટિક, માર્ટેન્સિટિક અને ઑસ્ટેનિટિક સ્ટેઇનલેસ સ્ટીલ ઉષ્મારોધક હોય છે.
સૌથી નવા પ્રકારના માર્ટેન્સિટિક સ્ટીલમાં 18થી 25% Ni ઉપરાંત ઓછાવત્તા અંશે Al, Ti, Nb ઉમેરાય છે. તેને મેરેજિંગ (maraging) સ્ટીલ પણ કહે છે.
નિકલ ધરાવતાં સ્ટીલ ઊંચી પ્રબળતા (strength)વાળું તથા કાટ કે ક્ષારણ સામે પ્રતિકારક હોય છે. ટંગ્સ્ટન સ્ટીલ ધાતુ કાપવાનાં ઓજારો [દા. ત., કરવતો, શારડી, (drill)] બનાવવામાં વપરાય છે; કારણ કે ખૂબ ગરમ થાય તોપણ તે તેની સખતાઈ કે તીક્ષ્ણ ધાર ગુમાવતું નથી.
પોલાદના ગુણધર્મો તેને અપાતી વિવિધ ઉષ્મા-માવજત ઉપર આધાર રાખે છે. નરમ પોલાદ(mald steel)માં વધુ કાર્બન ઉમેરતાં તેનું તનન-સામર્થ્ય (tensile strength) વધે છે. જો પોલાદને લાલચોળ થાય ત્યાં સુધી તપાવી ઠંડા પાણીમાં ઝબકોરવામાં આવે તો તે સખત અને બરડ (brittie) બને છે.
હવે તેને ફરી જુદા જુદા તાપમાને ગરમ કરવામાં આવે તો તેના ગુણધર્મો આ તાપમાન ઉપર આધાર રાખે છે. આ વિધિને લોખંડને પાણી ચડાવવું (tempering) કહે છે. આ રીતે લોખંડની સપાટી ઉપર તેના ઑક્સાઇડની પાતળી ફિલ્મના રંગ ઉપરથી તેનું આ તાપમાન અનુમાનિત કરી શકાય છે.
દા. ત.,
23૦o સે.; આછા ફિક્કા પીળા (straw) રંગનું | રેઝર બ્લેડ બનાવવા માટે |
255o સે.; ભૂખરું પીળું | ચાકુ તથા કુહાડી માટે |
277o સે.; જાંબુડી | કટલરી સાધનો માટે |
288o સે.; ચમકતા વાદળી રંગનું | ઘડિયાળની સ્પ્રિંગ તથા તલવાર માટે |
29૦થી 316o સે.; ઘેરું વાદળી | ફરશી (chisel) તથા મોટી કરવત માટે |
Ni + Cr ધરાવતું પોલાદ મજબૂત બખ્તર માટે વપરાય છે. તેલના કૂવાના ખોદકામમાં વપરાતા સિલિંડર બોર માટે પોલાદમાં 1% ઍલ્યુમિનિયમ ઉમેરવામાં આવે છે અને તે 45૦થી 5૦૦o સે.એ. એમોનિયાના વાતાવરણમાં ગરમ કરીને બનાવાય છે. આ વિધિને નાઇટ્રાઇડિંગ (nitriding) કહે છે.
પોલાદનું ઉત્પાદન : પોલાદ બે રીતે બનાવી શકાય : (i) શુદ્ધ ઘડતર (wrought) લોખંડમાં સંયોજિત કાર્બનનું પ્રમાણ વધારીને, તથા (ii) ઢાળેલા (cast) લોખંડમાંથી કાર્બન તથા અન્ય અશુદ્ધિઓ દૂર કરીને. અશુદ્ધિઓ દૂર કરવા માટેની બે વિધિઓ ખૂબ પ્રચલિત છે :
(i) બેસિમર વિધિ : હેન્રી બેસિમરે 1855માં આ વિધિ શોધી હતી.
(ii) સિમેન્સ-માર્ટિન ઓપન હાર્થ વિધિ (1864) : આ રીત વધુ વપરાશમાં છે.
ખાસ પ્રકારનું ઉચ્ચ ગુણવત્તાવાળું પોલાદ બનાવવા માટે હમણાંથી વિદ્યુત-ભઠ્ઠી વિધિ પણ વપરાશમાં છે.
