કાપડઉદ્યોગ અને તેનો વિકાસ
કાપડ ઉદ્યોગ અને તેના અંતર્ગત ઘટકોના વિકાસની રૂપરેખા
1. પ્રાચીન ઇતિહાસથી ઓગણીસમી સદી સુધી
કાપડ–ઉત્પાદનની શરૂઆત : કાપડની બનાવટનાં બે ઉદભવસ્થાન છે – હુન્નરઉદ્યોગ અને અર્વાચીન સંશોધન. પ્રાથમિક બનાવટમાં વળી શકે તેવા નેતર, વાંસ કે બીજી વસ્તુઓમાંથી ટોપલીઓ બનાવવામાં આવતી હતી. ત્યાર પછી દોરડાના પુનરાવર્તિત ગાળા વડે બનાવવામાં આવતી જાળી(net)ને મૂકી શકાય. આફ્રિકા અને પેરૂમાં લોકો મર્યાદિત દોરડાનો ઉપયોગ કરીને જાળી બનાવતા. કાપડ નાશ પામે તેવું હોવાને કારણે તેના પ્રાચીન નમૂના મળવા અતિ મુશ્કેલ છે. પાષાણયુગમાં ટોપલીને મળતી બનાવટના વણાટકામના નમૂના મળી આવ્યા છે. ઈ. પૂ. 3000 વર્ષ પહેલાં ભારતમાં સૂતર વપરાતું હતું; એ જ અરસામાં ચીનમાં રેશમના ઉત્પાદનની નોંધ થયેલી છે. પ્રાચીન યુગમાં સૂતર, રેશમ, ઊન, શણ વગેરે રેસાનો કાપડ બનાવવામાં ઉપયોગ કરવામાં આવતો હતો. વણાટ અને કાંતણ આ પ્રક્રિયાને અનુસરે છે. કાપડવણાટ ટોપલીની બનાવટમાંથી ઉદભવેલ છે. [કાંતણપ્રક્રિયા, વિશ્લેષણાત્મક રીતે કાપડ ઉત્પાદન વિભાગ, દોરાની બનાવટ કાંતણ અને વણાટ વિભાગમાં જુઓ.]
શરૂઆતનું કાપડ : કાપડનું ઉત્પાદન વણાટની સાદી પદ્ધતિથી કરવામાં આવતું, જે આકર્ષક હતું. દુનિયાના જુદા જુદા પ્રાદેશિક વિસ્તારની વિશિષ્ટતા ધરાવતા અને જુદી જુદી ભાત તેમજ રંગો અને વણાટની કળાકારીગરીના નમૂના નોંધપાત્ર છે.
દોરા અને કાપડ ઘણા સમયથી રંગવામાં અને છાપવામાં આવતાં હતાં. ઈ. પૂ. 200 વર્ષ પહેલાં રોમન રાજ્યમાં રંગાયેલા કાપડના નમૂના મળી આવેલ. ચીનમાં (ઈ. સ. 618-907) રેશમના દોરાને બાંધીને રંગવા માટે જે પદ્ધતિ વપરાતી હતી તે ‘ટાઈ ઍન્ડ ડાઈ’ તરીકે ઓળખાય છે. ઈ. પૂ. 400 વર્ષ પહેલાંના ભારતમાં બાંધણી તરીકે ઓળખાતા છપાયેલા કાપડના નમૂના મળેલ છે. ચોથી સદીના સમયમાં ઇજિપ્તમાંથી મળેલ શણ અને ઊનના કાપડના નમૂના ત્યાં વિકાસ પામેલી વણાટની પદ્ધતિનો ખ્યાલ આપે છે. ઈરાનમાંથી સાદા કાપડના તથા જાજમ અને પડદાના કાપડના પ્રાચીન નમૂના મળેલા છે.
મધ્ય યુગનું કાપડ : મધ્ય યુગમાં તુર્કસ્તાનની અમુક જાતિના લોકો ઊની કાપડ, જાજમ, રૂમાલ તથા ધાબળા બનાવવામાં કુશળ હતા. ભારતમાં મુઘલ યુગ (અગિયારમી સદીથી અઢારમી સદી સુધી) અને કદાચ એ પહેલાં બંગાળના ઢાકા શહેરમાં રંગીન તથા છાપકામવાળી અતિબારીક મલમલ (muslin) બનાવવામાં આવતી હતી. મુસ્લિમ ધર્મની મનાઈ હોવા છતાં, જીવંત વસ્તુઓની રજૂઆત કરતા ઘણી ઊંચી જાતના નમૂનાવાળું કાપડ મુસ્લિમ દેશોના લોકો બનાવતા હતા.
827 પછી સિસિલીના પેલરમોના રાજમહેલમાં સુંદર કાપડ બનાવવામાં આવતું હતું. ગ્રીસ અને તુર્કસ્તાનથી આશરે 1130માં વણાટકામના હોશિયાર કારીગરો પેલરમોમાં આવ્યા હતા અને રેશમમાં સોનાના તારને ગૂંથીને કાપડ બનાવતા હતા.
ઇટાલીમાં કાપડઉદ્યોગનો વિકાસ : 1266માં ફ્રાન્સના સિસિલી પરના વિજય બાદ ઘણા કારીગરો ઇટાલીના લૂકા પ્રદેશમાં વસ્યા. થોડા જ વખતમાં તેઓ રેશમના કાપડવણાટમાં ફૂલપાંદડીની ભાત માટે જાણીતા થયા. 1315માં ફ્લૉરેન્ટાઇને લૂકાને જીત્યા બાદ, સિસિલિયન કારીગરોને ફ્લૉરેન્સમાં વસાવ્યા. 1100ના ગાળામાં ફ્લૉરેન્સને ઝીણા ઊની કાપડના અને મખમલ(velvet)ના ઉત્પાદનનું કેન્દ્ર માનવામાં આવતું હતું.
પંદરમી સદીના અંત સુધીમાં 1,600 રેશમના અને 30,000 ઊની કાપડના કારીગરો વડે ઊંચી જાતની વણાટપદ્ધતિ વિકસાવવામાં આવી હતી. જિનીવા અને વેનિસમાં પણ સોળમી સદીના મધ્યભાગમાં મખમલ અને કિનખાબ(જરી)ના ઉદ્યોગનો મોટો વિકાસ થયો હતો (જુઓ કાપડનું ઉત્પાદન).
ફ્રાંસ અને જર્મનીમાં કાપડઉદ્યોગ : 1480માં ફ્રાન્સમાં રેશમના વણાટની શરૂઆત થઈ. 1520માં થોડા ઇટાલિયન અને ફ્લેમિશ વણકરોને ફાઉન્ટેનબ્લુ લાવી રાજાના વણકરની સીધી દેખરેખ નીચે તેમની પાસે પડદાનું કાપડ તૈયાર કરાવવામાં આવતું હતું. યુરોપના રેશમના ઉત્પાદન-કેન્દ્ર લિયોનમાં અન્ય કારીગરોને લાવવામાં આવ્યા હતા. 1589 સુધી મૂળ ઇટાલીનું સુશોભનવાળું કાપડ ફ્રાન્સમાં વપરાતું હતું. આ સમયમાં ઇંગ્લૅન્ડમાં રાજા હેનરી ચોથાએ ઊંચા પ્રકારની જાજમ તથા પડદાનું કાપડ બનાવવાનું કારખાનું સેવોનિયરસમાં સ્થાપ્યું હતું. સોળમી સદીમાં ઝાન, ગૉબ્લાંન ફ્રાન્સમાં પડદાનું કાપડ બનાવવાના કારખાના માટે ફ્લેમિશ વણકરોને લઈ આવ્યા હતા. ફ્રેન્ચ રાજા લુઈ તેરમાના શાસનકાળમાં (1610થી 1643) ઘરેણાંની ભાત(જરીકામ)વાળું કાપડ બનાવવાની શરૂઆત થઈ, જે ઇટાલીના જરીકામ જેવું હતું. 1662માં ફ્રાન્સના રાજા ચૌદમા લુઈએ પૅરિસમાં ગૉબ્લાંનું કારખાનું ખરીદ્યું. રૂઆં પણ માટીનાં વાસણોને મળતી ભાતવાળા કાપડના ઉત્પાદન માટે જાણીતું થયું. ફ્રાન્સમાં તેના પ્રાદેશિક લઢણ(fashion)ના અને વિશિષ્ટ કારીગરીના કાપડ માટે પ્રગતિ સધાતી રહી. રાજા સોળમા લુઈ(1774થી 1793)એ કાપડના વણાટમાં સુધારો કરી વેલપાંદડાં પ્રકારની ભાત ઉપસાવવાની શરૂઆત કરી હતી. 1790માં ફ્રાન્સમાં ક્રાંતિ થઈ ત્યારે કાપડઉદ્યોગમાં રુકાવટ આવી, પરંતુ તે થોડાક જ વખતમાં ફરી ઉત્થાન પામ્યો. ફ્લૅન્ડર્સ અને આર્ત્વા ઉત્તમ પ્રકારનાં કાપડ બનાવવાનાં કેન્દ્રો હતાં. ઍરાસ રેશમ અને મખમલ માટે; જેન્ટ, યેપર અને કોર્ટરાઈ દમાસ્કસ શણના વણાટ માટે તથા ઍરાસ અને બ્રસેલ્સ પડદાના કાપડ માટે જાણીતાં હતાં. અઢારમી સદીમાં દમાસ્કસ તેના ખાસ સંદેશયુક્ત મોટી ભાત માટે અને ઘણી ઊંચી ગુણવત્તા ધરાવતા લિનન (શણના) કાપડ માટે જાણીતું હતું. જર્મનીમાં ક્લોન પણ એક મહત્વનું ઉત્પાદનકેન્દ્ર હતું; ત્યાં બનેલું જાડા પટ્ટાનું કાપડ (જેમાં સોનાના જરીકામથી સંતોની આકૃતિ અને શિલાલેખોની ભાત ઉપજાવવામાં આવતી) સારી પ્રસિદ્ધિમાં આવ્યું હતું.
ઇંગ્લૅન્ડમાં કાપડઉદ્યોગ : ઈસુની તેરમી અને ચૌદમી સદીમાં ઇંગ્લૅન્ડમાં મુખ્યત્વે શણ અને ઊનના કાપડનું ઉત્પાદન કરવામાં આવતું અને કાપડને રંગનાર અને છાપનાર ફ્લેમિશ લોકોનું મહત્ત્વ તે વખતના વેપાર પર અસરકારક રીતે ફેલાયેલું હતું. 1455માં નૉરિચ અને લંડનમાં રેશમના ઉત્પાદનની શરૂઆત થઈ. 1564માં રાણી ઇલિઝાબેથ પહેલાંએ ખાસ હકપત્ર દ્વારા ફ્લેમિશ અને ડચ રહેવાસીઓને નૉરિચમાં દમાસ્કસ વણાટ અને ફૂલપાંદડીની ભાતવાળા રેશમના ઉત્પાદન માટે પરવાનગી આપી હતી. ફ્રાન્સમાં ખ્રિસ્તી ધર્મના અનુયાયીઓ(protestants)ના જુલમના કારણે ઘણા વણકરો ઇંગ્લૅન્ડમાં નૉરિચ, બ્રેઇન્ટ્રી અને લંડનમાં આવી વસ્યા; આશરે 3,500 નિરાશ્રિત વણકરો લંડનના સ્પિટલફીલ્ડ્ઝમાં વસ્યા અને સમય જતાં તે સ્થળ દમાસ્કસ વણાટનું, રેશમ અને કિનખાબના ઉત્પાદન માટેનું મુખ્ય કેન્દ્ર બન્યું. આ વણકરો રેશમી કાપડની ઊંચી ગુણવત્તા, સંકુલ વણાટની કારીગરી તથા સારા પોત માટે જાણીતા હતા. નૉરિચ પણ રેશમ અને ઊનની સુશોભિત શાલ માટે જાણીતું હતું.
અમેરિકાનો કાપડઉદ્યોગ : વણાટકામ અને રંગવાની પ્રક્રિયા અંગ્રેજોના આગમન પહેલાં અમેરિકામાં વિકાસ પામેલાં હતાં. પ્રાચીન સમયમાં ઉત્તર અને દક્ષિણ અમેરિકા વણાટકામમાં આગળ હતાં. પેરૂવિયન અને મેક્સિકન લોકો પાસે સુંદર વણાટકામવાળાં કપડાં હતાં. પેરૂવિયન કાપડ પ્રાચીન ઇજિપ્તમાં મળી આવતા કાપડને મળતું હતું. ઇન્કા લોકો સુતરાઉ કાપડ અને ઊની કાપડ ઉપર ચળકતા રંગો આધાર તરીકે વાપરતા હતા. એરિઝોના અને ન્યૂ મેક્સિકોમાંની નવાહો જાતિએ ખાસ બનાવેલ ઊનના ધાબળાનું વણાટકામ ઘણું ઘટ્ટ અને ચળકતા રંગોવાળું હતું. 1638માં મૅસેચૂસેટ્સમાં અંગ્રેજ વસાહતીઓએ કાપડઉદ્યોગ શરૂ કર્યો; ત્યાંના યૉર્કશાયરના વણકરોએ સુતરાઉ ફસ્ટિયન્સ, સુતરાઉ ટિવલ-જીન્સ અને લિન્ઝી-વુલ્ઝી, જાડા અને આછા વણાટવાળા કાપડનું ઉત્પાદન લિનન અને ઊનમાંથી કર્યું. 1654માં કાપડનું પૂરા કદનું કારખાનું શરૂ કરવામાં આવ્યું. 1793માં ઈલાઈ વ્હિટનીએ કપાસ લોઢવાના યંત્રની શોધ કરી.
ભારતમાં કાપડઉદ્યોગ : પ્રાચીન સમયમાં ભારતમાંના વસ્ત્રપરિધાન અને તેના ઉપયોગના જુદા જુદા ઉલ્લેખો શિલાલેખ, તેમજ ધાર્મિક લખાણોમાંથી મળેલા છે. ભારતમાંથી આશરે ઈ. પૂ. 4000 વર્ષ પહેલાં ઊન અને રેશમ ઉપર છાપકામ થયેલા કાપડના નમૂના મળેલ છે. આ નમૂના ઉત્તમ વણાટની કારીગરી દર્શાવે છે. કાંતણની પ્રક્રિયાના વિકાસમાં પાયારૂપ સ્પિનિંગવ્હિલ – રેંટિયો (spinning wheel) ભારતમાંથી બીજા દેશમાં ગયેલો તેમજ આડી હાથસાળ (horizontal loom) પણ ભારતમાં જ સૌપ્રથમ બનેલી એમ માનવામાં આવે છે. ભારતનું કાપડ ઘણાં વર્ષોથી જાણીતું હતું. ઢાકાની મલમલ અને કાશ્મીર અને દક્ષિણ ભારતનું રેશમ જાણીતાં હતાં. દેશ ઉપર બીજી સંસ્કૃતિઓનાં આક્રમણ અને અંદર અંદરના રાજ્યપલટાને કારણે યાંત્રિક રચના સહકારી ધોરણે વિકાસ પામી જ નહિ, પરંતુ ગૃહઉદ્યોગ તરીકે જ કાપડ તૈયાર થતું રહ્યું, તેના નમૂનારૂપ ગુજરાતના પાટણનાં પટોળાં, બાંધણી ને કચ્છનું ‘બાટીક’ છાપકામ ભારતની કાપડ-કારીગરી માટે દુનિયાભરમાં જાણીતાં હતાં. પટોળાં માટે વાપરવામાં આવતા દોરા ગાંઠીને રંગવાની પદ્ધતિ (tie and dye) અને બાટીક છાપકામ આજે પણ આશ્ચર્ય પમાડે તેવી કળા છે. 1430-1470ના ગાળામાં તુર્કસ્તાનના અનુભવી કારીગરોને કાશ્મીરમાં લાવીને તેમની મદદથી ઊની પ્રકારના ‘ટસ’ના રેસાનો ઉપયોગ કરી શાલ બનાવવામાં આવતી હતી. અઢારમી સદીના પૂર્વાર્ધમાં તેમાં વેલબુટ્ટાની ઉપસાવેલી કે ભરતકામવાળી ભાત તૈયાર કરવામાં આવતી હતી, જેને કિનારી ઉપર ફૂમતાં મૂકીને શણગારવામાં પણ આવતી. અંગ્રેજ શાસન દરમિયાન અને ઇંગ્લૅન્ડની ઔદ્યોગિક ક્રાંતિથી ગૃહઉદ્યોગને ઘણું નુકસાન થયેલું; પરંતુ યાંત્રિક ક્રાંતિને લીધે સહકારી ધોરણે કાપડઉદ્યોગની શરૂઆત ઓગણીસમી સદીમાં થવા પામી. જોકે અંગ્રેજ શાસન દરમિયાન વણાટકામના પારંગત કારીગરોની ભારે અવદશા થઈ. ઇંગ્લૅન્ડના કાપડઉદ્યોગને બજાર મળે તે માટે ઇરાદાપૂર્વક ભારતીય કાપડના ગૃહઉદ્યોગને મૃતપ્રાય બનાવી દેવાયો. 1915 પછી શરૂ થયેલ સ્વરાજ્યની ચળવળમાં રાષ્ટ્રપિતા ગાંધીજીએ રેંટિયાને સ્વરોજગારીના પાયાના સાધન તરીકે મહત્વ આપ્યું. ત્યારથી કાંતણ અને હાથવણાટનું ગૃહઉદ્યોગ તરીકેનું મહત્વ ફરી વાર અસ્તિત્વમાં આવ્યું. આ પ્રકારે તૈયાર થયેલા કાપડને ખાદી તરીકે ઓળખવામાં આવે છે. ભારતના સ્વાતંત્ર્ય (1947) બાદ પણ તે કળાને સ્વરોજગાર આપનાર ગૃહઉદ્યોગ તરીકે વિકસાવવામાં આવી છે.
ઔદ્યોગિક ક્રાંતિની અસરો : અઢારમી સદી સુધી કાપડઉદ્યોગ ખૂબ જ વિકાસ પામેલ હુન્નરઉદ્યોગ હોવા છતાં તે ગૃહઉદ્યોગ તરીકે જ અસ્તિત્વમાં હતો. સહકારી કાર્યક્ષેત્રમાં થતા લાભના અનુભવના આધારે 1568માં સૌપ્રથમ ઝુરિકમાં અને ત્યારબાદ ઇંગ્લૅન્ડમાં ડર્બી ખાતે 1717માં બીજું કારખાનું શરૂ કરવામાં આવ્યું. ઉત્તર ઇંગ્લૅન્ડમાં કારખાનાની સંચાલનવ્યવસ્થા ઘણી જ વિકાસ પામેલી હતી; પરંતુ ઔદ્યોગિક ક્રાંતિના ઉચ્ચ સ્તરે 1760 અને 1815ની વચ્ચે કારખાના-પદ્ધતિ(mill system)નો ઉદભવ થવા પામ્યો.
1733માં જ્હૉન કેના ઊડતા શટલની શોધના કારણે વણાટકામ ઘણું જ ઝડપી બન્યું અને તેની સફળતાએ ઝડપી સાળ માટે ઘણા ઝડપી કાંતણની જરૂર ઊભી કરી. 1769થી 1779 વચ્ચે સર રિચાર્ડ આર્કરાઇટે યાંત્રિક કાંતણની શોધ કરી અને સૅમ્યુઅલ ક્રૉમ્પ્ટને ઊનના કાંતણ માટે કાર્ડિંગ અને કૉમ્બિંગની શરૂઆત કરી. બદલાતી સદીઓની સાથે જ સૌપ્રથમ યંત્રસાળ (power loom) બનાવવામાં આવી. જળશક્તિથી ચાલતાં યંત્રો કરતાં વરાળશક્તિથી ચાલતાં યંત્રોની ઝડપ ઘણી જ વધારે હતી. આમ ઔદ્યોગિક સંચાલનપદ્ધતિ વધુ વિકસિત અને મજબૂત થઈ, જે સૌપ્રથમ ઇંગ્લૅન્ડમાં અને ત્યારબાદ યુરોપ અને અમેરિકામાં વિકાસ પામી.
ઓગણીસમી સદીથી અત્યાર સુધીનો કાપડઉદ્યોગ : ઓગણીસમી સદી દરમિયાન કાપડ બનાવવાનાં યંત્રોમાં સુધારા થયા અને તેની સફળતાથી ઉત્પાદનમાં વધારો થયો તથા તૈયાર કાપડ અને કપડાંની કિંમતમાં નોંધપાત્ર ઘટાડો થયો. પૂર્ણ કે પૂર્ણતાએ પહોંચેલાં સ્વયંસંચાલિત યંત્રોની પદ્ધતિને ધ્યાનમાં રાખીને વીસમી સદીમાં પણ આ કાર્ય ચાલુ રહ્યું છે.
કાપડની બનાવટમાં વૈજ્ઞાનિક પદ્ધતિનો ઉપયોગ : કાપડ-ઉત્પાદનનું યાંત્રિકીકરણ અને વિકાસ ઔદ્યોગિક ક્રાંતિની સાથે જોડાયેલાં છે અને તેમાં ઘણા જ સાદા ઇજનેરી અને ભૌતિક સિદ્ધાંતોનો ઉપયોગ થયેલ છે. વધુ વિકાસ માટે કાપડની પ્રક્રિયાઓના વૈજ્ઞાનિક સિદ્ધાંતોની સંપૂર્ણ સમજૂતીની જરૂર હતી. રેસા(fibres)ના બંધારણ અને ગુણધર્મોની પાયાની માહિતીની ખામીને કારણે તથા મર્યાદિત સમજણના કારણે કાપડની પ્રક્રિયાઓના વૈજ્ઞાનિક સંશોધનમાં વિલંબ થયો. આમ છતાં ઓગણીસમી સદીના ઉત્તરાર્ધમાં રેસાના રાસાયણિક અને ભૌતિક ગુણધર્મની માહિતીમાં વધારો થતાં વૈજ્ઞાનિક પદ્ધતિમાં નોંધપાત્ર કાર્ય થયું. રાસાયણિક વિદ્યામાં નવા રાસાયણિક પદાર્થની બનાવટ અને રેસાની રાસાયણિક સક્રિયતા તરફ વૈજ્ઞાનિકોનું ધ્યાન કેન્દ્રિત થયું. વીસમી સદીમાં ઇલેક્ટ્રૉનિક્સ અને કમ્પ્યૂટરના વિકાસથી કાપડના વિકાસ અને સંશોધનમાં નવી ભૌતિક અને ઇજનેરી કલ્પનાઓનો ઉપયોગ થવા લાગ્યો.
કૃત્રિમ (માનવસર્જિત) રેસાના વિકાસની અસર : વિજ્ઞાનનો પ્રગતિકારક ઉપયોગ અને રાસાયણિક પદાર્થમાંથી બનાવવામાં આવતા કૃત્રિમ રેસા નવા પ્રકારના કાપડ તરીકે કાયમી વપરાશમાં ઉપયોગી થયા. વળી કુદરતી રેસા ઉપર કરવામાં આવતી રાસાયણિક પ્રક્રિયાઓ માટે અને નવી પદ્ધતિઓના ઉદભવ માટે આ કૃત્રિમ રેસા જવાબદાર છે. કૃત્રિમ રેસા બનાવવા માટેના ઉદ્યોગમાં, વર્ષોના કુદરતી રેસાના કાપડઉદ્યોગના અનુભવને આધારે ઝડપથી પ્રગતિ થઈ શકી છે. ઔદ્યોગિક વપરાશ વધવાના કારણે જ આ રેસાના જુદા જુદા ગુણધર્મોના આધારે તેના ઉપયોગની માહિતી ભેગી કરવામાં સફળતા મળી છે.
ઔદ્યોગિક ક્રાંતિની અસર નીચે ભારતમાં કાપડઉદ્યોગનું પુનરુત્થાન : 1818માં બંગાળના કોલકાતા (કલકત્તા) શહેરમાં અંગ્રેજ ઉદ્યોગપતિએ ઔદ્યોગિક કાપડ-ઉત્પાદન શરૂ કર્યું. 1851માં પારસી યુવાન સર કાવસજીએ મુંબઈમાં કાપડની મિલ શરૂ કરી. 1854માં ભરૂચમાં સ્પિનિંગ મિલ સ્થાપવામાં આવી. એ જ વરસે ગુજરાતી ઉદ્યોગવીર રણછોડલાલે ઇંગ્લૅન્ડથી વહાણ મારફતે જરૂરી યંત્રો મંગાવીને કાંતણ, વણાટ તથા રંગવાની અને છાપવા તથા ઓપ આપવાની ક્રિયા સમાવતો શક્તિસંચાલિત સંયુક્ત એકમ ‘અમદાવાદ સ્પિનિંગ અને વીવિંગ’ના નામે શરૂ કર્યો. તેમાં તે વખતે 2,500 ત્રાક કાંતણ માટે ગોઠવવામાં આવી હતી. ત્યારબાદ 30 વર્ષના ગાળામાં તેને અનુસરીને બીજાં નવાં 32 કારખાનાં ઊભાં થયાં અને ઊંચી જાતનું કાપડ બનાવવા લાગ્યાં. આમ ગુજરાતમાં કાપડ-ઉત્પાદનના એકમ વધ્યા અને અમદાવાદ કાપડ-ઉત્પાદનના કેન્દ્ર તરીકે જાણીતું થયું. બીજા વિશ્વયુદ્ધ અને ભારતીય સ્વાતંત્ર્યસંગ્રામને કારણે સહકારી ક્ષેત્રનો વિકાસ રૂંધાયો પણ સ્વાતંત્ર્ય મળ્યા બાદ ફરી વાર ઉદ્યોગ ત્રણ સ્વરૂપે પ્રગતિ સાધી શક્યો, જેવાં કે ગૃહઉદ્યોગ, હાથસાળ, રેંટિયો અને બીજાં ઉપયોગી સાધનોથી થતું ઉત્પાદન; અર્ધસ્વયંસંચાલિત યંત્રોથી ઉત્પાદન અને સંપૂર્ણપણે યાંત્રિક ઉત્પાદન, જે એકમ મિલ તરીકે ઓળખાય છે. આમ ત્રણે સ્તરે સંચાલનમાં સહકારી વ્યવસ્થાની રચના જોવા મળે છે.
આધુનિક કાપડઉદ્યોગ : વિકસિત અને અર્ધવિકસિત દેશોમાં આધુનિક કાપડ બનાવવા માટેનાં પૂર્ણ ક્ષમતાવાળાં યાંત્રિક કારખાનાં આવેલાં છે. આ ઉપરાંત સૂતર, દોરા અને કાપડ બનાવવા માટેનાં યંત્રોમાં યાંત્રિક સુધારા તથા કાપડની ગુણવત્તામાં સુધારા કરવા, નવા રેસા અને પ્રક્રિયાઓમાં થતા વિકાસ અને કાપડની ગુણવત્તાની કસોટીની રીતો ધ્યાનમાં રાખવામાં આવે છે. આધુનિક કાપડઉદ્યોગ મોટા પાયા પર વસ્ત્રો બનાવવા ઉપરાંત ઔદ્યોગિક હેતુ માટે વાપરવામાં આવતા કાપડને પણ અગત્ય આપે છે. કાપડના જુદા જુદા ઉપયોગો અને ખાસ ઊંચી માગનું કાપડ બનાવવા માટે વિકસિત સંસ્થાઓમાં કાપડ-ઉત્પાદનનું જ્ઞાન ધરાવતા કારીગરો, ઇજનેરો, ડિઝાઇન-કલાકારો, તજ્જ્ઞો તેમજ ખરીદીનો કસબ જાણનારી વ્યક્તિઓનો ઉપયોગ કરવામાં આવે છે, જે ઉત્પાદકને હાલના બજાર તરફ દોરી જાય છે. આમ છતાં હજુ હાથવણાટના કાપડની સ્થાનિક બજારમાં તેમજ પરદેશમાં ફૅશન તરીકેની સારી માગ છે.
આધુનિક કાપડ : ઘણા પ્રકારનું આધુનિક કાપડ કૃત્રિમ રેસા અને કુદરતી રેસામાંથી બનાવવામાં આવે છે. કાપડના બંધારણના આધારે તેનું વર્ગીકરણ કરવામાં આવે છે. જાડા તાર અથવા પટ્ટીઓ રૂપે રેસાને પસાર કરી વણવામાં કે ગૂંથવામાં આવેલું કાપડ, જાળના રૂપે ગૂંથેલું કાપડ, રેસાનું યોગ્ય મિશ્રણ કરીને બનાવેલું કાપડ (blended fabrics) – ઊનના ધાબળા વગેરે તથા કૃત્રિમ અને કુદરતી રેસાનું મિશ્રણ કરી વણેલું કાપડ. સામાન્ય રીતે હાલમાં વ્યવહારુ વણાટ અને ગૂંથણકામથી કાપડ બનાવવાની પદ્ધતિનો અમલ થાય છે. આ ઉપરાંત આધુનિક કાપડ બનાવવા માટે નવી પદ્ધતિઓ વપરાય છે. કારણ કે જૂની પદ્ધતિથી ઉત્પાદન-ખર્ચ વધારે આવે છે. વળી આ આધુનિક પદ્ધતિઓ સંશોધન માટેની નવી ક્ષિતિજો ઉઘાડે છે.
ગુણવત્તાનું ધોરણ : આધુનિક કાપડને નિશ્ચિત ધોરણ મુજબ ઘણી કસોટીમાંથી પસાર કરવામાં આવે છે. સામાન્ય રીતે કાપડને મુખ્યત્વે જે જરૂરિયાત માટે વાપરવાનું હોય તે પ્રમાણે તેની નરમાશ અને મજબૂતાઈ હોય એ ગુણોની તપાસ કરવામાં આવે છે. ઔદ્યોગિક હેતુ માટે વાપરવામાં આવતું કાપડ કડકપણું અને ચોક્કસ પનો, એકમ ક્ષેત્રફળદીઠ વજન, વણાટ અને દોરાનું બંધારણ, મજબૂતાઈ, ખેંચાણશક્તિ, અમ્લતા, ક્ષારમયતા, જાડાઈ તથા છિદ્રાળુતા વગેરે કસોટીમાંથી પાસ થયેલું હોવું જરૂરી છે. પરિધાન માટેનાં વસ્ત્રોમાં ભૌતિક ગુણવત્તા ઉપરાંત છાપકામ અને રંગ મહત્વનાં છે. આ ઉપરાંત કાપડના જુદા જુદા ગુણધર્મો, જેમ કે તેની કુમાશ પણ ગ્રાહકની પસંદગી પર અસર કરે છે.
કાપડની ગુણવત્તા સાચવવા માટે કાપડઉદ્યોગ સંશોધન અને તેના વિકાસ ઉપર આધાર રાખે છે. મધ્યયુગની સહકારી મંડળીઓ ઊંચી ગુણવત્તા સાથે ઉત્પાદનનો સંબંધ જાળવતી હતી. ત્યારબાદ કાપડનાં કારખાનાંમાં કડક રીતે ગુણવત્તા તપાસવાની પદ્ધતિ દાખલ થઈ. પરિણામે નુકસાન વગરના કાપડ-ઉત્પાદન દ્વારા મેળવેલી ખ્યાતિને લીધે માલની માગ વધી; આધુનિક રીતે વિશિષ્ટ પ્રકારનાં સાધનોના વિકાસથી રેસા, દોરા અને કાપડના ગુણધર્મોને તપાસીને ગુણવત્તાની કસોટી કરવામાં આવે છે.
ઔદ્યોગિક હેતુ માટે, લશ્કર માટે, સરકારી કાર્યાલયોમાં વપરાતા ગણવેશના કાપડ માટે ચોક્કસ ધોરણ નક્કી કરવામાં આવે છે. તે જ રીતે છૂટક તથા જથ્થાબંધ કાપડના ખરીદનાર માટે પણ આ કસોટીની રીતો અપનાવવામાં આવે છે. ગ્રાહક સંબંધી ક્ષેત્રોમાં કામ કરતા લોકો પણ કાપડની કસોટીથી માહિતગાર હોય છે અને ખરીદતી વખતે તેની જરૂરી તપાસ તથા સાબિતી માટે સંકેત કે છાપનો અભ્યાસ કરી ખરીદે છે.
આધુનિક કાપડ બનાવતા ઘણા એકમો, માલ બનાવવાની મહત્વની પ્રક્રિયાના સ્થાને જ ગુણવત્તાની તપાસ માટેની સુવિધાઓ રાખે છે. દોરાની એકસરખી જાડાઈ તેમજ બીજા ગુણધર્મો માટે, કાપડ-વણાટની ખામી માટે અને તૈયાર કાપડ રંગ અને ઓપ આપનાર રસાયણોની ર્દઢતા માટે તપાસવામાં આવે છે. જોકે દરેક દોરાને અથવા કાપડના ટુકડાને તપાસવો શક્ય હોતો નથી. પણ આંકડાશાસ્ત્રનો ઉપયોગ કરી, નુકસાનીની નક્કી કરેલી સીમાઓમાં રહીને કસોટી કરવાનાં યાંત્રિક સાધનોના ઉપયોગથી કિંમત અને સમયમાં ઘણો જ બચાવ થઈ શક્યો છે. કદ (dimension), મજબૂતાઈ, છિદ્રાળુતા વગેરે માપવા માટેની રીતો નક્કી થઈ છે, જે સામાન્ય રીતે ઉદ્યોગની માગ અને જરૂરિયાત મુજબ કરવામાં આવે છે. રંગના પાકાપણા (fastness) માટેનાં માપ (standard) મળે છે. પાણી-પ્રતિરોધક (water resistant), સળ-પ્રતિરોધક (crease resistant), આગ-પ્રતિરોધક (flame resistant) જેવા અગત્યના ગુણધર્મો માટે પણ અમુક કસોટીધોરણ નક્કી થયેલાં છે અને જુદા જુદા એકમોએ તેમની પોતાની કસોટીઓ વિકસાવીને અપનાવી છે તેમજ જે કાપડ આગ-પ્રતિરોધક તરીકે દર્શાવવામાં આવેલું હોય તે એવા ધોરણસર હોય કે જેમાં આગ-પ્રતિરોધક ગુણનું સાતત્ય જળવાતું હોય તેની તકેદારી રખાય છે.
ઘણા ઉત્પાદકો વ્યાપાર-ચિહ્ન અને ગુણવત્તાની ખાતરી ધરાવતાં લેબલ લગાવે છે. તેવી જ રીતે ખાસ પ્રક્રિયાના પરવાનેદારો જે તે પ્રક્રિયાનાં વ્યાપારચિહ્ન પણ ઘણી વાર ગુણવત્તાની ખાતરી માટે લગાવે છે, જેમાં માલના ઉત્પાદકો તરફથી નક્કી કરેલાં ધોરણ જાળવવાની ખાતરી આપવામાં આવી હોય છે; દા.ત., સનફોરાઇઝ્ડ કાપડ.
2. દોરાનું ઉત્પાદન
દોરો એકસૂત્રી રીતે કુદરતી અથવા કૃત્રિમ રેસા કે તંતુઓ અથવા બીજી વસ્તુઓ કંતાઈને બને છે. તે વણાટ કે ગૂંથણથી બનતા કાપડ માટે અનુકૂળ હોય છે. દોરો એક કરતાં વધારે તંતુઓને વળ આપવાથી બની શકે; અનિશ્ચિત લંબાઈના તાંતણા અગર રેસાને વળ આપ્યા વગર અથવા વળ આપીને એકરૂપ કરી દોરારૂપે બનાવવામાં આવે છે, જેને ફિલામેન્ટ કહે છે. અનિશ્ચિત લંબાઈના એકતંતુરૂપ તાંતણાને એક-તંતુક (mono-filament) કહે છે અને એક કરતાં વધારે એક-તંતુક ભેગાં કરવાથી બહુતંતુક (multi-filament) બને છે. કાગળ અથવા ધાતુના પતરાને જેમ વિભાજિત કરી પટ્ટીના સ્વરૂપે બનાવવામાં આવે છે તેમ તંતુ બનાવવામાં આવે છે. કાપડની બનાવટમાં વપરાતા દોરાના ગુણધર્મો તેના દેખાવ, બંધારણ, પોત અને ઉપયોગ ઉપર આધાર રાખે છે.
કાપડની બનાવટમાં વપરાતા તંતુઓ (textile fibres) : કાચો માલ – જે તંતુઓ કાપડની બનાવટ માટે ઉપયોગી હોય તે દોરા અને કાપડની બનાવટ માટે પૂરતી લંબાઈ, બારીકાઈ (fineness), મજબૂતાઈ અને કુમાશ (flexibility) ધરાવતા હોવા જોઈએ અને કાપડ જે હેતુ માટે બનાવેલ હોય તેની અસર સામે ટકી શકે તેવા હોવા જોઈએ. આ ઉપરાંત તેના બીજા ગુણધર્મો, જેવા કે સ્થિતિસ્થાપકતા (plasticity), વળ (crimp-waviness), ભેજગ્રાહકતા (moisture absorption), ગરમી અને સૂર્યપ્રકાશની અસર, ઉત્પાદન દરમિયાન જુદાં જુદાં રસાયણોની થતી અસર અને તૈયાર કાપડની ડ્રાય ક્લીનિંગ અને ધોવાની ક્રિયા તેમજ જીવાણુ અને જંતુઓ માટેની પ્રતિરોધકતા વગેરે તપાસવામાં આવે છે. આ ગુણધર્મોના તફાવતના આધારે તંતુઓનું જુદા જુદા ઉપયોગ માટે યોગ્ય સ્થાન નક્કી કરી શકાય છે.
સૌપ્રથમ કાપડ-ઉપયોગી તંતુઓ પ્રાણીઓ અને વનસ્પતિમાંથી મળી આવ્યા હતા. ખૂબ લાંબા સમય સુધી કુદરતમાં મળી આવતા તંતુઓ ઉપરના પ્રયોગોથી રૂ, ઊન, શણ, ફ્લૅક્સ અને રેશમ જેવા તંતુઓ સંતોષકારક લાગવાથી ઉપયોગ માટે તેમનો સ્વીકાર થયો. ઈ. સ.ની ઓગણીસમી સદીમાં માનવસર્જિત તંતુઓનો વ્યાપારી ધોરણે વિકાસ શરૂ થયો; 1940 સુધીમાં તેનો ઘણો વિકાસ થયો હતો; બીજા વિશ્વયુદ્ધ પછી તે ઝડપી વિકાસ પામ્યો અને 1970 સુધીમાં તે વિશાળ સંશોધન અને વિકાસ માટેનો વિષય બની રહ્યો. આમાં ફરી વાર ઉત્પાદન કરેલ (regenerated) તંતુઓ(જેવા કે રેયૉન-rayon-fibres; આ તંતુઓ બનાવવા માટેના પદાર્થ કુદરતમાં અસ્તિત્વમાં છે)ના વિકાસને ગણવામાં આવે છે. ખનિજ અને ખનિજ-તેલમાંથી મેળવવામાં આવતા રાસાયણિક પદાર્થમાંથી સંશ્લેષિત રેસા બનાવવામાં આવે છે. રાસાયણિક પદાર્થનો ઉપયોગ કરી બનાવવામાં આવતા રેસા (દા.ત., નાયલૉન, પૉલિયેસ્ટર, ઍક્રિલિક વગેરે) આધુનિક સમાજમાં ઘણા જ ઉપયોગી નીવડ્યા છે.
કિંમતને અસર કરતાં પરિબળો : તંતુઓની કિંમત તેમની ઉપયોગિતા, બજારની માગ અને તેમના ઉપર કરવામાં આવતી પ્રક્રિયાના પ્રકાર તેમજ તેમની સર્વગ્રાહિતા પરથી નક્કી થાય છે. કુદરતી તાંતણાના ઉત્પાદન માટે વિશાળ જમીન, હવામાન અને તેને વારંવાર ઉત્પાદનસ્થળથી ઔદ્યોગિક ઉત્પાદનના સ્થળ સુધી લાવવા માટેનાં ખર્ચ મહત્વનાં પરિબળ છે. કુદરતી તંતુઓની ગુણવત્તા અને તેનો જથ્થો બદલાતાં રહેવાથી કિંમતમાં વધઘટ રહ્યાં કરે છે. ઉત્પાદનપ્રક્રિયા દરમિયાન જુદી જુદી ગુણવત્તા સુધારવા માટે સંશોધન કરવામાં આવે છે.