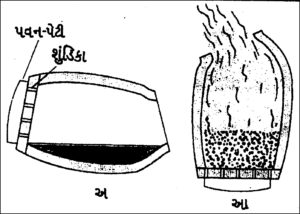
આકૃતિ 1 : બેસિમર પરિવર્તક : (અ) ભરણ અને સ્રવન (charging and pouring); (આ) ધમવણી (blowing)
બેસિમર વિધિ : ભરતર લોખંડમાંથી પોલાદ બનાવવાની આ વિશિષ્ટ વિધિ છે. વાતભઠ્ઠીમાંથી મળેલા પીગળેલા લોખંડને બેસિમર પરિવર્તક(converter)માં લેવામાં આવે છે. તે એક મોટા ઈંડાના આકારનું, નીચેના ભાગમાં છિદ્રોવાળું પાત્ર છે. આ છિદ્રો દ્વારા પીગળેલ ધાતુમાં હવા ફૂંકવામાં આવે છે. પરિણામે કાર્બનનું કાર્બન-ડાયૉક્સાઇડમાં ઉપચયન થાય છે. આ પીગળેલ ધાતુમાં હવે આવશ્યક પ્રમાણમાં સ્પીગેલ (spiegel) ઉમેરવામાં આવે છે. કેટલાક આધુનિક પરિવર્તકોમાં હવાને બદલે ઑક્સિજન તથા બાષ્પને પીગળેલ ધાતુમાં ફૂંકવામાં આવે છે, જેથી પોલાદ દ્વારા નાઇટ્રોજનનું શોષણ અટકાવી શકાય.
આ વિધિને VLN (very low nitrogen) વિધિ કહે છે. હવે બેસિમર વિધિને બદલે બૅઝિક ઑક્સિજન વિધિ (BOP) વપરાવા લાગી છે. લોખંડના ભંગાર (scrap) તથા પીગળેલા કાચા લોખંડને એક ઢળતી (tilting) ભઠ્ઠીમાં લઈ તેમાં ઊંચા દબાણે ઑક્સિજન ફૂંકવામાં આવે છે.
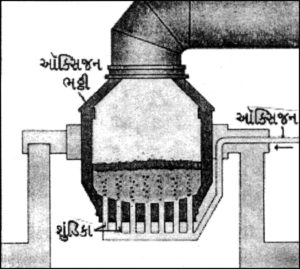
આકૃતિ 2 : BOP વિધિ
સિમેન્સ-માર્ટિન ઓપન હાર્થ વિધિ : આ વિધિમાં કાચા લોખંડ તથા પોલાદના ભંગારને અથવા લોખંડના અયસ્કને નિયત ગણતરી કરેલા પ્રમાણમાં પ્રોડ્યૂસર ગૅસ સાથે ભઠ્ઠીના હાર્થમાં ગરમ કરીને બનાવાય છે.
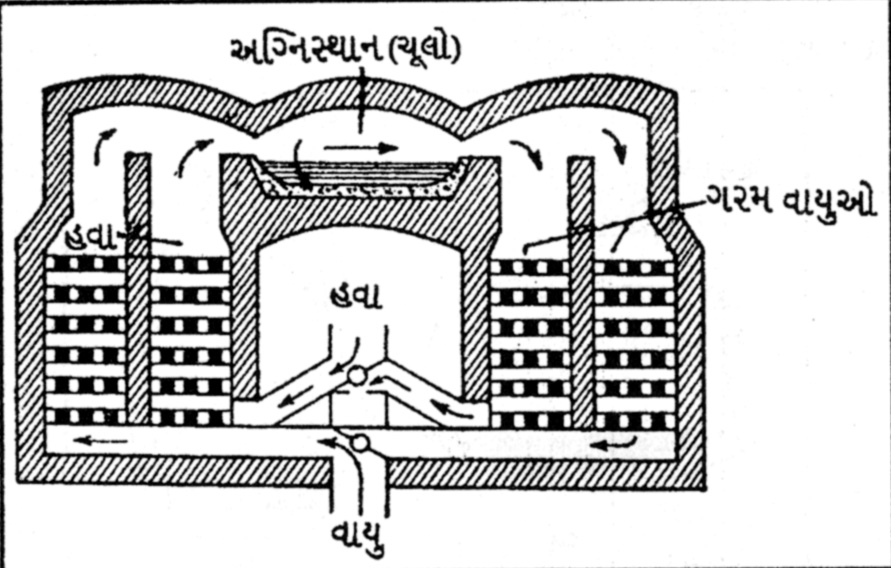
આકૃતિ 3 : સિમેન્સ-માર્ટિન ઓપન હાર્થ વિધિ
વિદ્યુત-ભઠ્ઠી વિધિમાં લોખંડનો ભંગાર અને મિશ્ર કરવાની ધાતુઓ લેવામાં આવે છે. વીજધ્રુવો દ્વારા શક્તિશાળી વિદ્યુતચાપ ભારેલી સામગ્રી(charge material)માંથી પસાર થઈ પુષ્કળ ગરમી ઉત્પન્ન કરે છે. આથી ધાતુ પીગળે છે અને પોલાદ બનાવવાની રાસાયણિક ક્રિયાઓને પ્રેરે છે.