માનવસર્જિત તંતુઓ કાપડના ઉત્પાદનસ્થળ પાસે જ બનાવી શકાય છે; તેના ઉત્પાદન માટે વિશાળ જમીનની જરૂર નથી; આ તંતુઓ જરૂરિયાત મુજબના ગુણધર્મોવાળા અને જરૂરી જથ્થામાં ઝડપથી બનાવી શકાય છે; દોરો બનાવવા માટે ઓછી પ્રક્રિયામાંથી પસાર થવું પડે છે. શરૂઆતની ઉત્પાદનકિંમત યંત્રસામગ્રીના ઉપયોગને લીધે ઘણી ઊંચી આવે છે, પરંતુ તે કિંમત જળવાઈ રહે છે અને જેમ ઉત્પાદન વધારવામાં આવે તેમ નીચી આવે છે.
માનવસર્જિત તંતુઓ માટે જુદા જુદા વિશિષ્ટ હેતુઓ માટેની માગને પહોંચી વળવા, જરૂરી સંશોધન દ્વારા ગુણધર્મોમાં સુધારા થાય છે. માનવસર્જિત તંતુઓનો ઉપયોગ અને ઉત્પાદન વધવા છતાં, મુખ્ય કુદરતી તંતુઓએ પોતાનું ઉદ્યોગ પરનું પ્રભુત્વ જાળવી રાખ્યું છે.
દોરામાં રૂપાંતર : રેશમ અને માનવસર્જિત તંતુઓમાંથી બનાવેલ તંતુઓની લંબાઈ ઘણી હોવાથી, ટૂંકા તંતુઓ માટેની કાંતણક્રિયા જે દોરો બનાવવા માટે કરવી પડે છે તે કરવાની જરૂર પડતી નથી. વળ ચડાવ્યા સિવાયના એકસાથે સળંગ દોરડાના રૂપમાં ભેગા કરેલા માનવસર્જિત તંતુઓને ટો કહેવામાં આવે છે. થોડો વળ ચડાવીને તાંતણાને એકત્રિત કરીને જરૂર મુજબની જાડાઈના દોરા બનાવવામાં આવે છે. રૂના તાંતણા માત્ર 10.6 સેમી. લાંબા હોય છે તેમને જરૂરિયાત મુજબની લંબાઈ મેળવવા માટે મજબૂતાઈથી વળ ચડાવવામાં આવે છે.
સામાન્ય રીતે લાંબા તાંતણા (filament yarns) ચળકતા, લીસા અને બારીક, જ્યારે ટૂંકા તંતુઓ (staple fibres) ચળકાટ વગરના, તંતુમય અને જાડા હોય છે. માનવસર્જિત લાંબા તાંતણાને પહેલેથી નક્કી કરેલી લંબાઈ મુજબ કાપીને ટૂંકા તંતુઓરૂપે ફેરવવામાં આવે છે. તેમને સામાન્ય રીતે મૂળ નામ સાથે જોડીને ઓળખવામાં આવે છે; જેમ કે, રેયૉનના તંતુઓ (rayon staple fibre), પૉલિયેસ્ટર તંતુઓ વગેરે.
અપરિષ્કૃત તંતુઓ પર પ્રક્રિયા : આધુનિક કારખાનામાં મોટા ભાગે અપરિષ્કૃત તંતુઓ પર યાંત્રિક ધોરણે પ્રક્રિયા કરવામાં આવે છે. રૂના તંતુઓ ગાંસડીઓરૂપે અને ઊન ગાંઠારૂપે કારખાનામાં આવે છે. કારખાનામાં તેમાંથી જુદા જુદા પ્રકારની અશુદ્ધિઓ (foreign materials) જેવી કે ડાળાં-પાંદડાં-ફોતરાં વગેરે દૂર કરવામાં આવે છે. ઊનમાંથી પણ ચીકાશવાળી અશુદ્ધિ (wool grease) દૂર કરવા માટે પ્રક્રિયાઓ કરવામાં આવે છે. રેશમમાંથી ઘણા નાના તંતુ, નકામું રેશમ, સેરિસિન તથા ગુંદર (silk gum) વગેરે દૂર કરવા માટે પ્રક્રિયા કરવામાં આવે છે. કાચા શણને પણ બજારમાં મૂકતા પહેલાં સાફ કરવામાં આવે છે. માનવસર્જિત તંતુઓ કારખાનાંમાં બનાવવામાં આવતા હોવાથી તેમાં ભાગ્યે જ અશુદ્ધિઓ હોય છે. એકસરખી લંબાઈ, જાડાઈ, ઘનતા તથા ભેજગ્રાહકતા માટે સામાન્ય રીતે જુદા જુદા જથ્થાના (lots) કુદરતી તાંતણા સાથે મિશ્ર કરીને એકસરખો દોરો બનાવવામાં આવે છે. જ્યારે જુદા જુદા તંતુઓ ભેગા કરીને દોરો બનાવવાનો હોય ત્યારે જુદા પ્રકારના તંતુઓ મિશ્રિત કરવામાં આવે છે. તંતુઓ મિશ્રિત કરવાના હોય ત્યારે માનવસર્જિત તંતુઓ જરૂરી લંબાઈના ટોમાં મેળવી શકાતા હોઈ તેને મિશ્રિત કરવાની જરૂર નથી.
રૂ, ઊન, રેશમના ટૂંકા તંતુઓ (waste silk) અને માનવસર્જિત તંતુઓને કાર્ડિંગ પ્રક્રિયામાંથી પસાર કરવામાં આવે છે. આ પ્રક્રિયામાં એક-એક તંતુ પસાર કરવામાં આવે છે. તેમાં બાકી રહી ગયેલ અશુદ્ધિ દૂર થાય છે. કાર્ડિંગ પ્રક્રિયા તંતુઓનું એકસરખું પાતળું પડ બનાવે છે, જે ભેગું થઈને સળંગ, લાંબું, જાડું, વળ વગરનું દોરડું બની રહે છે; જેને પૂણી (sliver) કહેવામાં આવે છે.
બારીક દોરાના ઉત્પાદન વખતે કાર્ડિંગ બાદ કૉમ્બિંગ પ્રક્રિયા કરવામાં આવે છે, જેમાં બધા જ ટૂંકા તંતુઓ દૂર કરી માત્ર લાંબા તંતુઓ સમાંતર સ્થિતિમાં પૂણીમાં રખાય છે. તે સુંવાળા અને ચળકાટવાળા હોય છે. પૂણીને ખેંચીને પાતળી બનાવી સાધારણ વળ આપતાં તે રોવિંગના રૂપમાં મળે છે (roving એટલે પૂણી અને દોરા વચ્ચેની સ્થિતિ). હૅકલિંગ પ્રક્રિયા શણના તાંતણાને છૂટા પાડીને મજબૂત બનાવવાની પ્રક્રિયા છે અને તે કૉમ્બિંગ પ્રક્રિયા જેવી જ છે.
3. કાંતણ (spinning)
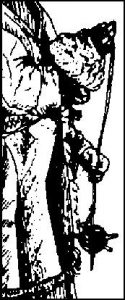
આકૃતિ 1 : પ્રાથમિક કાંતણપ્રક્રિયા
કાંતવાની પ્રાચીન રીતો : તંતુઓને ભેગા કરી એકીસાથે સરખા ગોઠવી, ખેંચી, વળ ચડાવી એક સળંગ દોરાના રૂપમાં ફેરવવાની પ્રક્રિયાને કાંતણ કહેવામાં આવે છે. ઓછી લંબાઈવાળા તંતુઓમાંથી કાપડનું વણાટ કરવા માટે કાંતણપ્રક્રિયા અનિવાર્ય છે. ત્રાક (spindle) અને ડિસ્ટાફ (ત્રાક જેવી જ બીજી વસ્તુ – તકલી) કાંતણ માટે મધ્ય યુગમાં અને તે પહેલાં વપરાતી હતી. ડિસ્ટાફ લાંબી પટ્ટી હતી, જેમાં તંતુઓનો જથ્થો ભરાતો અને છૂટી ફરતી અને લટકતી ભારે ત્રાક તેમાંથી જરૂરી લંબાઈના તંતુઓને ખેંચી લઈ કાંતણપ્રક્રિયાને ઝડપી બનાવતી હતી. કાંતનાર ત્રાકને જોરથી ફેરવે એટલે તંતુઓ પકડવા માટેની પટ્ટીમાંથી તંતુઓ બહાર ખેંચાઈને વળવાળા દોરાના રૂપમાં ફેરવાઈ જતા. પૂરતી લંબાઈનો દોરો કંતાતાં તેને ત્રાક પર વીંટી લેવામાં આવતો અને પ્રક્રિયા એ જ રીતે ફરી શરૂ કરવામાં આવતી. ઋગ્વેદમાં કાંતણ અને વણાટનું વર્ણન મળે છે. પુરાવા ઉપલબ્ધ થતા નથી. કાંતણચક્ર એટલે કે રેંટિયાની શોધ ભારતમાં થઈ હતી. મધ્ય યુગમાં તે યુરોપમાં દાખલ થયો. ત્યાં જૂની પદ્ધતિનું યાંત્રિકીકરણ થયું. જૂની ફરતી ત્રાક પર કાંતનારે તૈયાર દોરાને વારંવાર વીંટવો પડતો હતો. તે ક્રિયાને રેંટિયાના ઉપયોગથી યુક્તિપૂર્વક દૂર કરવામાં આવી. રેંટિયામાં કાંતણની પ્રક્રિયા દરમિયાન ડાબા હાથમાં પૂણી પકડી જમણા હાથે ચક્રને ફેરવવામાં આવે છે અને પૂણીને ખેંચવામાં આવે છે, દોરો તૈયાર થતાં ચક્રને ઊંધી દિશામાં ફેરવી ત્રાક અથવા તકલી પર વીંટવામાં આવે છે, જેથી કાંતણપ્રક્રિયા પૂર્ણ બને છે.
રેંટિયાના ઉપયોગથી અગત્યનો ફાયદો એ થયો કે દોરો બનાવવા માટે તેમાં પાતળી જગ્યાએ વધારે બળ આપી અને જાડી જગ્યાએ ખેંચાણ આપી તેમાં એકસરખાપણું લાવવાનું શક્ય બન્યું.
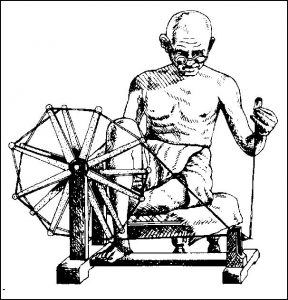
આકૃતિ 2 : ભારતીય રેંટિયો
રેંટિયામાં સુધારા : ઓગણીસમી સદી સુધી રેંટિયાનો વપરાશ ચાલુ રહ્યો, સોળમી સદીથી તેમાં સુધારાવધારા થતાં તે સેક્સની વ્હિલ તરીકે વિકાસ પામ્યો હતો, જેના વડે જાડા તારનું ઊન અને સૂતર પણ સળંગ રીતે કાંતવામાં આવતું હતું. ત્રણથી પાંચ રેંટિયા વડે એક સાળને માટે જરૂરી સૂતર બનાવી શકાતું; પરંતુ ‘કે’ના શટલ(ઊડતા કાંઠલા)ના ઉપયોગથી સૂતરની જરૂરિયાત વધી અને કાંતણ-યંત્રોની શોધની માગ વધી. જેમ્સ હારગ્રીવ્ઝની કાંતણ-શૃંખલા(spinning-jenny; patented 1770)થી એકસાથે વધુ ત્રાકોને ચડાવી શકાઈ; પરંતુ આ દોરા ફક્ત વાણા (filling yarn) તરીકે જ વાપરી શકાયા. સર રિચાર્ડ આર્કરાઇટે અગાઉની શોધ ધ્યાનમાં રાખીને હારગ્રીવ્ઝ જેનીના યંત્ર કરતાં વધુ મજબૂત દોરા બનાવી શકે તેવું વધુ સારું યંત્ર બનાવ્યું. સૅમ્યુઅલ ક્રૉમ્પટન નામના વૈજ્ઞાનિકે કાંતણના ત્રીજા યંત્રની શોધ કરી (1779), જે મ્યૂલ તરીકે ઓળખાય છે. તેને લીધે ઉત્પાદનક્ષમતામાં ઘણો જ વધારો થયો અને એક કારીગર એકસાથે 1,000 ત્રાકો ચલાવી શકતો. જાડા તથા પાતળા બન્ને પ્રકારના દોરા બનાવી શકાય તેવા યંત્રની શોધ થઈ. ક્રૉમ્પ્ટનના યંત્રે ઘણી સારી રીતે કાંતણક્રિયાને વધુ ઉત્પાદનક્ષમ બનાવ્યા બાદ બ્રિટન અને યુનાઇટેડ સ્ટેટ્સમાં કાંતણ-યંત્રો પર વિશેષ શોધ કરવામાં આવી.
આધુનિક કાંતણ : આધુનિક કાંતણમાં સાદી પૂણીને અથવા થોડા વળવાળી પૂણી(roving)ને યંત્રમાં મૂકવામાં આવે છે. યંત્રમાં ગતિવાળાં પૈડાં(rolls)ની મદદથી તેને ખેંચીને લાંબી અને પાતળી બનાવી, ત્રાક વડે તેમાં જરૂરી વળ આપી તાંતણાને એકબીજા સાથે ભેગા જકડી રાખવામાં આવે છે. દોરાની મજબૂતાઈ વળની ઘનતા (tightness) પરથી નક્કી થાય છે. આમ છતાં ખૂબ વધારે વળ આખરે દોરાને નબળો પાડીને તોડી નાખે છે. દોરાના વળને લીધે આંટા (spiral) બને છે, જે અંગ્રેજી મૂળાક્ષર Zમાં અથવા ગુજરાતી મૂળાક્ષર ‘ટ’માં વચ્ચે જે ઢાળ બને છે તેને મળતા આવે છે. આ પ્રકારના દોરાના વળને ઝેડ (Z) ટ્વિસ્ટ અથવા ‘ટ’ વળ કહે છે; જ્યારે આંટા અંગ્રેજી મૂળાક્ષર એસ (S) અથવા ગુજરાતી મૂળાક્ષર ‘ડ’ના વચ્ચેના ઢાળ જેવા બને ત્યારે તેને એસ (S) ટ્વિસ્ટ કે (ડ) વળ તરીકે ઓળખાવી શકાય. ક્રેપ પ્રકારના દોરા કાપડમાં ક્રિંકલ અસર (crinkled effect) ઉપજાવે છે, જેમાં ઘણા વધારે વળ આપેલા દોરા વાપરવામાં આવે છે. તૈયાર કાપડમાં પડછાયા જેવી અસર (shadow effect) ઊલટસૂલટ વળ (S અને Z) ચડાવેલા દોરા વાપરીને મેળવવામાં આવે છે, જેમાં પ્રકાશનું પરાવર્તન જુદા જુદા ખૂણેથી થતાં આવી અસર મળે છે.
ફાળકા પર વીંટવાની ક્રિયા (reeling and throwing) : રેશમના કોશેટામાંથી કાચા રેશમના તાંતણાઓને ફાળકા પર વીંટવાની ક્રિયાને રીલિંગ કહેવામાં આવે છે. રેશમ અથવા માનવસર્જિત તાંતણાને ભેગા કરી વળ ચડાવીને ચોક્કસ જાડાઈના દોરાના રૂપમાં ફેરવવામાં આવે છે તે ક્રિયાને થ્રોઇંગ કહેવામાં આવે છે.
દોરાના બાંધા (yarn packages) : સામાન્ય રીતે દોરાના વપરાશના હેતુ પર બાંધા બનાવવાની રીતનો આધાર છે. કાંતેલા દોરાને લાકડા, પૂંઠા અથવા પ્લાસ્ટિકમાંથી બનાવેલ ફરકડી (bobbin) પર વીંટવામાં આવે છે. ફરકડીમાં વચ્ચે કાણું હોય છે, જેથી કરીને ત્રાક અથવા તેના જેવા પકડમાં રાખવાના બીજા સાધનમાં તે બરાબર બેસી શકે છે. દોરાના ગાંઠા બનાવવા માટે સામાન્ય રીતે સ્પૂલ, કોન, સ્પ્રિંગ, ટ્યૂબ કે ચીઝનો ઉપયોગ કરવામાં આવે છે. સ્પૂલ નળાકાર આકારની કૉલરવાળી ફિરકી છે, જેની પર એકસરખા દોરા વીંટાતાં નળાકાર ગાંઠો બને છે. કોન શંકુ આકારની ફિરકી છે, જેમાં દોરાનો ગાંઠો શંકુ આકાર ધારણ કરે છે. સ્પ્રિંગ અગર ચીઝ પરના ગાંઠાને સીધેસીધો રંગવા માટેના મશીન પર ઉપયોગમાં લેવાય છે. દોરાની આંટીઓ કોઈ પણ આધાર વગર ગોળાકાર રૂપમાં હોય છે. પર્ન નળાકાર પીપ આકારનો દોરાનો ગાંઠો છે. તેમાં સામાન્ય રીતે વાણા(weft)ના તાર હોય છે, જે સાળ ખાતામાં શટલ ભરવા માટે ઉપયોગી છે, જ્યારે ક્વિલ્સ એ ભૂંગળી આકારનું એક છેડે પાતળું (ધારવાળું) બૉબિન છે. એ પણ વણાટમાં વપરાતા વાણાને વીંટાળવા માટે વપરાય છે. સાળ ખાતામાં તાણા(warp)ના તારને વીંટવા માટે જે નળાકાર લાકડાનું કે ધાતુનું સાધન વપરાય છે તેને બીમ કહે છે.
સૂતરના દોરાના પ્રકાર : સૂતરના દોરામાં વપરાયેલા તારની સંખ્યા ઉપર આધારિત વર્ગીકરણ. સૂતરને એક-દોરા (single or one play), એક કરતાં વધારે (plied), એક કે વધારે વળ (twisted) અથવા ગડી પાડેલા (folded) દોરા તરીકે, જાડા દોરા, પાતળાં દોરડાં, મજબૂત દોરડાં તથા હૉઝર પ્રકારના (hawser – રાંઢવું) દોરામાં વર્ગીકૃત કરી શકાય. એકવડો દોરો એ તંતુઓને ભેગા કરીને જરૂરી વળ આપી એકરૂપ કરી ભેગા કરેલા લાંબા તાંતણાને વળ આપીને અથવા વળ આપ્યા વગર અથવા પટ્ટીના રૂપમાં અથવા માનવસર્જિત તાંતણાને જરૂરી જાડાઈ આપી એક તાર (mono filament) તરીકે પણ બનાવી શકાય. કાંતેલો એક દોરો એ થોડા તંતુઓ ભેગા કરીને વળ ચડાવેલા ટૂંકા તંતુઓથી બને છે. તંતુઓને ભેગા રાખવા માટે જરૂરી વળ ચડાવવામાં આવે છે. આ વળ અંગ્રેજી મૂળાક્ષર એસ (S) અથવા ઝેડ(Z)ના રૂપમાં હોઈ શકે (આકૃતિ 3). સાદા દોરા જુદી જુદી ભાતના કાપડની બનાવટ માટે ઉપયોગી બને છે.
વળ ચડાવેલા દોરા (ply yarns) : સામાન્ય રીતે બે અથવા બે કરતાં વધારે સાદા દોરાને ભેગા કરીને વળ ચડાવેલા અથવા ગંઠેલા અથવા ગડી પાડેલા દોરા બનાવવામાં આવે છે. બે દોરાને ભેગા કરી વળ ચડાવી બેવડા વળનો દોરો (two-ply yarn) અને ત્રણ દોરાને ભેગા કરીને વળ ચડાવી ત્રેવડા વળનો દોરો (three-ply yarn) બનાવવામાં આવે છે. વળ ચડાવેલા દોરા સામાન્ય રીતે એકસરખા વળ પાડેલા સાદા દોરાને ભેગા કરીને મૂળ વળ કરતાં વિરુદ્ધ દિશામાં વળ ચડાવીને બનાવવામાં આવે છે, જ્યારે બંને દોરા અને વળ ચડાવેલાની વળની દિશા એક જ રાખવામાં આવે ત્યારે દોરામાં તાંતણાની પકડ સખત બને છે, જેને કારણે દોરા મજબૂત પરંતુ ઓછી નરમાશવાળા બને છે. વળ ચડાવેલા દોરા ઊંચી જાતનાં પોપલિન, સૂટિંગ, ફુલ વૉયલ, ભરત-ગૂંથણ વગેરે ઔદ્યોગિક કાપડની બનાવટમાં અને ખૂબ જ ઝીણા કાપડના વણાટ માટે ઉપયોગી છે.
વળ ચડાવેલા જાડા દોરા (cord yarn) : જાડા દોરા સામાન્ય રીતે પાતળા વળવાળા દોરાને ભેગા કરી વિરુદ્ધ દિશામાં વળ ચડાવીને બનાવવામાં આવે છે (આકૃતિ 3).
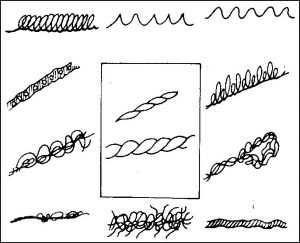
આકૃતિ 3 : વિવિધ ટેક્સ્ચ્યુરાઇઝ્ડ યાર્ન
મજબૂત દોરડાં (cable cord) : આમાં SZS (એસ-ઝેડ-એસ) રૂપના વળને અનુસરવામાં આવે છે, જેમાં ‘S’ (એસ) વળવાળા સાદા દોરા, ‘Z’ (ઝેડ) વળવાળા સાદા દોરા સાથે અને ત્યારપછી તેમાંથી ‘S’ પ્રકારના વળવાળા દોરાના રૂપમાં બનાવી શકાય અથવા ZSZ (ઝેડ-એસ-ઝેડ) રૂપમાં બનાવી શકાય. હૉઝર કોર્ડ SSZ (એસ-એસ-ઝેડ) અથવા ZZS(ઝેડ-ઝેડ-એસ)ના પ્રકારના વળ આપી બનાવી શકાય છે. જાડા દોરા એ દોરડા, દોરડી તેમજ રાંઢવા બનાવવા માટે, ઔદ્યોગિક કાપડ અથવા પોશાકનું કાપડ બનાવવામાં વપરાય છે.
નવતર પ્રકારના દોરા (novelty yarns) : નવતર પ્રકારના દોરા ઘણી ભાતના હોય છે, જેમાં ખાસ કરીને સ્લબ એટલે કે ટૂંકા તંતુઓનો સમૂહ જાણીજોઈને દોરાની બનાવટમાં દાખલ કરવામાં આવે છે. માનવસર્જિત રેસામાં આ પ્રકારની અસર ઉત્પાદન દરમિયાન તેની જાડાઈમાં ફેરફાર કરીને મેળવવામાં આવે છે. કુદરતી તંતુઓ, શણ (linen), ઊન, કેટલાક પ્રકારના રેશમના અસમાન તાંતણામાંથી બનાવેલ કાપડમાં આવતી અસામાન્ય અનિયમિતતાઓ રહેવા દઈને તૈયાર કાપડમાં ખાસ પ્રકારની ભાત ઉપજાવવામાં આવે છે. માનવસર્જિત રેસામાં ઉત્પાદન વખતે ફેરફાર કરી ‘ક્રિમ્પિંગ અને ટેક્ષ્ચ્યુરાઇઝિંગ’ જેવી ખાસ પ્રકારની અસરવાળા દોરા બનાવી કાપડમાં વાપરવામાં આવે છે.
ટેક્સ્ચ્યુરાઇઝ્ડ યાર્ન (વળાંકવાળા અથવા કદવાળા દોરા) : ટેક્સ્ચ્યુરાઇઝ્ડ યાર્ન બનાવવાની પ્રક્રિયા માનવસર્જિત રેસા માટે સૌપ્રથમ અપનાવવામાં આવી હતી, જેને લીધે તેની પારદર્શકતા, સરકાઉપણું અને તંતુની ગોળી થવાને લીધે સપાટીનું ખરબચડાપણું (pilling tendency – ઘસારાને કારણે તંતુઓના છેડા ખેંચાઈને કાપડની સપાટી ઉપર ગોળીઓ ચોંટી જાય તેવી અસર ઉત્પન્ન કરે છે) ઓછાં થાય છે. આ પ્રક્રિયાથી દોરા અપારદર્શક, સુંદર દેખાવવાળા અને કદવાળા બને છે; હૂંફ (warmth) આપવા અને ભેજશોષકતા(absorbency)ના તેના ગુણધર્મોમાં વધારો થાય છે. ટેક્ષ્ચ્યુરાઇઝ્ડ યાર્ન સામાન્ય રીતે માનવસર્જિત લાંબા રેસા હોય છે જે ખાસ પ્રકારના પોત (texture) અને સુંદરતા માટે કાપડની બનાવટમાં વપરાય છે.
કદવર્ધન (bulking) : કદવર્ધનની પ્રક્રિયાથી દોરામાં હવા ભરાઈ શકે તેવી જગ્યા ઉત્પન્ન થાય છે, જેને કારણે દોરાની ભેજશોષકતા અને તેમાંથી હવાની અવરજવરના ગુણધર્મમાં વધારો થાય છે. સામાન્ય રીતે દોરામાં વળાંકો અને તરંગો (crimp and waviness) ઉત્પન્ન કરીને તેના કદ(bulk)માં વધારો કરવામાં આવે છે. આવા ક્રિમ્પ્ડ યાર્નમાં અમુક અમુક અંતરે દોરાને ખેંચી વાળની લટ જેવા વળાંક (curling) આપવામાં આવે છે અને ગોળાકાર ગાળા (coiled loop) જેવી અસર ઉપજાવવામાં આવે છે. આ અસર કુદરતમાં મળતા ઊનના રેસાને મળતી આવે છે. આ પ્રકારની અસરો સામાન્ય રીતે ગરમીથી અને કેટલીક વાર રાસાયણિક પ્રક્રિયાઓ વડે મેળવવામાં આવે છે. 1970 પહેલાં કદવાળા દોરા (bulk yarn) ખોટા વળ(false twist)ની રીતથી બનાવવામાં આવતા હતા; એમાં લાંબા તાંતણાને વળ ચડાવી તેને ગરમીથી ઘન (set) બનાવી, વળ ઉકેલી અને ગરમીથી ફરી ઘન બનાવવામાં આવતા; આમ ગરમીની અસરથી વળને ઘન બનાવવામાં આવતા અથવા દૂર કરવામાં આવતા હતા. નાયલૉનના તાંતણાનું કદ વધારવા માટે પૂરણપેટી(stuffer box)ની રીત વાપરવામાં આવે છે; જેમાં દોરાને ગરમ નળીમાં દાખલ કરવામાં આવે છે જ્યાં વાંકાચૂકા (zigzag) વળાંક ઉત્પન્ન કરી દોરાને ધીમે ધીમે પેટીના બીજા છેડેથી બહાર કાઢવામાં આવે છે. ગૂંથી અને ઉકેલવાની રીત(knit-deknit process)થી સંશ્લેષિત દોરા તૈયાર કરવામાં આવે છે. ગરમીની અસરથી તેમાં ગૂંથવાથી ઉત્પન્ન થયેલા ગાળા(loops)ને સ્થાયી બનાવવામાં આવે છે, અને દોરાને છૂટા પાડી ઓછા વળ આપવામાં આવે છે. આમ કાપડમાં જરૂરી પોત મેળવવા માટે આ પ્રકારના દોરાનો ઉપયોગ થાય છે.
રાસાયણિક રીતે વધારે-ઓછી સંકોચનશીલતા (shrinkage) ધરાવતા રેસાને એક જ દોરામાં ભેગા કરી તેની ધોલાઈ (washing) કરવાથી અથવા વરાળ-બાફ (steaming) આપવાથી વધારે સંકોચન-શીલતાવાળા તાંતણા વિશેષ સંકોચાઈને તાંતણાને ખેંચ્યા વગર કદવર્ધનની અસર ઉપજાવે છે. દોરાના કદમાં હવાના દબાણથી પણ ફેરફાર કરવામાં આવે છે. એમાં દોરાને એક પેટીમાં ભરીને તેમાં ઊંચા દબાણવાળી હવા છોડવાથી પ્રત્યેક તાંતણો છૂટો થઈને બધા નાનામોટા ગાળામાં વહેંચાઈ જાય છે જેથી તેના કદમાં વધારો થાય છે.
સ્ટ્રેચ યાર્ન : ખેંચાઈ શકે તેવા માનવસર્જિત લાંબા રેસાને સ્ટ્રેચ યાર્ન કહે છે; જે એકદમ વધારે વળ ચડાવેલા તથા ગરમીની પ્રક્રિયાથી ઘન (heat set) કરેલા અને વળ ઉકેલેલા, આંટા જેવા વળાંકવાળા અને સ્થિતિસ્થાપકતાના ગુણવાળી રચનાવાળા દોરા છે.
સ્થિતિસ્થાપક તાંતણા (elastomeric fibres) : સ્પૅનડેક્સ (spandex) વધારે પ્રમાણમાં સ્થિતિસ્થાપક રેસામાંથી બનાવેલ હોય છે. તેમાં મુખ્યત્વે પૉલિયુરેથીન હોય છે. (સ્પૅનડેક્સ તેના ઉત્પત્તિસ્થાન પરથી ઉદભવેલ નામ છે.) આવરણ વગરના (uncovered) રેસા કાપડ બનાવવા માટે ઉપયોગમાં લઈ શકાય છે પરંતુ તેમાંથી બનતું કાપડ રબર જેવું લાગે છે. આથી મોટાભાગના સ્થિતિસ્થાપક રેસા દોરાના અંદરના મુખ્ય ભાગ તરીકે વપરાય છે અને જે ખેંચી શકાય નહિ તેવા અથવા અસ્થિતિસ્થાપક કુદરતી અથવા માનવસર્જિત રેસાઓ વડે આવરી લેવામાં આવે છે. આમ છતાં કુદરતી રેસાને કેટલીક પ્રક્રિયા વડે સ્થિતિસ્થાપક બનાવીને તેમાં જરૂરી ગુણધર્મો પણ યુક્તિ વડે પૂરા પાડી શકાય છે, જેથી સ્થિતિસ્થાપક સૂતરનો અંદરના ભાગ (core) તરીકે ઉપયોગ કરવાની જરૂર પડતી નથી.
જરીના તાર – ધાતુના તાર (metallic yarns) : આ પ્રકારના તાર-સર્જિત તાંતણા, જેવા કે પૉલિયેસ્ટરની પાતળી પટ્ટીઓ પર ધાતુના ઢોળ ચડાવીને બનાવવામાં આવે છે. બીજી રીતમાં ઍલ્યુમિનિયમ ધાતુને બે પાતળાં પડ વચ્ચે સંયોજિત (sandwich) કરીને બનાવવામાં આવે છે. જરીનો તાર (ધાતુનો તાર) એ મધ્ય ભાગે માનવસર્જિત દોરા અથવા કુદરતી દોરાને રાખીને ફરતા ધાતુના પાતળા પડના તાર વીંટીને પણ બનાવાય છે; જેમાં ધાતુનો ભાગ બહારની સપાટી બનાવે છે.
ઉપયોગિતા પર આધારિત વર્ગીકરણ : કાપડની બનાવટમાં વપરાતા દોરા : વણાટવાળું અને ગૂંથેલું કાપડ બનાવવા માટે કોઈ પણ પ્રકારના દોરા ઉપયોગમાં લઈ શકાય છે. વણાટમાં ઊભા તાર એટલે કે તાણા વધુ દબાણ કે ઘસારો સહન કરે છે, તેથી સામાન્ય રીતે તે આડા તાર કે વાણાની સરખામણીમાં વધુ મજબૂત વળ ચડાવેલા, એકસરખી જાડાઈના તથા લીસા હોય છે. વણાટ દરમિયાન જે જોર અને ઘસારો પડે છે તેને પહોંચી વળવા માટે તાણા પર કાંજી (starch) ચડાવવામાં આવે છે, તેને કાંજીની પ્રક્રિયા (sizing process) કહેવાય છે. વણાટ દરમિયાન વાણા પર નહિવત્ જોર કે ઘસારો લાગે છે.
વણાટવાળા જાડા દોરા કે પટ્ટીના જેવી અસર કાપડમાં ઉપસાવવા માટે તાણા અને વાણાના વ્યાસમાં ફેરફાર હોય તેવા દોરા વાપરવામાં આવે છે. જુદા જુદા ઉદગમસ્થાન(origin)માંથી પ્રાપ્ત કરેલા તાંતણામાંથી બનાવેલા દોરા, જુદા જુદા વળ ચડાવેલા દોરા અથવા જરીના તારના ઉપયોગ વડે કાપડમાં વિશિષ્ટ પ્રકારની ભાત ઉપસાવવામાં આવે છે. ગૂંથેલા કાપડમાં ઇચ્છા મુજબ કુમાશ જળવાઈ રહે તે ર્દષ્ટિથી તે માટેના દોરા સુંવાળા અને ઓછા વળવાળા હોય છે.
હસ્તઉદ્યોગમાં ગૂંથણ માટે વપરાતું સૂતર સામાન્ય રીતે બે અથવા તેથી વધારે દોરાને વળ આપી બનાવેલ હોય છે. એમાં નીચેના પ્રકારના દોરાનો સમાવેશ કરી શકાય; જેવા કે,
કદવાળા દોરા (fingering yarns) – સામાન્ય રીતે બે કે ત્રણ દોરાને ભેગા કરી વળ આપી બનાવેલ આ દોરા વજનમાં હલકા અને એકસરખા વ્યાસવાળા અથવા જાડાઈના હોય છે અને તૈયાર પોશાક બનાવવામાં તેનો ઉપયોગ થાય છે.
જર્મન ટાઉન દોરા – ચાર દોરાને વળ આપી બનાવેલ આ દોરા પોચા તથા પ્રમાણસર વજનના હોય છે અને તે ગરમ ધાબળા તથા સ્વેટર બનાવવામાં વપરાય છે.
શેટલૅન્ડ દોરા – બે દોરાને વળ આપી બનાવેલ આ દોરા ઝીણા, પોચા, રુવાંટીવાળા અને વજનમાં હલકા હોય છે; જે નાનાં ભૂલકાં, બાળકો વગેરેનાં ગરમ કપડાં તથા શાલ બનાવવા વપરાય છે.
ગૂંથવા માટેના ઊની દોરા – આ દોરા વધારે વળ ચડાવેલ ભારે, પોચા પરંતુ બરડ (crisp) નહિ અને ગરમ કાપડની બનાવટમાં વપરાતા દોરા કરતાં જુદા જ પ્રકારના હોય છે; સ્વેટરની બનાવટમાં તે ઉપયોગી છે.
ઝેફર દોરા ઊન અથવા બીજા રેસા સાથે મિશ્રિત ઊનમાંથી બનાવેલા ઘણા ઝીણા અને નરમ તથા ઓછા વળ આપી બનાવેલ દોરા. એ હલકાં ગરમ વસ્ત્રો બનાવવામાં વપરાય છે.
ભરતકામમાં વપરાતા દોરા – સામાન્ય રીતે એક કરતાં વધારે દોરાને ઓછા વળ આપીને અથવા જાડા દોરા રેશમ અથવા કૃત્રિમ રેશમ(rayon)માંથી બનાવવામાં આવે છે. અંકોડી(crocheting)ના કામમાં વપરાતા દોરા ઢીલા અને જાડા સૂતરના હોય છે જ્યારે ગૂંથવા કે તૂણવા માટે વપરાતા દોરા (darning yarns) ઓછા વળ આપીને કાંતેલા હોય છે.
સીવણ માટેના દોરા – સીવવા માટેના દોરા બે કે વધારે દોરાને ખૂબ જ પાસે પાસે સરખો વળ ચડાવીને દોરાનો વર્તુલાકાર આડો છેદ (circular cross section) બને તે પ્રમાણે દોરીરૂપે બનાવવામાં આવે છે. ઔદ્યોગિક અથવા ઘરમાં સીવવાના સંચામાં અને હાથથી સીવણ માટે વપરાતા દોરા, સોયમાં પરોવી શકાય તેવા સુંવાળા તથા ખેંચાણ સહન કરી શકે તેટલી મજબૂતાઈ ધરાવતા સ્થિતિસ્થાપક હોવા જરૂરી છે. સીવણ દરમિયાન થતા ઘસારા અને બળને લીધે તથા ઘરમાં અને ધોબીને ત્યાં કપડાં ધોતી વખતે ટાંકામાંથી તે તૂટી ન જાય તેવા હોવા જરૂરી છે.
ખાસ હેતુ માટેના દોરાને જરૂરી પ્રક્રિયા વડે તૈયાર કરવામાં આવે છે. ઉદાહરણ તરીકે, પાણી-પ્રતિરોધક કાપડમાંથી કપડાં બનાવવા માટે પાણી-પ્રતિરોધકતા ધરાવતા દોરા વાપરીને સીવવામાં આવે છે. સામાન્ય રીતે કાંતણ બાદ દોરાને ખાસ પ્રક્રિયામાંથી પસાર કરવામાં આવે છે. ફરકડી પર વીંટી, ફરકડીના છેડાના ભાગે દોરાનું કદ દર્શાવવામાં આવે છે. દોરાનાં બીજાં ખાસ જરૂરી પરિમાણ જે તે પ્રદેશ અથવા વિસ્તારમાં પ્રચલિત પદ્ધતિ પ્રમાણે પણ દર્શાવવામાં આવે છે.
રેશમના દોરાના પાતળાપણા (fine diameter) સાથે સ્થિતિસ્થાપકતા (elasticity) અને મજબૂતાઈ સંકળાયેલાં છે, જે કાયમી સ્થિતિસ્થાપકતાનો ગુણધર્મ ધરાવતા હોવાથી ઊન અને રેશમના સીવણકામ માટે યોગ્ય છે. બટન-બોરિયાં લગાવવા માટે અને ભરતકામમાં વપરાતા રેશમી દોરા સામાન્ય સીવવામાં વપરાતા રેશમના દોરા કરતાં ત્રણગણા જાડા, સુંવાળા ને ચળકતા તથા મજબૂત હોય છે.
રૂના દોરા – જે કાપડ વનસ્પતિજન્ય (plant origin) રેસામાંથી બનાવવામાં આવ્યું હોય, એટલે કે રૂ, શણ તથા કૃત્રિમ રેશમ (viscose rayon), તેને સીવવા માટે રૂના દોરા યોગ્ય છે, કારણ કે તેમના સંકોચનશીલ (shrinkage) ગુણધર્મ લગભગ સરખા છે. સંશ્લેષિત રેસા(synthetic yarns)ની સંકોચનશીલતા ખૂબ જ ઓછી હોવાથી સુતરાઉ કાપડ સીવવા માટે તે યોગ્ય ગણાતા નથી. દોરાની ખેંચાણશક્તિ (stretch) વણાટવાળા કાપડ માટે યોગ્ય છે પરંતુ ગૂંથેલા તેમજ વધારે સ્થિતિસ્થાપકતાવાળા કાપડ માટે વધારે ખેંચાણશક્તિ ધરાવતા દોરા જરૂરી છે.
નાયલૉનના દોરા – તે મજબૂત અને વધુ સ્થિતિસ્થાપક હોય છે અને સંકોચાતા નથી, તેથી ખેંચાણ પડે તેવા કાપડ અથવા ખેંચાઈ શકે તેવાં કપડાં માટે તે વધારે યોગ્ય છે.
પૉલિયેસ્ટરના દોરા પણ નાયલૉન જેવા જ ગુણધર્મો ધરાવે છે, તેથી તે પહેલાંથી સંકોચાયેલા (pre-shrunk) કાપડ અને સંશ્લેષિત રેસામાંથી બનાવેલ કાપડ માટે યોગ્ય છે.
દોરાને માપવા માટેની પદ્ધતિઓ : દોરાનું માપ સામાન્ય રીતે તેની લંબાઈ તથા વજનના સંબંધ (અથવા વ્યાસ) પરથી દોરાના નંબર, કાઉન્ટ અથવા કદ (size) વડે દર્શાવવામાં આવે છે. દુનિયાના જુદા જુદા પ્રદેશોમાં દોરાના માપ માટે જુદી જુદી રીતો શોધાઈ હોવાથી તેમાં નિયમિતતા જળવાઈ નથી.