પોલાદની વિવિધ જાતો દર્શાવવાની રીતો : પોલાદમાં ઘણી ધાતુઓ જુદા જુદા પ્રમાણમાં હોય છે. તેમનું પ્રમાણ પોલાદ જે ઉપયોગ માટે વાપરવાનું હોય તેના ઉપર આધાર રાખે છે. દરેક દેશમાં પોલાદને દર્શાવવાની પ્રચલિત રીતો હોય છે. યુ.એસ.ની SAE અને AISI રીતમાં પોલાદને ચાર આંકડા દ્વારા દર્શાવાય છે; દા.ત., 1૦4૦ સ્ટીલ, 2135 સ્ટીલ. બ્રિટનમાં En શ્રેણી વડે તે દર્શાવાય છે; દા.ત., En 2૦, En 4૦. ભારત, જર્મની અને રશિયામાં પોલાદનું તનન-સામર્થ્ય અને તેમાં રહેલ ધાતુતત્ત્વો સ્પષ્ટપણે દર્શાવાય છે. દા.ત., St 4૦, C 15, Mn 75 પોલાદ એટલે ૦.15% C, ૦.75% Mnવાળું 4૦ કિગ્રા./મિમી2ના તનન-સામર્થ્યવાળું પોલાદ.
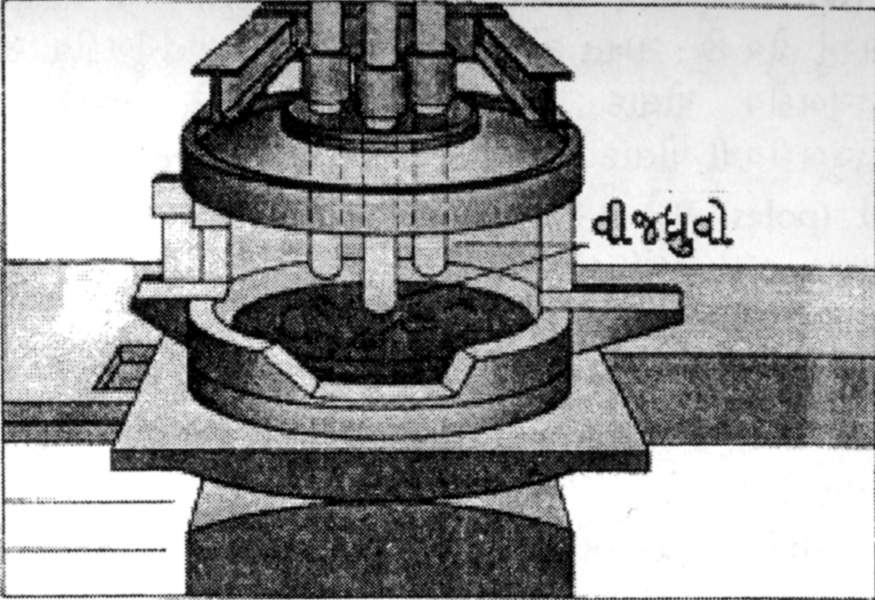
આકૃતિ 4 : વિદ્યુત-ભઠ્ઠી વિધિ : ભરણ (charge) અને વીજધ્રુવો વચ્ચે પ્રબળ વિદ્યુતચાપ ઉત્પન્ન થવાથી ઉદ્ભવતી તીવ્ર ગરમી ભરણને પિગાળે છે અને પોલાદ બનવા માટેની જરૂરી રાસાયણિક પ્રક્રિયાઓને પ્રોત્સાહિત કરે છે.