આડકતરી પદ્ધતિ – આ પદ્ધતિમાં એકમ વજનમાંથી બનેલા તારની લંબાઈને આધારભૂત ગણી જેમ તાર પાતળા (finer) તેમ તે ઊંચા આંકના ગણવામાં આવે છે. મોટાભાગના જે દેશોમાં નાના તાંતણાનો ઉપયોગ દોરા બનાવવા માટે કરાય છે, ત્યાં દોરાનું માપ તેના ચોક્કસ વજનના પ્રમાણમાં લંબાઈના સંબંધથી નક્કી કરવામાં આવે છે. ઉદાહરણ તરીકે એક પાઉન્ડ એકમ વજનમાંથી જાડા તાર(coarser yarn)ની સરખામણીમાં પાતળા તાર વધારે લંબાઈના બને છે, એટલે કે ઊંચો આંક (higher count) એ પાતળો તાર છે એમ દર્શાવે છે. કદનો આંક (size number) એ એક પાઉન્ડ દોરાના વજન માટે જોઈતા દોરાની લંબાઈ દર્શાવે છે. બ્રિટન અને યુનાઇટેડ સ્ટેટ્સમાં એક પાઉન્ડ વજનના દોરામાંથી બનતી આંટીઓની સંખ્યા પર આધારિત પદ્ધતિ અમલમાં છે. દાખલા તરીકે, જો એક પાઉન્ડ વજનમાં 840 વારની સૂતરની 80 આંટી થાય તો, દોરાનો કાઉન્ટ 80 ગણવામાં આવે છે (80s).
- સૂતર અને રેશમ માટે 840 વારની આંટી.
- શણ માટે 300 વારની આંટી.
- ઊન માટે 256 વારની આંટી.
- વર્સ્ટેડ ઊન માટે 560 વારની આંટી.
આખા વિશ્વમાં, એક કિલોગ્રામ વજનમાંથી બનતી 1,000 મીટર (1 કિલોમિટર) લંબાઈની આંટીઓની સંખ્યા દર્શાવતી ઉપયોગી પદ્ધતિ અમલમાં છે.
ડેનિયર પદ્ધતિ – આ પદ્ધતિ આંતરરાષ્ટ્રીય ધોરણે, રેશમ તથા માનવસર્જિત રેસા અને દોરાનું કદ માપવા માટે અપનાવવામાં આવે છે. તે રેશમના તાંતણા માપવા માટેની જૂની પદ્ધતિ પરથી ઘડી કાઢવામાં આવેલી છે (એમાં 1,000 વારને ડ્રામમાં વજન તરીકે આધારભૂત ગણવામાં આવતા). ડેનિયર આંક એ 9,000 મીટર લંબાઈના તાંતણા અથવા દોરાનું ગ્રામમાં વજન દર્શાવે છે. ઉદાહરણ તરીકે, 9,000 મીટર લંબાઈના દોરાનું વજન 15 ગ્રામ થાય તો તે 15 ડેનિયરના છે એમ કહેવાય. એ જ રીતે 9,000 મીટર લંબાઈના દોરાનું વજન 100 ગ્રામ થાય તો તે 100 ડેનિયરના છે એમ કહેવાય; જે 15 ડેનિયરના દોરા કરતાં જાડા છે. આથી ઓછો આંક એ ઝીણા દોરા છે તેમ નિર્દેશ કરે છે. આ પદ્ધતિ ટૂંકા તાંતણા માટે ઉપયોગી નથી, કારણ કે તેમના વધારે વજનને લીધે ઘણા મોટા આંકનો નિર્દેશ કરવો પડે છે.
ટૅક્સ પદ્ધતિ – આ પદ્ધતિ સાર્વત્રિક પદ્ધતિ તરીકે મૂળ 1873માં ઘડી કાઢવામાં આવી હતી. તે ટૂંકા તંતુઓ, ટૂંકા દોરા અને લાંબા તાંતણાને માપવા માટે ઉપયોગી છે; તે 1 કિલોમિટર લંબાઈના તારનું ગ્રામમાં વજન દર્શાવવાની પદ્ધતિ પર આધારિત છે.
4. કાપડનું ઉત્પાદન
દોરા અને કેટલીક વખત તાંતણાને એકબીજામાં ભરાવી કાપડમાં રૂપાંતરિત કરવામાં આવે છે. કાપડના ગુણધર્મ તેમાં વપરાયેલ દોરાની જાત (material) તથા પદ્ધતિ પરથી નક્કી થાય છે. મોટાભાગે હાલમાં કાપડ દોરા પસાર કરવાની (interlacing) પદ્ધતિઓ જેવી કે વણાટ અથવા ગૂંથણથી બનાવવામાં આવે છે. વણાટપદ્ધતિ કાપડના ઉત્પાદન માટે મુખ્ય છે, જેમાં પાયાના વણાટ તરીકે સાદું વણાટ [દા.ત., ખાટલામાં ભરાતી પાટી અથવા દોરી (plain or tabby weave)], ટ્વિલ, સાટીન અને ભપકાદાર વણાટ (fancy weave) કે જેમાં પાછળ રૂંવાંવાળું (pile), જૅકાર્ડ, ડૉબી અને જાળી(gauze)નો સમાવેશ થાય છે. ગૂંથેલા કાપડનું મહત્વ ઝડપથી વધી રહ્યું છે, જેમાં તાણા અને વાણાના બનાવેલ રાશલ (raschel) અને ટ્રાઇકૉટ (tricot) એમ કાપડ-ગૂંથણીના બે પ્રકાર છે. બીજા પ્રકારમાં જાળી, વેણી (braid) અને પટ્ટીના રૂપમાં ગૂંથેલ કાપડને ગણાવી શકાય. વણાટ સિવાયના કાપડ(non-woven fabric)ને પણ મહત્વ મળતું જાય છે, જેમાં રેસાને બાંધીને અથવા દબાણથી ઊની કાપડ જેવી અસર ઉપજાવી કાપડ બનાવવામાં આવે છે. રેસાને ચોંટાડીને (laminating) પણ કાપડ બનાવવામાં આવે છે. આધુનિક શોધ પ્રમાણે સોય-વણાટ (needle weaving) અને સીવણ-ગૂંથણ (sewing-knitting)થી પણ કાપડ બનાવવામાં આવે છે.
વણેલું કાપડ : દોરાને નિયમિત ક્રમમાં પસાર કરી બનાવાતા કાપડને વણેલું કાપડ અને પદ્ધતિને વણાટ (weave) કહેવામાં આવે છે. વણાટની પ્રક્રિયામાં તાણા અને વાણાના દોરાને એકબીજા સાથે ચોક્કસ ક્રમમાં ગોઠવવાથી વણાટનું બંધારણ નક્કી થાય છે. તાણા અને વાણા એકબીજાને સમાંતર અથવા એકબીજાને લંબરૂપે રહે તે જરૂરી નથી; પરંતુ વણાટનું બંધારણ સામાન્ય રીતે બે ભાગનું બનેલું હોય છે, જેમાં બન્ને ભાગ વળી શકે તેવા અને એકબીજાને કાટખૂણે ઓળંગતા હોય છે. વણાટ એ તાણા અને વાણાની ગૂંથણીની રીતથી જાળી અને અંબોડી (braiding) (જેમાં પાછળથી એ જ દોરાનો ઉપયોગ થાય છે)થી જુદું પડે છે. આ ઉપરાંત વણાટ અને ગૂંથણમાં ભૌમિતિક ફરક એ છે કે વણાટમાં દોરા ઓછા અંશના ખૂણે પસાર થાય છે, જ્યારે ગૂંથણમાં સામાન્ય રીતે આનાથી વિરુદ્ધ હોય છે. વણેલું કાપડ ઉપયોગી ગુણધર્મો ધરાવે છે. આ ગુણધર્મો કાપડમાં વપરાયેલ તાણા અને વાણાના બંધનને લઈને નહિ, પરંતુ તેમની ભૌમિતિક રચના તથા ઘર્ષણના લીધે છે.
કાપડ પર વિવિધ પ્રકારની ભાત ઉપસાવવાની રીતો : કાપડમાં વપરાતા દોરા, તેને ઓપ આપનાર પ્રક્રિયા તથા તેના બંધારણની પસંદગી કરી ભાત બનાવનાર (textile designer) તેની પર જુદી જુદી ભાત ઉપજાવી, ઘણા પ્રકારનું કાપડ બનાવી શકે છે. દોરાનું જાડાપણું કે પાતળાપણું, તેની કુમાશ, તાંતણાનો સમન્વય, વળ, રંગ વગેરેની ઘણી અસર ઓપ આપેલા તૈયાર કાપડ પર જોવામાં આવે છે. ઓપ આપવાની પદ્ધતિ (finishing process) ઘણા પ્રકારની છે, એમાં કાપડની બિનજરૂરી રુવાંટી કાપીને કે બાળીને દૂર કરવાની પદ્ધતિથી માંડીને અઘરી અને ગૂંચવણભરી રાસાયણિક પ્રક્રિયાઓ આવી જાય કે જેમાં સૂતરના અપારદર્શક કાપડને પારદર્શક બનાવી અને કાયમી કડક બનાવવાની રીત (દા.ત., organdy) વગેરેનો સમાવેશ થાય છે.
વણાટવાળા કાપડના ગુણધર્મ નક્કી કરવા માટે બંધારણીય અથવા વણાટપદ્ધતિ મુખ્ય કારણરૂપ છે. વણાટ માટે મુખ્ય ત્રણ પદ્ધતિઓ ગણાવી શકાય – (1) સાદી અથવા ટૅબી, (2) ટ્વિલ અને (3) સાટીન. અઘરી બંધારણ અથવા વણાટપદ્ધતિમાં પાયાની રીતોનો સમન્વય કરવામાં આવે છે તેમજ ઊંચી હાથકારીગરી અથવા યાંત્રિક સાળ વાપરવામાં આવે છે; આમાં એક કરતાં વધારે પડવાળી (multiple plane) તેમજ જુદી જુદી ભાત ઉપજાવનાર વણાટપદ્ધતિઓ(pile, inlaid, gauze)ને અઘરી ગણવામાં આવે છે. વણાટની બંધારણની પદ્ધતિઓ બાદ કરતાં, તાણાની ગોઠવણીમાં ફેરફાર કરીને, ખેંચાણ આપી કાપડના દેખાવમાં ફેરફાર કરવામાં આવે છે, જેથી કાપડ ઘટ્ટ અથવા આછું અને વધુ અથવા ઓછી નિયમિતતાવાળું બનાવી શકાય છે.
જે રીતે સંગીતનાં પરિમાણ સંગીત બનાવનારના વિચાર સંકેત દ્વારા પ્રદર્શિત કરે છે તેવી જ રીતે વણાટના બંધારણ વિશેની માહિતી વણાટના કારીગરના વિચારોને કાગળ પર બિન્દુરચના (point paper plans) અથવા વણાટના નિર્દેશિત સંકેત (weave drafts) દ્વારા દર્શાવવામાં આવે છે. વણાટના નિર્દેશિત સંકેત, ગ્રાફપેપર પર વણાટના એકમનો નિર્દેશ કરતા રેખાંકન સ્વરૂપમાં હોય છે. આ માહિતી સાળખાતાના કારીગરોને અથવા ઉદ્યોગના કુશળ માણસોની સારણીમાં તાણાની ગોઠવણી, ફણી અને શેડિંગ પ્રક્રિયાના ક્રમ (shedding order) નક્કી કરવામાં ઉપયોગી બને છે.
વણાટપ્રક્રિયા : વણાયેલું કાપડ સામાન્ય રીતે એક દિશામાં બીજી દિશા કરતાં ઘણું લાંબું હોય છે. લંબાઈને સમાંતર (lengthwise) રહેલા તારને તાણો અને તાણાની સાથે સંયોજાઈને પહોળાઈને સમાંતર જતા તારને વાણો કહેવામાં આવે છે. (જેના પર્યાય તરીકે ‘weft’, ‘filling’, ‘woof’ અને ‘shoot’ અથવા ‘shute’ શબ્દો છે.) તાણાનો દોરો અચોક્કસ લંબાઈનો હોય છે. તેને છેડા તરીકે ઓળખવામાં આવે છે. વાણાની લંબાઈ કાપડની એક કિનારીથી બીજી કિનારી સુધીની હોય છે. તેને પનો (પિક) કહે છે. ક્રમિક પિકની લંબાઈ ક્રમિક ગોઠવાયેલા અને એક જ દોરાના સળ પડીને ગોઠવાયેલા વાણાની લંબાઈને અનુરૂપ હોય છે.
વણાટની બધી જ પ્રક્રિયામાં વાણો પસાર કરતાં પહેલાં, બનેલા કાપડથી થોડા અંતરે બધા જ તાણાને બે પડમાં છૂટા પાડવામાં આવે છે. આ પ્રક્રિયાને શેડિંગ ક્રિયા – બારું બનાવવાની ક્રિયા કહે છે; જ્યારે બે પડ વચ્ચે જગ્યા થાય તેને શેડ કહે છે (આકૃતિ 4 અ). ત્યારબાદ આ શેડમાં વાણાને દાખલ કરવામાં આવે છે. આ રીતે વાણો પસાર કરવાની પ્રક્રિયાને પિકિંગ કહે છે (આકૃતિ 4 આ). તાણાના પડમાં રહેલા બધા જ તાર અથવા થોડા તાર પહેલાંની જગ્યા કરતાં બદલાય છે અને નવા શેડ વણાટના બંધારણ મુજબ બનાવવામાં આવે છે. આમ વાણો, તાણાના બે પડ વચ્ચે ગોઠવાય છે.
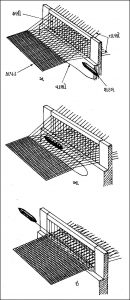
આકૃતિ 4 : અ, આ, ઇ : વણાટપ્રક્રિયાની અવસ્થાઓ
તાણાના પડ અને કાપડના સંયોજન પાસે વાણાને લાવવાની અને પહેલાંના વાણા કરતાં ઇચ્છા મુજબના યોગ્ય અંતરે વાણાને ગોઠવવાની ક્રિયાને ‘બીટ’ અથવા ‘બીટિંગ અપ’ કહે છે (આકૃતિ 4 ઇ). આ ક્રિયા શેડ બદલાય તે વખતે થાય છે અને નવો શેડ બને તે પહેલાં પૂરી કરવામાં આવે છે. આમ વણાટચક્રના પ્રાથમિક કાર્યમાં શેડ બનાવવાની, વાણો પસાર થવાની અને બીટિંગની ક્રિયા ક્રમમાં આવે છે, જેમાં તાણાને વારાફરતી ગોઠવીને વાણો પસાર કરી જે ભૌમિતિક રચના, તાણા અને વાણાના એકથી બીજા છેડાની વચ્ચે બને છે તે જોવા મળે છે; દા.ત., ખાટલામાં તાણેલી પાટી કે દોરીથી બનતી રચના. આ વણાટક્રિયાને આંતરપટ્ટા ગૂંથણી (interlacing) પદ્ધતિ તરીકે ગણાવી શકાય.
સાળનો વિકાસ : કોઈ પણ યુક્તિ કે યંત્ર વડે જે તાણાને ખેંચાણમાં રાખીને શેડ બનાવે તેને અંગ્રેજીમાં ‘લૂમ’ (મધ્ય યુગમાં વપરાતો શબ્દ lome – ‘tool’) તરીકે ઓળખવામાં આવે છે. સાળ ઘણા પ્રકારની જોવા મળે છે; જેમાં અસલ ઢબથી ઉપયોગમાં લેવાતા દોરડા, સળિયા તથા વાંસના બંધારણથી માંડીને સ્ટીલ અને લોખંડનાં બનાવેલાં આધુનિક યંત્રો સુધી હોય છે.
પ્રાયોગિક ધોરણની ચોક્કસ સાળને બાદ કરતાં તાણાના શેડને રાચ(heddle)ના ઉપયોગથી બનાવવામાં આવે છે. અસલી ઢબની થોડી સાળમાં સાદા કાપડની બનાવટમાં રાચનો ઉપયોગ એકાંતરા તાણાના તારને માટે કરવામાં આવતો હતો. સામાન્ય રીતે રાચનો ઉપયોગ તાણાના એક કે વધુ તાર માટે પણ કરી શકાય છે. રાચ જાડા દોરા, ધાતુના તાર અથવા પાતળી પટ્ટીરૂપે તાણાના છૂટા નહિ પડેલ પડને લંબરૂપે (વપરાશ વખતની સ્થિતિ) ગોઠવાયેલ હોય છે. આધુનિક સાળ પર તેની મધ્યમાં ઝીણા કાણાવાળી રાચ વાપરવામાં આવે છે. રાચના કોઈ પણ એક છેડાને પકડીને ઊંચો કે નીચો કરવામાં આવે તો તાણાને પડથી છૂટા પડતો જોઈ શકાય છે. રાચને પકડી રાખતા ચોકઠાને હાર્નેસ કહે છે.
મોટાભાગની સાળમાં વાણો શટલ વડે પસાર કરવામાં આવે છે, જે અંદરની તરફથી પોલું હોય છે. તેમાં વાણાનો દોરો વીંટેલું બૉબિન મૂકી શકાય અને સહેલાઈથી પસાર થઈ શકે તેવું હોય છે. વાણાનો દોરો તેમાં આપેલ ઝીણા કાણા દ્વારા અંદરથી બહાર તરફ ઊકલી શકે છે. શટલ તાણાનાં બે પડ વચ્ચેથી પસાર થાય છે ત્યારે તેની પાછળ વાણાને મૂકતું જાય છે.
નિયમિત ક્રમમાં ધાતુના ઝીણા તારને સમાંતર ગોઠવીને બન્ને બાજુ બંધ કરી બનાવેલ રચના ફણી તરીકે ઓળખાય છે. તેનાથી બીટિંગ ક્રિયા અસરકારક બને છે. ફણીને તાણાના પડને લંબરૂપે ગોઠવવામાં આવે છે. તે રાચ અને તાણા તથા કાપડની વચ્ચે આગળપાછળ થઈ શકે છે. ફણીના બે ક્રમિક તારના ખાનામાંથી એક કે વધારે તાર પસાર કરવામાં આવે છે. આથી તે બીટિંગ ક્રિયાની સાથે સાથે કાપડમાં બે તાર વચ્ચેની યોગ્ય જગ્યાનું નિયમન કરવાનું કાર્ય કરે છે.
પ્રાથમિક સાળ : ભારતમાં હાથસાળ અને તેના ઉપયોગ માટેના આડકતરા પુરાવા મળે છે. ઇજિપ્તમાં આવેલ અલ-બદરિયામાં (ઈ. પૂ. 4404) મળેલ ચિનાઈ માટીના વાસણ પરના ચિત્રમાં સૌપ્રથમ સાળ, જે બે પાટડાના સ્વરૂપમાં હતી (એક તાણા વીંટેલો અને બીજો તૈયાર કાપડ વીંટેલો) તેનો નમૂનો મળી આવેલ છે. જમીન સાથે ચારે ખૂણામાં બે વાંસની મદદથી તાણાને ખેંચી રાખવામાં આવતા હતા. છૂટા સળિયા અથવા લાકડાના ટુકડા (lease rod) વડે તાણાના પડના બે ભાગ પાડીને શેડ બનાવવામાં આવતા, તથા બે દોરાને નિયમિત રીતે જુદા રાખવામાં મદદ કરતા. લીઝ રૉડનો ઉપયોગ આજ સુધી ચાલુ રહ્યો છે, તે નિર્દેશ કરે છે કે સાળના વિકાસની શરૂઆત તેના ઉપયોગ સાથે જ થઈ હતી. હાથને ઓછો શ્રમ પડે તે ર્દષ્ટિએ સાળનો વિકાસ શરૂ થયો હતો. લીઝ રૉડના ઉપયોગ પહેલાં હાથનાં આંગળાં વડે દરેક એકાંતર તારને છૂટો પાડવામાં આવતો હતો અને શેડ બનાવવામાં આવતો, જેમાંથી વાણાને પસાર કરવામાં આવતો. જો સાળનો વધુ વિકાસ બતાવવામાં આવે તો તેમાં વપરાતો ત્રીજો લીઝ રૉડ રાચના આધારરૂપ સળિયા વડે દર્શાવી શકાય. રાચને આધાર આપતા સળિયાને તાણાની ઉપર ગોઠવવામાં આવે છે. સાદા વણાટ માટે એકાંતર તારને સળિયા સાથે બાંધવામાં આવે છે. જ્યારે તેને ઊંચો ખેંચવામાં આવે ત્યારે યોગ્ય અને ઝડપથી શેડ બને છે. કેટલાકના મત મુજબ રાચ એ સાળના વિકાસમાં મહત્વની શોધ છે. સામાન્ય ઉપયોગમાં વપરાતો આ સળિયો સામી દિશામાં પણ શેડ બનાવે છે, જેથી વાણો સહેલાઈથી પાછો ફરી શકે છે.
બે આડા પાટડાના ઉપયોગવાળી સાળ સાથે ઊભા પાટડાના ઉપયોગથી બનેલી પ્રાથમિક અવસ્થાની સાળ પણ ગણાવી શકાય. તાણા ઊભા પાટડા પરથી નીચે લટકતા અને તેને સીધા તથા ખેંચાણમાં રાખવા માટે માટીના ગઠ્ઠા, ચૉકસ્ટિક કે બીજાં યોગ્ય વજન લટકાવવામાં આવતાં. આ પ્રકારની સાળનાં વજનો ઈ. પૂ. 3000ની સાલના અવશેષરૂપે મળેલ છે. પરંતુ આનો ઉદભવ તે પહેલાં થયો હશે તેમ માનવામાં આવે છે. સૌપ્રથમ ઊભા પાટડાની સાળનું ચિત્ર ઇજિપ્તના અઢારમા વંશ(ઈ. પૂ. 1567-1320)ના સમયમાં મળી આવેલું. ગાલીચા-પડદા વગેરેની ગૂંચવણભરેલી વણાટની ભાતને તે મળતું આવે છે (ઈ. પૂ. 1483 અને 1411માં). આ ગાલીચા થીબ્ઝના થુટમોસ ચોથાની કબરમાંથી મળેલ. (આજે પણ ગાલીચા તથા પડદાની બનાવટમાં ઊભી સાળની પસંદગી કરવામાં આવે છે.) ઊભી સાળમાં લટકતા તાણાને બીજા આડા પાટડા સાથે બાંધવામાં આવે છે અને આમ ઊભી તથા આડી બન્ને સાળનો સમન્વય જોવામાં આવે છે. રાચ અને શેડ બનાવતો સળિયો ઉપરના ત્રણ પ્રકારની સાળમાં વપરાય છે.
પ્રાથમિક સાળના ભાગ રૂપે ઘણી જૂની સંસ્કૃતિમાં વર્ણવેલી આ સાળ એક યા બીજી પદ્ધતિથી ઉપયોગમાં લેવાતી હતી. નવાહો ઇન્ડિયન્સ એટલે કે અમેરિકન રેડ ઇન્ડિયન વણકરો સદીઓથી ઊભી સાળનો ઉપયોગ કરીને જાડું કાપડ અને ધાબળા બનાવતા હતા. બે આડા પાટડાની સાળના ઉદાહરણ રૂપે પાછળના પટ્ટાની સાળ (back-strap loom) હતી જેમાં એક પાટડો ઝાડ અથવા બીજી કોઈ કાયમી જગ્યાએ બાંધવામાં આવતો અને બીજી પટ્ટીનો છેડો વણકર પોતાની કમર સાથે બાંધતો હતો. વણકર તાણા પર જોઈતું ખેંચાણ અને પટ્ટી પર જરૂરી દબાણ આપી કાબૂ રાખી શકતો હતો. આ બૅક-સ્ટ્રૅપ લૂમ, પહેલાંના કોલંબિયાના પેરૂમાં અને દક્ષિણ તથા મધ્ય અમેરિકાની સંસ્કૃતિમાં, એશિયામાં તથા બીજે પણ વપરાતી હતી.
ક્ષિતિજને સમાંતર આધારવાળી સાળ : પૂર્વના દેશોમાં, આશરે ઈ. પૂ. 2500ના અરસામાં વધુ વિકસેલી સાળનો ઉપયોગ થતો હતો. ચીનમાંથી શાંગ અથવા યીનના સમયમાં (અઢારમીથી બારમી સદી) રેશમી કાપડ પર સોનેરી ભાતવાળા અવશેષ મળેલા છે. આ ટ્વિલ દમાસ્કની ભાતના હતા, જે વણાટના વિશેષ જ્ઞાનના પુરાવારૂપ છે. આ નમૂના, ઉપર વર્ણવેલી સાળો પર બનાવી શકાય તેવા નથી. આ પ્રકારનું કાપડ ક્ષિતિજને સમાંતર આધારવાળી સાળ વડે બનાવવામાં આવ્યાની શક્યતા છે. બે પાટડાવાળી આડી સાળ અને ક્ષિતિજને સમાંતર આધારવાળી પગના ઉપયોગથી ચાલતી સાળની વચ્ચેના નમૂના તરીકે રાચના આધારવાળી સાળ પગના ઉપયોગથી ચાલતી હશે તેવું માની શકાય; પરંતુ આ માટે કોઈ પુરાવા ઉપલબ્ધ નથી.
પગથી ચાલતી આડી સાળના, યુરોપિયન ચિત્રશૈલીના તેરમી સદીના દસ્તાવેજ ઉપલબ્ધ છે. તે જોતાં, ત્યાં આ સાળ ઘણી વિકાસ પામેલી હોવી જોઈએ. ઘણું કરીને તે પૂર્વના દેશોમાંથી યુરોપમાં દાખલ કરવામાં આવી હશે. આ બે પાટડાની સાળને એક ચોકઠામાં પગ વડે ચલાવી શકાય તેમ ગોઠવવામાં આવતી હતી. રાચના સળિયામાં સુધારા કરીને ધરી (shaft) તરીકે ઓળખાતા પાટાને દોરડાથી સંચાલિત કરવામાં આવતો. તેના ઘણા લાભ પણ હતા. આ પ્રકારની બે પાટડાથી ચાલતી સાળમાં, બે કરતાં વધારે રાચ વાપરી શકાતી; પરંતુ તેમાં તાણાની ગોઠવણ મર્યાદિત રહેતી. તેમ છતાં ચોક્કસ વણાટ કરી, ઘણી ગૂંચવણભરી પદ્ધતિ દ્વારા થોડું કાપડ બનાવી શકાતું તથા ધરીવાળી સાળ પર 24 જેટલી ધરી સહેલાઈથી બેસાડીને, વણકર સંકુલ વણાટવાળું કાપડ બનાવવા માટે શક્તિમાન થતો. પહેલાં તો બીટિંગ માટે વપરાતી વણકરની તલવાર અથવા દાંતાવાળી વસ્તુની જગ્યાએ પટ્ટી(batten)નો વપરાશ શરૂ થયો. સાળના મુખ્ય આધાર પર અવલંબતી હોવાથી અને તેના વજન અને મુક્ત રીતે ફરી શકવાની ક્ષમતાને કારણે બીટિંગની ક્રિયા વધુ સરળ બનાવી શકાઈ. પગથી ચાલતી રચનાના ઉપયોગથી વણકરના બન્ને હાથ છૂટા રહી શકતા અને શટલ પસાર કરી શકતા તેમજ બીટિંગ માટેની પટ્ટી ચલાવી શકતા હતા. ઘણા સમય સુધી સાળ આ જ સ્થિતિમાં રહી.
ડ્રૉ લૂમ : તાણા ખેંચી શકાય તેવી આ સાળ છે. સાદા અને સરળ કાપડના વણાટ માટે ધરીવાળી સાળ યોગ્ય હતી; પરંતુ વધુ ગૂંચવણભરી ભાતનું કાપડ વણવા માટે જુદા પ્રકારની સાળની જરૂર હતી, જેમાં આશરે 100 કે વધુ ધરીની જરૂર પડે. આ પ્રકારનું વણાટ તાણા ખેંચી શકાય તેવી સાળ વડે કરી શકાય. આ પ્રકારની સાળનું ઉદભવસ્થાન મળતું નથી પરંતુ એમ માનવામાં આવે છે કે પૂર્વના દેશોમાં ક્યાંક રેશમના વણાટમાં તેનો ઉપયોગ થતો અને મધ્ય યુગમાં ઇટાલીનાં રેશમ ઉત્પન્ન કરતાં કેન્દ્રોમાં તેને દાખલ કરવામાં આવેલી. ડ્રૉ લૂમમાં બે રીતે શેડ બનાવી શકાતો; પગથી ચાલતી ધરી વડે જે વણકર ચલાવી શકતો, તે ઉપરાંત જે પ્રકારની ભાત પાડવાની હોય તે પ્રમાણે તાણાને વિભાજિત કરી, દોરડા વડે ઊંચકીને. આ કાર્ય સાળના ઉપરના ભાગમાં બેસાડવામાં આવતા કારીગર(draw boy)ની મદદથી થતું.
સત્તરમી સદીની શરૂઆતમાં ઇટાલી અને ફ્રાંસમાં, ખેંચી શકાય તેવી સાળમાં સુધારો કરીને યાંત્રિક ડ્રૉ બૉયનો ઉપયોગ શરૂ કરવામાં આવ્યો. ડ્રૉ બૉયને સાળની બાજુમાં જમીન પર ઊભો રાખીને દોરડાથી સારી રીતે સંચાલન કરી શકાતું. આ ડ્રૉ બૉયની મદદ તથા તેનાથી થતી ભૂલોને કારણે ઉદભવતી ખામીઓ દૂર કરવા માટે સ્વયંસંચાલિત યાંત્રિક ખેંચાણ માટેની શોધખોળ કરવાનું કાર્ય ચાલુ રહ્યું. સ્વયંસંચાલિત યાંત્રિક રીતે શેડ બનાવવાની ક્રિયાની મોટાભાગની શોધ ફ્રાંસમાં થઈ છે. આ દેશ રેશમકામમાં આકૃતિઓવાળી ભાત ઉપજાવવામાં આગળ પડતો હતો.
1725માં બેસિલ બાઉશોને ભાત (pattern) બનાવવા માટે જરૂરિયાત મુજબ દોરડાં ખેંચી શકાય તેવી તાણા ખેંચવાની યાંત્રિક રીતમાં ઉમેરો કર્યો. નળાકારની ફરતે વીંટેલા, ભાતને લગતાં કાણાં પાડેલા કાગળના ટુકડાના ઉપયોગથી પસંદગીને નિયંત્રિત કરવામાં આવતી હતી. નળાકારને પસંદગી માટેની પેટી તરફ ખસેડવામાં આવતો, જેમાં તાણાનું નિયમન કરતાં દોરડાં સાથે સોયા રાખવામાં આવતા. એ સોયા કાગળના ભાગને અડતા ને આગળ ધકેલાતા અને બાકીના કાણામાંથી પસાર થતા અને ત્યાં જ રહેતા. આમ પસંદ કરેલાં દોરડાં, પગથી ચાલતા ભાગ વડે નીચે ખેંચવામાં આવતાં હતાં.
તાણા ખેંચવા માટે વપરાતી યાંત્રિક રચનાથી તાણાની યોગ્ય પસંદગી થઈ શકતી, છતાં પણ ચાલકની જરૂર પડતી હતી. 1728માં સોયાની સંખ્યા વધારીને દરેક જુદા શેડ બનાવવાની ક્રિયા માટે સળંગ પટ્ટીરૂપ લંબચોરસ કાણાં પાડેલ જાડા કાગળનો ઉપયોગ કરી વધુ સુધારો કરવામાં આવ્યો. 1745માં ઝાક દ વોકાસોંએ ઘણા સુધારાવાળી સાળ બનાવી. નિયમન કરતી પેટીને તેણે સાળના ઉપરના ભાગે ગોઠવી હતી. પેટીમાં તાણાના સીધા સંચાલન માટે વપરાતાં દોરડાં, આંકડા સાથે બાંધેલાં હતાં. આ આંકડા સોયમાંથી પસાર થતા અને ધાતુની પટ્ટી વડે ઊંચકાયેલા રહેતા, જે નળાકાર પર ચોંટાડેલા કાગળ વડે પસંદગી પામતા હતા. અહીં બીજા કોઈ મદદનીશની જરૂર રહેતી નથી. નળાકાર રચના ઘણી ગૂંચવણભરેલી છે તથા તેની કોઈ યાંત્રિક રચનાની માહિતી નથી. પરંતુ તે જૅકાર્ડ રચનાના પાયાના સિદ્ધાંત તરીકે ઉપયોગી નીવડી છે.
જૅકાર્ડ રચના : કોઈ પણ પ્રકારની દોરવણી વગર, સ્વપ્રયત્નથી, ફ્રાંસના વતની જૉસેફ-મારી જૅકાર્દે આ રચના વોકાસોં સાળની સંભાળ લેતી વખતે શોધી હતી. તેમણે 1801માં પૅરિસમાં ઔદ્યોગિક પ્રદર્શનમાં સુધારેલી ડ્રૉ લૂમ મૂકી અને અત્યારે જૅકાર્ડ રચના તરીકે ઓળખાતી સાળ પરની રચના જોવા મળે છે તેની 1805માં શોધ કરી; તેમના નામ પરથી તે જૅકાર્ડ રચના તરીકે જાણીતી છે. આ રચનાથી બનતું કાપડ જૅકાર્ડ વણાટ તરીકે ઓળખાય છે.
જૅકાર્ડ રચના સાળના ઉપરના ભાગે ગોઠવવામાં આવે છે અને તેનું સંચાલન વણકર પગ પડે કરી શકે છે. આ રચનાના ઉપયોગથી પસંદગી પ્રમાણે શેડની રચના કરી શકાય છે. ડ્રૉ લૂમમાં તાણા પસાર કરેલી ગાળા(loop)વાળી દોરી હોય છે જેનું સંચાલન બીજા છેડે લટકાવેલું વજન ખેંચીને કરી શકાય છે. તે જ રીતે જૅકાર્ડ રચનામાં સ્પ્રિંગથી ઉપરનીચે થઈ શકે તેવા હૂકની રચના હોય છે, જેમાંથી તાણા પસાર કરવામાં આવે છે. આ હૂકની સાથે સોયા જોડાયેલા હોય છે. વણાટમાં જે પ્રકારની ભાત ઉપજાવવાની હોય તે પ્રમાણે પટ્ટીમાં કાણાં પાડવામાં આવે છે. ક્ષિતિજ સમાંતર ગોઠવેલા સળિયાથી તેનું સંચાલન કરવામાં આવે છે. નળાકારમાં જ્યારે કાણાં પાડેલી પટ્ટી પસાર થાય છે ત્યારે હૂક સાથે જોડાયેલી સોયો જે કાણામાંથી પસાર થાય છે તે તાણા ઊંચકાય છે, જ્યારે બાકીની સોયો પાછી ધકેલાતાં, તાણા તેના મૂળ સ્થાનમાં જ રહે છે. આ પ્રમાણે પસંદગી અનુસાર શેડની રચના કરી શકાય છે. વાણો (શટલ) પસાર કરવાની સ્થિતિ પ્રમાણે અલગ પટ્ટીની રચના કરવામાં આવે છે. આ પ્રકારના વણાટમાં મર્યાદિત દોરાનું સંચાલન શક્ય હોઈ, આવર્તિત ભાતવાળી રચના સાળ ઉપર જ ગોઠવવામાં આવે છે. જૅકાર્ડ રચનાના ઉપયોગથી વણકર ગૂંચવણભરી કારીગરીવાળું કાપડ બનાવી શકે છે. મોટાં ચિત્રોની ભાત પણ આ રીતે ઉપસાવી શકાય છે.
ફ્લાઇંગ શટલ : જ્હૉન કે નામના અંગ્રેજ સંશોધકે ફ્લાઇંગ શટલ માટે 1733માં મેળવેલ પેટન્ટ એ સ્વયંસંચાલિત સાળની બનાવટ માટે પ્રથમ પગથિયું હતું. જ્હૉન કે પહોળી સાળનો કારીગર હતો. કારણ કે આ સાળમાં બે કારીગર સાળની બાજુમાં બેસતા અને તેમાંનો એક, એક છેડાથી મધ્યમાં અને બીજો મધ્યમાંથી બીજા છેડે અને ફરી મધ્યમાં શટલને ફેંકતો હતો. આમ શટલની ફેરબદલી તાણાની વચ્ચે અટકાવ સાથે થતી હોવાથી કાપડમાં ખામી આવતી. કેએ શટલને દોરી બાંધી તાણામાંથી પસાર કરવાની રચના કરી જેથી શટલ શેડમાં એકથી બીજા છેડે અને બીજા છેડેથી મૂળ સ્થાને સહેલાઈથી પસાર કરી શકાતું. આમ ફ્લાઇંગ શટલની રચના વડે વણકર કોઈ પણ પનાનું કાપડ, પહેલાં જે બે વણકર વણી શકતા તેના કરતાં વધુ ઝડપથી વણી શકતો. કેની શોધનો મુખ્ય લાભ એ હતો કે ફ્લાઇંગ શટલને સ્વયંસંચાલિત સાળ માટે તુરત જ ઉપયોગમાં લઈ શકાયું.
શક્તિસંચાલિત સાળ (power driven loom) : અંગ્રેજ પાદરી એડમંડ કાર્ટરાઇટે 1785માં કાપડના વણાટ માટેનો સર્વપ્રથમ શક્તિસંચાલિત સાળ માટે પેટન્ટ મેળવ્યો હતો. તેમાં શેડ બનાવવાની, વાણો નાખવાની અને તૈયાર કાપડ વીંટવાની પદ્ધતિઓને જ ગણતરીમાં લીધી હતી. કાર્ટરાઇટની 1786ની બીજી સાળ ઘણી જ આશાસ્પદ હતી. તેમાંની વણાટયંત્ર માટેની કલ્પનાઓ શક્તિસંચાલિત સાળના વિકાસ માટે પાયારૂપ ગણી શકાય તેવી હતી.
તાણાને કાંજી ચડાવવાની પદ્ધતિ : આ માટે સાળને વારંવાર થોભાવવી પડતી હતી. આ રીત શક્તિસંચાલિત સાળના વિકાસમાં વિઘ્નરૂપ હતી. આ માટે એક કારીગરને કાંજીની પ્રક્રિયા કરવા માટે રોકવો પડતો; તેથી સમય અને કિંમતમાં કોઈ ફેર પડતો નહિ. ઓગણીસમી સદીની શરૂઆતમાં કાંજીની પ્રક્રિયા માટે યંત્રની શોધ થઈ; જેમાં તૈયાર તાણાને વૉર્પર બીમ પર અને કાંજી કરેલા તાણાને વણવા માટેના વીવર બીમ પર લપેટવામાં આવતા હતા. થોડા સમય બાદ સુધારેલા કાંજીયંત્ર(sizing machine)ની શોધ થઈ જેને કારણે શક્તિસંચાલિત સાળ ઉપયોગી બની.
સ્કૉટલૅન્ડના વિલિયમ હૉરક્સે 1803થી 1813ના ગાળામાં તૈયાર કાપડ વીંટવાની રચના (cloth beam) વિકસાવી અને લાકડાની હાથસાળ કરતાં વધુ મજબૂત ને ઓછી જગ્યા રોકે તેવી સાળ લોખંડમાંથી બનાવી.
બૉસ્ટનના ફ્રાંસિસ કેબોટ લોવેલે કાંજીયંત્રમાં વધુ અખતરા કર્યા અને શક્તિસંચાલિત સાળમાં વધારે ઝડપથી કાપડ વણી શકાય તેવા સુધારા કર્યા.