ભારતમાં પોલાદ-ઉદ્યોગ : ભારતમાં આધુનિક લોખંડ અને પોલાદ ઉદ્યોગની શરૂઆત સૌપ્રથમ કુલ્ટી (પશ્ર્ચિમ બંગાળ) ખાતે 187૦માં બેંગાલ આયર્ન ઍન્ડ સ્ટીલ વર્ક્સની સ્થાપનાથી થઈ. 19૦7માં જમશેદપુર ખાતે તાતા આયર્ન ઍન્ડ સ્ટીલ કું.(TISCO)ની સ્થાપનાથી મોટા પાયા પર પોલાદનું ઉત્પાદન શરૂ થયું. તે પછી 1919માં બર્નપુર ખાતે ઇન્ડિયન આયર્ન ઍન્ડ સ્ટીલ કંપની(IISCO)ની સ્થાપના થઈ. 1923માં જાહેર ક્ષેત્ર(public sector)માંનું પ્રથમ એકમ ભદ્રાવતી ખાતે વિશ્વેશ્વરૈયા આયર્ન ઍન્ડ સ્ટીલ લિ. સ્થપાયું.
સારણી 1 : સ્ટીલ પ્લાન્ટૉની ક્ષમતા
પ્લાન્ટ | કાચું પોલાદ
(’000 ટન) |
વેચાણક્ષમ પોલાદ
(’000 ટન) |
ભિલાઈ
દુર્ગાપુર રૂરકેલા બોકારો ઍલૉય સ્ટીલ પ્લાન્ટ સાલેમ IISCO |
3925
1450 1350 4000 260 – 360 |
3153
250 1212 3156 184 175 406 |
આઝાદી પછી દ્વિતીય પંચવર્ષીય યોજના હેઠળ પ્રત્યેક 1૦ લાખ ઇન્ગોટ ટન-ક્ષમતાનો એક એવા ત્રણ સંયંત્ર (plant) ભિલાઈ, દુર્ગાપુર અને રૂરકેલા ખાતે સ્થપાયા. ખાનગી ક્ષેત્રની બે કંપનીઓ-TISCO અને IISCO-એ તેમની ક્ષમતા વધારીને અનુક્રમે 2૦ લાખ ટન અને 1૦ લાખ ટનની કરવાનું શરૂ કર્યું. પાંચમી પંચવર્ષીય યોજના દરમિયાન બીજાં ત્રણ કારખાનાં સાલેમ (તમિળનાડુ), વિજયનગર (કર્ણાટક) તથા વિશાખાપટનમ્(આંધ્રપ્રદેશ)માં સ્થપાયાં. વળી પોલાદનું ઉત્પાદન કરતા અન્ય નાના એકમો પણ સ્થાપવામાં આવ્યા છે. આજે પચાસ કરતા વધારે એકમો કાર્યરત છે.
સ્ટીલ ઑથોરિટી ઑવ્ ઇન્ડિયા લિ. (SAIL) ભારત સરકારની માલિકીનું છે અને તે ભિલાઈ, દુર્ગાપુર, રૂરકેલા, બોકારો, બર્નપુર, સાલેમ વગેરે સ્થળોએ આવેલા પ્લાન્ટોનું સંચાલન સંભાળે છે.
વિવિધ સ્ટીલ-પ્લાન્ટોની ક્ષમતા (1997-98) સારણી 1માં દર્શાવી છે. લોખંડ અને પોલાદનું ઉત્પાદન સારણી 2માં દર્શાવેલ છે.
સારણી 2 : લોખંડ અને પોલાદનું ઉત્પાદન (’000 ટનમાં)
સ્ટીલ પ્લાન્ટ | 1993-94 | 1994-95 | 1995-96 | 1996-97 | 1997-98 | |||||
કાચું
પોલાદ |
વેચાણક્ષમ
પોલાદ |
કાચું
પોલાદ |
વેચાણક્ષમ
પોલાદ |
કાચું
પોલાદ |
વેચાણક્ષમ
પોલાદ |
કાચું
પોલાદ |
વેચાણક્ષમ
પોલાદ |
કાચું
પોલાદ |
વેચાણક્ષમ
પોલાદ |
|
ભિલાઈ
દુર્ગાપુર રૂરકેલા બોકારો ઍલૉય સ્ટીલ પ્લાન્ટ સાલેમ IISCO |
3953
618 1148 3712 210
– 322 |
3335
641 1130 3205 160
46 333 |
4051
936 1178 3656 200
– 344 |
3409
852 1201 3168 154
56 332 |
4073
1024 1205 3680 252
– 329 |
3494
947 1148 3330 188
48 302 |
4187
1248 1240 3644 248
– 352 |
3482
1093 1180 3046 201
132 352 |
4223
1365 1176 3534 204
– 298 |
3524
1259 1180 2748 154
177 298 |
જ. પો. ત્રિવેદી
ગાયત્રીપ્રસાદ હીરાલાલ ભટ્ટ
ગૌતમ ઉપાધ્યાય
કિશોર પંડ્યા