તાણાને ઢીલો કરવાની અને તૈયાર કાપડ વીંટવાની સંયોજિત ક્રિયા વડે તાણાનું ખેંચાણ વણાટ દરમિયાન જળવાઈ રહે તેવા સુધારા પણ થયા. બીટિંગ વખતે કાપડ ઢીલું ન પડે અને શટલ તેની જગ્યાએ પાછું ગોઠવાય ત્યાં સુધીની ક્રિયાનો પ્રયોગ સૌપ્રથમ ઇરેસ્ટસ બ્રિગહામ બિગલોએ જાજમના વણાટ માટેની સાળમાં કર્યો. આ પ્રયોગનો લાભ બધા જ પ્રકારના વણાટમાં લેવામાં આવ્યો. શક્તિસંચાલિત સાળને આંચકા વગર ઘર્ષણથી ઊભી રાખવાની ક્રિયા એ બિગલોની બીજી ઉપયોગી શોધ હતી. તે પ્રથમ જાજમના વણાટના ઉપયોગમાં લેવામાં આવી હતી.
આ શોધો પ્રાથમિક ધોરણે સાદા કાપડના વણાટ માટેની શક્તિસંચાલિત સાળ સંબંધી છે. મૅસેચૂસેટ્સમાં સુતરાઉ કાપડના કારખાનાની મશીનશૉપમાં યંત્રવિદ (machinist) તરીકે કામ કરતા અંગ્રેજ કારીગર વિલિયમ ક્રૉમ્પ્ટને સાળ-સુધારણાનું કાર્ય કર્યું. તેનો પેટન્ટ 1837માં અમેરિકા અને ઇંગ્લૅન્ડમાં મેળવવામાં આવ્યો. પાછળથી તેમના દીકરા જ્યૉર્જ ક્રૉમ્પ્ટને તેમાં વધારે સુધારા કર્યા. આમ ઓગણીસમી સદીના સાળ-સુધારણાના પ્રયાસોએ જુદી જુદી જાત અને ભાત તથા ઓછી ઉત્પાદન-કિંમતવાળા કાપડનું જથ્થાબંધ ઉત્પાદન શક્ય બનાવ્યું.
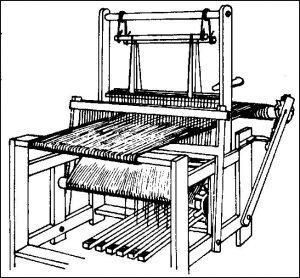
આકૃતિ 5 : સાળ
આધુનિક સાળ (modern looms) : આધુનિક સાળ પણ શેડ બનાવવાની (shadding), વાણા પસાર કરવાની અને કાપડ આગળ ખસેડવાની ક્રિયાઓના પુનરાવર્તિત ક્રમ પ્રમાણે કામ કરે છે. આ પ્રાથમિક માળખાના આધારે જ વીસમી સદીમાં ઘણો વિકાસ સધાઈ રહ્યો છે. જૂની સાળમાં સુધારો કરીને વધુ ઉત્પાદનક્ષમતાવાળી નવી જાતની સાળ ઔદ્યોગિક વિકાસ માટે તૈયાર કરવામાં આવે છે. આ માટે મુખ્ય બે કારણ છે : (1) મજૂરીનો ઊંચો અને સતત વધતો જતો દર, (2) લાંબા માનવસર્જિત રેસા. મજૂરીના ઊંચા દરના કારણે ઉત્તમ ગુણવત્તાવાળાં, સ્વયંસંચાલિત, વધુ ઉત્પાદનક્ષમતાવાળાં યંત્ર અને સાળ અસ્તિત્વમાં આવ્યાં છે. લાંબા માનવસર્જિત રેસાથી ઊંચી ગુણવત્તાવાળું કાપડ બનાવી શકાય છે.
આધુનિક સાળને બે ભાગમાં વહેંચી શકાય : (1) સાદા કાપડના વણાટ માટેની સાળ, (2) નળાકાર કાપડના વણાટ માટેની સાળ (circular or tubular fabric loom).
મોટાભાગની સાળ સાદા કાપડના વણાટ માટે વપરાય છે. આથી બીજા પ્રકારની સાળનો નિર્દેશ કરવાનો હોય ત્યારે તેનો ત્યાં ઉલ્લેખ કરવામાં આવે છે. સપાટ સાળ બે ભાગમાં વહેંચી શકાય. જેમાં શટલ વપરાય છે તેને શટલવાળી સાળ અને શટલ વપરાતું નથી પરંતુ સ્થિર જથ્થામાંથી વાણો ખેંચવામાં આવે છે તેને શટલ વગરની સાળ તરીકે ઓળખવામાં આવે છે. શટલવાળી સાળના પણ બે પ્રકાર છે : એકમાં શટલ હાથથી પસાર કરવામાં આવે છે, જ્યારે બીજામાં શટલ સ્વયંસંચાલિત રીતે કાર્ય કરે છે. બંને આધુનિક અને શક્તિસંચાલિત સાળ છે. બંનેમાં વણાટકાર્ય સ્વયંસંચાલિત હોય છે તથા બંને એક જ પ્રકારે કાર્ય કરે છે.
જ્યાં દોરા, કાપડ અથવા સ્વયંસંચાલિત સાળની યંત્રવિદ્યાની પૂરતી જાણકારી ન હોય તેમજ તે આર્થિક રીતે પોસાય તેમ ન હોય ત્યાં હાથસાળ ખાસ સંજોગોમાં વપરાય છે. આ સાળ ઓગણીસમી સદીના ઉત્તરાર્ધની શક્તિસંચાલિત સાળ કરતાં પ્રાથમિક રીતે જુદી પડે છે, તે ઓછી ઉત્પાદનક્ષમતા ધરાવે છે પરંતુ યાંત્રિક રીતે ઉત્તમ છે; દા.ત., દાંતાવાળા ચક્ર(cast gear-wheel)ની જગ્યાએ કાપાવાળી (machine cut) યાંત્રિક રચના અને મજબૂત હડલો વાપરવામાં આવે છે. શટલની જગ્યા બદલવા માટે ઉપરથી પસાર કરવાની રીતે(overpick)ને બદલે સુઘડ અને સલામત એવી નીચેથી પસાર કરવાની રીત(underpick)નો ઉપયોગ કરવામાં આવે છે.
આધુનિક સાળના મુખ્ય પ્રકાર તરીકે જુદા જુદા પના (width) માટે વપરાતી સ્વયંસંચાલિત સાળ છે. આ પ્રકારની સાળમાં દોરો ભરેલું બૉબિન, ખાલી બૉબિનની જગ્યાએ મૂકવામાં આવે છે. આધુનિક સાળ એ ઓગણીસમી સદીના અંતભાગમાં બનેલી સ્વયંસંચાલિત સાળ જેવી જ છે. આ સમયના ગાળામાં આપોઆપ શટલ બદલાય તેવી રચનાવાળી સાળ બનાવવામાં આવી હતી. પરંતુ કોઈ પણ દોરા/વાણા બદલવા માટે શટલ બદલવું જરૂરી છે તેવું માનતા હોવાથી તે બિનઉપયોગી પુરવાર થઈ હતી.
સામાન્ય યાંત્રિકીકરણના સુધારા સિવાય સ્વયંસંચાલિત સાળમાં વાણો પસાર કરવાની રીતમાં જ વિકાસ થયો છે. હાથ વડે ભરાતા બૉબિનની જગ્યાએ સ્વયંસંચાલિત બૉબિન વીંટાળવાના મશીન પર ભરેલું બૉબિન સાળ પર સંચાલિત બૉબિનપૂરક રચના વડે પૂરવામાં આવે છે. દોરાનાં મોટાં બંડલ બૉબિન ભરવા માટે યંત્ર પર મોકલવામાં આવે છે. આમ આ બૉબિન ભરવા માટેની રચનાઓ અમુક પ્રકારના દોરાઓ માટે જ આર્થિક રીતે શક્ય બને છે. જ્યારે એક કરતાં વધારે રંગના વાણા વાપરવાના હોય છે ત્યારે પૂરક રચના તરીકે રોટરીબૅટરીની રચના વપરાય છે, જેમાં ઊભી હારમાં બૉબિન ગોઠવવામાં આવે છે.
આમ ત્રણેય રીતમાં શટલ ભરવાની રીત સરખી જ છે. જ્યારે શટલ તેના ઘર(box)માં સ્થિત હોય છે અને ફણી(reed)ને આધાર આપતો પાટડો (bar) વધુમાં વધુ આગળના ભાગમાં આવે છે ત્યારે પૂરક (filler) શટલમાં આવે છે અને તપાસે છે કે વાણો ખાલી (exhaust) થવાની તૈયારીમાં છે કે નહિ. પૂરક યાંત્રિક અથવા વીજળીક રચના હોઈ શકે છે, જેમાં વાણાની ગેરહાજરીમાં યાંત્રિક ઘસારા અથવા વીજળીક અવરોધના બદલાવાના આધારે વાણાની ગેરહાજરી જોવામાં આવે છે. આના બદલામાં પ્રકાશ પર આધારિત પૂરક રચના (optical filler) પણ વાપરવામાં આવે છે જે ખાલી કોકડીથી પરાવર્તિત પ્રકાશના જથ્થા પર આધાર રાખે છે.
પૂરક રચના સંકેત આપે છે કે બૉબિન ખાલી થવાની તૈયારીમાં છે ત્યારે યાંત્રિક કે વીજળીક સંકેતો બૉબિન બદલવાની રચનાને કાર્યરત બનાવે છે. શટલ યોગ્ય રીતે તેના ઘરમાં ગોઠવાયેલી સ્થિતિમાં હોય છે અને ક્ષણ માટે તાણા અને વાણાની ગતિ સ્થિર બને છે. આ વખતે બૉબિન શટલમાં દાખલ કરાય છે અને તે જ સમયે ખાલી બૉબિન શટલની ખુલ્લી બાજુથી બહાર ધકેલાય છે. આ દરમિયાન સાળ તેની સામાન્ય ઝડપથી ચાલુ જ રહે છે.
આ પ્રક્રિયા દરમિયાન કાપડની ધારી પાસે બિનજરૂરી વાણો બહાર રહે છે. આને જો યોગ્ય રીતે નિયંત્રિત કરવામાં ન આવે અથવા દૂર કરવામાં ન આવે તો કાપડમાં નુકસાન થવાનો સંભવ રહે છે (જૂના બૉબિનના વાણાના અવશેષ દૂર થવાની ખાતરી રૂપે બૉબિન શટલમાંથી બહાર નીકળે તે પહેલાં શટલની આંખ પાસે છરી (cutter) પહોંચીને વાણાને કાપે છે). જૂની યાંત્રિક રચનાને બદલે હવાના દબાણશોષક-(pneumatic suction)ની રચના આધુનિક સાળમાં ઉપયોગમાં લેવામાં આવે છે. તેને કારણે નાજુક બંધારણવાળું કાપડ સ્વયંસંચાલિત સાળ પર ગુણવત્તાને નુકસાન પહોંચાડ્યા સિવાય વણી શકાય છે.
ઝડપી સાળમાં ઉત્પાદનક્ષમતા વધારવા માટે ઘણી વાર મોટાં અને ભારે શટલ વપરાય છે, જે પહેલાંના કરતાં ઘણો જ વધારે અવાજ કરે છે. સામાન્ય કાપડના કારખાનામાં થતો અવાજ ઘણો વધારે હોય છે. તેને કારણે લાંબા વખતે કારીગરોની શ્રવણશક્તિને નુકસાન થાય છે. આ ખામી આધુનિક શટલ વગરની સાળમાં દૂર કરવામાં આવી છે.
શટલ વગરની સાળ ત્રણ પ્રકારની હોય છે : (1) શટલની રચના જેવી જ રચનાવાળું સાધન (dummy shuttle), (2) રેપિયર (ખંજર જેવી રચના) અને (3) પ્રવાહીની ધાર જેવી રચના.
ડમી શટલ : શટલ વગરની સાળ તરીકેની સફળ સાળ છે. એમાં શટલની રચના જેવી રચનાવાળું સાધન વપરાય છે અને શેડમાંથી પસાર થતાં પાછળ વાણો મૂકતું જાય છે.
રેપિયર : શેડમાં એક અથવા બે રેપિયર પસાર થાય છે અને સ્થિત જથ્થામાંથી વાણો પુરાતો જાય છે. આ પટ્ટી જ્યારે શેડમાં હોય ત્યારે સીધી હોય છે અને ઘર(shuttle box)માં આવે ત્યારે ચક્ર પર વીંટાઈ જાય છે, જેથી જગ્યાનો બચાવ થાય છે. રેપિયર એ મજબૂત સળિયો અથવા તો વળી શકે તેવા સ્ટીલની પટ્ટીનું બનેલું હોય છે. રેપિયર સાળ લગભગ બધી જ રીતે ડમી શટલ લૂમ કરતાં સરળ હોઈ વધુ ઉપયોગી છે; પરંતુ તે વાણો પસાર કરવાની વધારે ઝડપ માટે યોગ્ય નથી. વધુમાં વધુ એક મિનિટમાં 365 મી. પસાર કરી શકે છે. વણાટની ઝડપ કેટલા રેપિયર વાપરવામાં આવે છે તેના પર તથા કાપડની કિનારી (selvedge) કેવી છે તેના પર આધારિત છે.
પ્રવાહીની ધાર જેવી રચના (fluid jet loom) : ફ્લ્યુઇડ જેટ લૂમ બે પ્રકારની હોય છે : (1) ઍર જેટ અને (2) વૉટર જેટ. ઍર જેટ અથવા વૉટર જેટ વડે વાણાને શેડમાંથી જોઈતી લંબાઈ પ્રમાણે પસાર કરવામાં અથવા ધકેલવામાં આવે છે. આ પ્રકારની સાળની સૌથી મહત્વની બાબત એ છે કે શેડમાંથી વાણા સિવાય કોઈ પણ ઘન વસ્તુ પસાર કરવામાં આવતી નથી. સામાન્ય રીતે વાણાને તપાસવાની તથા સુરક્ષિત રાખવાની બધી જ તકલીફો દૂર કરે છે અને અવાજનું પ્રમાણ ઘટાડી શકાય છે.
આ ઉપરાંત ઔદ્યોગિક રીતે વિકાસ પામેલ સાળ પણ હાલમાં પ્રાયોગિક ધોરણે અમલમાં છે. સાળનો વિકાસ હંમેશાં ધીમો રહ્યો છે. કેટલીક સાળ જે હાલમાં મહત્વ ધરાવે છે તે આજથી લગભગ 50 અથવા 100 વર્ષ પહેલાં શોધાઈ હતી. સૌથી મહત્વની સંશોધન-પ્રવૃત્તિ શટલ વગરની સાળની પદ્ધતિની દિશામાં નોંધાઈ છે, કારણ કે ઊંચી ગુણવત્તા અને ઉત્પાદનક્ષમતા વધારવાનું આથી શક્ય બને. વળી વાણો દાખલ કરવાની ઝડપી પદ્ધતિ અને અવાજ, ભયજનક ધ્રુજારી (danger vibration), વધુ વીજળિક શક્તિનો ઉપયોગ, વાપરવામાં આવતાં શટલના ઘસારા ઉપર ધ્યાન આપવાનું વગેરે ગેરલાભો પણ દૂર કરી શકાયા.
પ્રાયોગિક ધોરણે સીધા પ્રક્ષેપની પદ્ધતિથી વાણો લંબ રૂપે ઝડપથી પસાર કરવામાં આવે છે, જે પોતાની ગતિ વડે જ તાણાની આરપાર પસાર થાય છે. ત્યારે શેડમાં વાણા સિવાય બીજું કંઈ જ દાખલ કરવામાં આવતું નથી. આને સુસ્ત (inertial) પદ્ધતિ તરીકે ઓળખવામાં આવે છે. બીજી પ્રાયોગિક ધોરણે વિકાસ પામતી સાળમાં એક કરતાં વધારે રેપિયર વાણા માટે પસાર કરવામાં આવે છે. વધારામાં હેડલ અને ફણીને દૂર કરવાની દિશામાં સંશોધનપ્રવૃત્તિ અપનાવવામાં આવી છે.
પાયાનો વણાટ (basic weave) : પ્રાથમિક વણાટમાં સાદો વણાટ (plain or tabby weave) ટ્વિલ અને સાટીનને ગણાવી શકાય.
સાદો વણાટ (plane weave) : સાદો વણાટ અથવા ટૅબી વણાટ એ સાદામાં સાદો અને બધા વણાટમાં સામાન્ય વણાટનો પ્રકાર છે. અહીંયાં તાણા અને વાણાના માત્ર બે તારને જોડવાથી વણાટનો એકમ બને છે. આ પ્રકારના વણાટ માટે તાણાને ખેંચાણ આપીને સમાંતર ગોઠવવામાં આવે છે અને તાણાના પટ્ટાને લંબ રૂપે વાણો એક
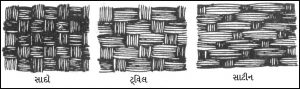
આકૃતિ 6 : વણાટના વિવિધ પ્રકાર
છેડેથી બીજા છેડે વારાફરતી ઉપરનીચે તાણામાંથી પસાર કરવામાં આવે છે. (દા.ત., ખાટલામાં ભરવામાં આવતી પાટી.) વાણાને વિરુદ્ધ દિશામાં તાણાઓમાંથી વારાફરતી પસાર કરતાં વણાટ એકમ પૂરો થાય છે અને પહેલાંનો વાણો તેની જગ્યાએ ગોઠવાય છે. દરેક વાણાના દાખલ થવા સાથે કાપડની લંબાઈ વધતી જાય છે. જ્યારે તાણા અને વાણા લગભગ કદ અને જથ્થામાં સરખા બને ત્યારે તૈયાર કાપડ સમતોલ થાય છે અને તાણા તથા વાણાની સંખ્યા સરખી હોય તેવા પ્રકારના બીજા કોઈ પણ પ્રાથમિક વણાટના કાપડની રચના કરતાં મજબૂત હોય છે. સાદા વણાટ અથવા ટૅબી વણાટમાં જ્યારે જુદા જુદા કદના તાણા અને વાણા વપરાય છે ત્યારે તેમાંથી ટાફેટા અને પોપલિન પ્રકારનું કાપડ બને છે, જેમાં આડી સળ (ribs) અથવા દોરીની અસર ઉપજાવવા માટે પાતળા તાણાને પ્રમાણમાં થોડા જાડા વાણા વડે વણવામાં આવે છે. સાદા વણાટમાં ટૅબીની પદ્ધતિને વધુ સરળ બનાવતાં બે કે તેથી વધારે તાણા અથવા વાણા અથવા બંનેને એકમ તરીકે પસાર કરવામાં આવે છે ત્યારે જે રચના બને છે તે ટોપલી જેવા વણાટના કાપડની અસર ઉપજાવે છે.
ટૅપેસ્ટ્રી : એ સાદા વણાટનો જ પ્રકાર છે. તેમાં જુદા જુદા રંગના વાણાને તાણામાંથી પસાર કરીને ભાત (pattern) બનાવવામાં આવે છે, જે સામાન્ય રીતે અસંતુલિત વણાટ છે. અહીં વાણો પ્રમાણમાં ઓછા તાણાઓને ઢાંકે છે. આ પ્રકારનું કાપડ મજબૂત અને ઘટ્ટ (ટકાઉ) હોય છે. તેઓ સપાટ અને સામાન્ય રીતે ઉઠાવ (drape) વગરના હોય છે. તેનો ઉપયોગ ઉત્સવમાં તથા શણગારવા માટે વપરાતા કાપડમાં સદીઓથી થાય છે.
ટ્વિલ વણાટ (twill wave) : ટ્વિલ વણાટ એ વણાટમાં પડતી ત્રાંસી (diagonal) લાઇનોની રચનાથી બનતો પ્રકાર છે. સાદા ટ્વિલનું વણાટ બે તાણાની ઉપરથી અને ત્યારબાદના તાણાની નીચેથી વાણો પસાર કરતાં બને છે. આ જ એકમને દરેક પિક વખતે જમણી કે ડાબી બાજુ આવર્તિત કરીને વણાટ કરવામાં આવે છે. ટ્વિલ કે જેમાં તાણા વધારે અને વાણાની ઉપરથી પસાર થતા હોય તેને તાણાની ઉપલી સપાટીની બાજુ જ્યારે વાણા વધારે અને તાણાની ઉપરથી પસાર થતા હોય તેને વાણાની મુખપૃષ્ઠની બાજુ કહેવામાં આવે છે. ટ્વિલનો ખૂણો પણ બદલી શકાય છે.
ટ્વિલના એક એકમમાં તાણા અને વાણાની સંબંધિત સંખ્યા બદલાતાં તેના પ્રકાર બદલી શકાય છે. (જેમ કે, 2 : 1, 2 : 3, 3 : 1, 6 : 2 વગેરે.) એકમના વિકર્ણ ત્રાંસી લાઇનો નિયમબદ્ધ રીતે મધ્યાન્તરે તોડી, વિકર્ણની દિશા ઉલટાવી વળાંક ‘V’ આકાર(V, L – chevrons or lozenges)ની રચના અથવા ઘણી ટ્વિલની રચના ભેગી કરીને અથવા સુધારા કરીને નવી રચના અને પ્રકાર બનાવી શકાય છે.
ટ્વિલનો ઉઠાવ એ જ કાઉન્ટના સાદા વણાટવાળા કાપડ કરતાં સારો આવે છે, કારણ કે ટ્વિલમાં ઓછું વણાટકામ હોય છે. ઘણા વજનદાર પોત(texture)ના કાપડમાં વર્ષોથી ટ્વિલનું વણાટ થતું આવ્યું છે. ઉદાહરણ રૂપે મધ્ય યુગનું ઊની કાપડ (wool serges), હીરાની ભાતના વણાટવાળું, મેજ તથા પથારીના પાથરણા માટેનું કાપડ તથા ભારતીય શાલને ગણાવી શકાય.
સાટીન વણાટ (satin weave) : સાટીન વણાટ દેખીતી રીતે ટ્વિલના વણાટને મળતો આવે છે. ટ્વિલ વણાટનો ગુણધર્મ છે કે તેમાં ક્રમમાં આવતા વાણાની નિયમિતતા જળવાઈ રહે છે, જ્યારે સાટીનમાં તેમ થતું નથી. આથી સ્પષ્ટ ત્રાંસી રેખાઓ જોવા મળતી નથી. પરંતુ લાંબા ઉપર દેખાતા તાણાવાળી સુંવાળી સપાટીવાળા કાપડની રચના જોવા મળે છે. યોગ્ય સાટીનના વણાટમાં પાંચ તાણા અને વાણાના આવર્તિત એકમ હોય છે. આથી ઓછામાં ઓછા પાંચ આવર્તિત ગાળા જરૂરી છે. સાટીન કાપડ સુંવાળું, તૂટ્યા વગરનું, ઓછા વળવાળું, દેખીતી રીતે આડા વણાયેલા દોરાઓથી બનેલું હોય છે. તે પ્રકાશના પરાવર્તનને કારણે ચળકાટવાળું લાગે છે. ઓછો વણાટ, વણકરને પ્રમાણમાં વધારે તાણા વાપરવાની છૂટ આપે છે, જેથી ઘટ્ટ અથવા ભારે પોતવાળું કાપડ બને છે. તેમાં સુંવાળાપણું તથા ઝાંયવાળાં પડ (shadowed folds) બનાવી શકાય છે. સાટીન વણાટમાં લાંબાં આવર્તન (floats) હોય છે તે પહેરવામાં નાજુક (susceptible) છે તેથી તેની ગણના ઊંચી જાતના કાપડ (luxurious fabric) તરીકે થાય છે.
સાટીન વણાટ એ દમાસ્ક અને વાણાની બાજુવાળું સાટીન એમ બે પ્રકારે ઉપલબ્ધ છે. દમાસ્ક એ ઘણો અગત્યનો પાયાના સાટીનના વણાટનો ફેરફાર છે. ઉત્તમ દમાસ્કમાં ઘટ્ટ રંગીન આકૃતિઓની ભાતને તાણાની દિશામાં સાટીન વણાટ અને સંલગ્ન ભાગને વાણાની દિશાના સાટીન વણાટથી ઉપસાવી કાપડ બનાવવામાં આવે છે. આ રીતે તાણા અને વાણા વડે થતા પ્રકાશના પરાવર્તનમાં ફેરફાર કરીને ભાત ઉપસાવવામાં આવે છે. રેશમના વણાટમાં દમાસ્ક પ્રકારના વણાટની પદ્ધતિ ચીનમાંથી શરૂ થઈ હતી. ઇટાલી 13મીથી 17મી સદી સુધી યુરોપના રેશમ-ઉત્પાદનનું કેન્દ્ર હતું. ત્યારે દમાસ્ક વણાટપદ્ધતિ ઇટાલીમાં થઈ યુરોપમાં પ્રસરેલી. આ સમય દરમિયાન ખેંચી શકાય તેવી સાળ(draw loom)ના નેધરલૅન્ડ અને બેલ્જિયમના કારીગરોએ પણ લિનન દમાસ્કનું વણાટ કરી આ કળા વિકસાવી હતી. તે વખતના રેશમના દમાસ્ક વણાટમાં બાઇબલના પ્રસંગો, સમકાલીન બનાવો અથવા રાજા-ઉમરાવોનાં હથિયારો મોટી આકૃતિઓના રૂપે વણીને કાપડના નમૂના બનાવવામાં આવતા હતા.
સંકુલ વણાટ અથવા મિશ્રિત વણાટ (complex weave) : બહુસ્તરીય (multiple), રૂંવાંવાળું (pile), જૅકાર્ડ, ડૉબી અને લીનો વગેરે આ પ્રકારના વણાટ ગણાય છે.
બહુસ્તરીય સાદો વણાટ (multiple plain weave) : બંને બાજુ વાપરી શકાય તેવું દ્વિસ્તરીય કાપડ આ રીતે બનાવી શકાય છે, જે બે સ્તરમાં વણાયેલું હોય છે. આ બંને સ્તર તદ્દન જુદા અથવા બંને કાપડની કિનારીથી કાપડમાંની ભાતની કિનારીઓની સાથે અથવા તો જુદા બાંધેલા વાણા વડે જોડાયેલા હોઈ શકે છે. સામાન્ય રીતે બંને સ્તરના વણાટ માટે પાયાની પદ્ધતિઓનો ઉપયોગ કરવામાં આવે છે અને કાપડ કયા હેતુ માટે ઉપયોગમાં લેવાનું છે તેના પર સ્તરનો વણાટ આધારિત હોય છે.
દ્વિસ્તરીય કાપડ(double woven)નો પહેરવેશમાં ઉપયોગ થાય છે; પરંતુ તે હૂંફાળું (warm), વજનમાં ભારે અને ઓછું ઓપ આપનાર છે, જે ઘણે ભાગે પથારીના પાથરણા તરીકે અથવા દીવાલ સુશોભનમાં વાપરવામાં આવે છે. 18મી સદીના જર્મનીમાં દ્વિસ્તરીય વણાટના પ્રાચીન નમૂના રૂપે બેઇડવાન મળેલ, જે દ્વિસ્તરીય સાદા વણાટથી બનાવેલી પરંતુ તે ભાતની કિનારી વડે જોડાયેલું હતું. તેમાં ઘાટા રંગની એક સ્તરની ભાત અને બીજા સ્તરમાં આછા રંગની ભાત કાપડની પાછળની બાજુએ દેખાય છે.
એક જ બાજુ ઉપયોગમાં લઈ શકાય તેવું (non-reversible) કાપડ બે કે વધારે તાણાનો અને કેટલીક વખત વાણાનો ઉપયોગ કરીને પણ બનાવી શકાય છે. આ પ્રકારના કાપડમાં સંકુલ (intricate) ભાત ઉપર અને બધા તાણા અને વાણા મુખપૃષ્ઠ પર ન દેખાય પરંતુ તે કાપડની પાછળની બાજુ જાળાના રૂપમાં ગંઠાયેલા હોય છે. આ પ્રકારમાં પ્રાચીન પર્શિયન અને બાઇઝન્ટાઇન આકૃતિવાળું કાપડ ગણી શકાય છે તેમજ હાલમાં જૅકાર્ડ અને જરીકામ કરેલ કાપડ ગણાય છે.
રૂંવાંવાળો વણાટ (pile weave) : રૂંવાંવાળા કાપડમાં સાદો વણાટ હોય છે, જેમાં વધારાના દોરા બાંધેલા કે વણાયેલા અને સપાટી પર કપાયેલા અથવા તો ગાળા(loop)ના રૂપમાં અસ્તિત્વ ધરાવતા હોય છે. આમાં ઘણા પ્રકારનાં ગંઠન આવરી શકાય છે; દા.ત., રૂંવાંવાળા અંગૂછા (towel), કૉર્ડરૉય (corduroy), રેશમી વેલ્વેટ (silk velvet) અને ઓરિયેન્ટલ ધાબળા (oriental rugs).
તાણામાં રૂંવાંવાળું કાપડ વધારાના તાણા વડે બનાવવામાં આવે છે. આ પ્રકારનું કાપડ બનાવવા માટે પ્રથમ એક સ્તરના તાણાઓના સમૂહને ઊંચો કરવામાં આવે છે અને પસાર થતો વાણો તેના તળિયાના પ્રથમ તાણા સાથે વણાય છે. રૂંવાં માટેના તાણા ઊંચા કરવામાં આવે છે અને એક સળિયો પૂરા પનામાં પસાર કરવામાં આવે છે. બાકીના તળિયાના તાણા ઉપાડીને ત્રીજો શેડ બનાવીને પછી તળિયાનો વાણો પસાર કરવામાં આવે છે. ત્યારબાદ સળિયો ખસેડી લેવામાં આવે છે, જેથી તાણામાં રૂંવાં બને છે. આ ક્રમનું પુનરાવર્તન અનેક વખત કરવામાં આવે છે. કપાયેલાં રૂંવાંવાળા (cut pile) મખમલની બનાવટમાં સળિયાના છેડા પરની તીક્ષ્ણ ધાર ત્યાંથી પસાર થતાં રૂંવાંવાળા તાણાને કાપે છે, જે બે સુંદર કપાયેલા રૂંવાંની હરોળ રૂપે અસ્તિત્વ ધરાવે છે. જોકે આ રીતમાં ઘણા તકનીકી ફેરફાર થયા છે. આ જ પાયાની પદ્ધતિમાં ફેરફાર કરીને રૂંવાંવાળા વણાટ માટેનાં યંત્રો અને પદ્ધતિ વિકસાવવામાં આવ્યાં છે.
જ્યારે સળિયો કાઢી લેવામાં આવે ત્યારે રૂંવાં કપાય નહિ તો આવર્તિત ગાળાની રચનાવાળું કાપડ બને છે. ટેરીપાઇલ-ફૅબ્રિકમાં તળિયાનો તાણો ખેંચાયેલો અને રૂંવાંવાળો તાણો ઢીલો રહે છે. જ્યારે વાણો પસાર કરવામાં આવે છે ત્યારે ઢીલો તાર (તાણો) ગાળાના રૂપમાં કાપડની બંને બાજુ બંધાય છે.
વેલ્વેટના બે સ્તરવાળા કાપડની બનાવટ માટે કાપડનાં બે પડ એકીસાથે સામસામે વણવામાં આવે છે; જેમાં લાંબાં રૂંવાંવાળા તાણાના દોરાથી બંને સ્તર જોડાયેલા હોય છે. કાપડ વણાયા પછી છરી વડે બંને સ્તર છૂટા પાડવામાં આવે છે.
કૉર્ડરૉય અને વેલ્વેટીન એ વાણાના આવર્તન(weft pile)વાળી રચનાઓ અથવા બંધારણ છે. લાંબા ગાળાના (long floats) વાણાના દોરાઓને તળિયાના વણાયેલા વાણાની વચ્ચે દાખલ કરવામાં આવે છે. કાપડના વણાટ બાદ લાંબા ગાળાના દોરા ઊંચા થાય છે. આમ હરોળમાં કપાયેલ રૂંવાંની રચના બને છે.
વેલ્વેટીનની બનાવટમાં સંપૂર્ણ કાપડની સપાટી પર લાંબા ગાળાનાં રૂંવાં બનાવવામાં આવે છે અને એકસરખી રીતે કાપીને વેલ્વેટની નકલ કરવામાં આવે છે. પૌરસ્ત્ય દેશોમાં અને સ્કૅન્ડિનેવિયાના પ્રદેશોમાં બનતા કામળા સાદા વણાટની રચના પર આધારિત છે. જેમાં ફૂમતાં(knots)ની રચના બનાવવામાં આવે છે. ફૂમતાંની દરેક હરોળ બે વાણાને પકડમાં રાખીને વણવામાં આવે છે. પૌરસ્ત્ય કામળાની રચનામાં 2.53 સેમી.માં 160 જેટલાં ફૂમતાંની સંખ્યા હોય છે, જેથી મૂળ સાદા વણાટની રચના સંપૂર્ણ રીતે ઢંકાઈ જાય છે.
જરી–કિનખાબની રચનાવાળું કાપડ (inlaid weave) : આ પ્રકારના કાપડમાં ચિત્ર ઉપસાવવા માટે ભાતવાળા તાણા કે વાણાને તળિયાના તાણા કે વાણાની વચ્ચેથી પસાર કરવામાં આવે છે.
જરી-કિનખાબના કાપડમાં રંગીન દોરા અથવા ધાતુના તાર અથવા બંનેને પ્રાથમિક વણાટ કરતાં સહેજ ઢીલા ઊપસે તેમ વણવામાં આવે છે. પ્રાથમિક વણાટ ગમે તે પ્રકારનો હોઈ શકે. પરંતુ જરી-કિનખાબ (brocaded pattern) પ્રાથમિક વાણાની વચ્ચે વાણાના રૂપમાં દાખલ કરીને પ્રાથમિક તાણાથી તેને બાંધવામાં આવે છે.
ઇતિહાસમાં 19મી સદીમાં કાપડવણાટની જૅકાર્ડ પદ્ધતિથી આ રચના વધારે પ્રચલિત બની. આ પહેલાં પણ ભારતમાં તથા પૂર્વના બીજા પ્રદેશોમાં આ પ્રકારના વણાટ પ્રચલિત હતા, જેમાં જરીવાળી ઢાકાની મલમલ, રેશમ તથા રાજા-મહારાજાઓના પોશાકોમાં વપરાતાં કલાત્મક કાપડ આનાં ઉત્તમ ઉદાહરણ છે. ગુજરાતમાં સૂરત શહેર તે વખતે અને આજે પણ આ પ્રકારના કામ માટે મશહૂર છે. વણાટકામની સાથે આ પ્રકારનો ધીમો પણ સંગીન ઉત્કર્ષ થયો છે. શરૂઆતમાં આ પ્રકારનું કાપડ ડ્રૉ લૂમ પર વણવામાં આવતું, જેમાં જે-તે પ્રકારનાં બૉબિન રાખવામાં આવતાં હતાં અને જરૂર પ્રમાણે પસાર કરીને વણાટકામ કરવામાં આવતું હતું. સામાન્ય રીતે વધારાના વાણા ભાત પ્રમાણે અને બાકીના પાછળની બાજુએ લાંબા ગાળાના રૂપમાં રહેતા હતા. યાંત્રિકીકરણ સાથે સ્વિવલ અને લૅપિટ પ્રકારની રચના અસ્તિત્વમાં આવી. સ્વિવલ પ્રકારમાં વધારાના વાણા પસાર કરવામાં આવે છે, જ્યારે લૅપિટમાં વધારાના તાણા દાખલ કરવામાં આવે છે. બંને પ્રકારના વણાટ જોવામાં સરખા લાગે છે પરંતુ બંનેના વણાટ ઝીણવટપૂર્વક તપાસતાં જુદા તરી આવે છે.
જૅકાર્ડ વણાટની રચના : આખા કાપડમાં પૂર્ણ ભાત ઉપસાવવા માટે જૅકાર્ડ વણાટ, જૅકાર્ડ રચના ધરાવતી સાળ પર વણવામાં આવે છે. દરેક તાણાને જરૂર પ્રમાણે નિયંત્રિત કરી કાપડનું વણાટકામ કરવામાં આવે છે. કલાત્મક કાપડ, પડદાનું કાપડ અને દમાસ્ક વગેરેના ઉત્પાદનમાં આ પદ્ધતિ વપરાય છે. આ કાપડ ઘણું મોંઘું હોય છે; કારણ કે વણાટપ્રક્રિયામાં વપરાયેલ સાળ માટે નવી ભાત પ્રમાણેનાં કાર્ડ બનાવવામાં વધારે સમય અને ઊંચી બુદ્ધિમત્તા જરૂરી છે. સાળની વણાટપદ્ધતિ ધીમી હોવાથી ઉત્પાદન ઓછું મળે છે. સામાન્ય રીતે આ પ્રકારના વણાટમાં એક કરતાં વધારે પ્રાથમિક વણાટનો ઉપયોગ ભાત ઉપસાવવા માટે કરવામાં આવે છે.
ડૉબી વણાટ : આ પ્રકારના વણાટથી પણ સમગ્ર કાપડ પર ભાત ઉપસાવી શકાય છે. આમાં જૅકાર્ડ કાર્ડના બદલે લાકડાની સાંકડી પટ્ટીના રૂપમાં તાણાનું નિયંત્રણ કરતી રચના સાળ પર ગોઠવવામાં આવે છે જેને ડૉબી કહેવામાં આવે છે. આ પ્રકારના વણાટમાં મર્યાદિત સાદી, નાની, ભૌમિતિક આકૃતિઓવાળી ભાત ટૂંકા ટૂંકા અંતરે આવર્તન પામે છે. આથી આ પ્રકારની બનાવટવાળું કાપડ ઓછું ખર્ચાળ હોય છે તેથી જૅકાર્ડ વણાટવાળા કાપડ કરતાં સોંઘું અને વધુ પ્રમાણમાં ઉપલબ્ધ બને છે.
5. ગૂંથેલું કાપડ (knitted fabrics)
કાપડમાં એક અથવા વધારે દોરાથી બનાવેલા આવર્તિત ગાળા(loops)ની શ્રેણીનું બીજી શ્રેણી સાથે બંધન બનાવી ગૂંથેલું કાપડ બનાવાય છે. જે આવર્તિત ગાળા કાપડની કિનારી અથવા લંબાઈને સમાંતર આવેલા છે, તેને વૉલસ (wales) કહે છે અને કિનારી અથવા લંબાઈને લંબરૂપે (આડા – crosswise) આવેલા છે, તેને કોર્સ (course) તરીકે ઓળખવામાં આવે છે. હાથથી ગૂંથણીનું કામ આશરે 1,000 વર્ષ પૂર્વે અરબસ્તાનના રણપ્રદેશમાં ભટકતી ટોળીઓ દ્વારા મૂળ શરૂ થયેલ, જે ઇજિપ્તમાંથી સ્પેન, ફ્રાંસ અને ઇટાલીમાં પ્રસરેલું માનવામાં આવે છે. ગૂંથીને કાપડ બનાવનાર ધંધાદારી મંડળીઓ પૅરિસ અને ફ્લૉરેન્સમાં મધ્ય યુગમાં હતી. ઑસ્ટ્રિયા અને જર્મનીમાં ઊઘડતા રંગના દોરાઓ વાપરી સાંકળની જેમ ગાંઠોવાળું ભરતકામ કરી કાપડ બનાવવામાં આવતું, નેધરલૅન્ડમાં કુદરતી ભાત જેમાં વધારાના દોરા કાપડની પાછળની બાજુ રહે તે પ્રમાણે ગૂંથીને આ કળાનો વિકાસ સાધવામાં આવેલ. ડચ પ્રદેશના ઘણા કુશળ કારીગરો ડેન્માર્કમાં વસતી ડેનિશ સ્ત્રીઓને આ કળા શીખવવા માટે ગયા હતા. 1589માં યાંત્રિક સાધન(frame knitting machine)ની શોધ થતાં હાથગૂંથણીની કળાનું મહત્વ ઘટ્યું, તેમ છતાં અત્યારે હાથગૂંથણી માટે વપરાતા દોરાના ઉત્પાદનનું મહત્વ કાપડઉદ્યોગમાં એક શાખા રૂપે છે.
આજપર્યંત ભારત અને આજુબાજુના પ્રદેશોમાં હાથથી કરવામાં આવતી ગૂંથણીનું મહત્વ છે, જેમાં એક સોયાથી કે બે સોયાથી ગૂંથણીનું કાર્ય કરવામાં આવે છે.
એક સોયાથી કરવામાં આવતી ગૂંથણી ગુજરાતમાં અંકોડીની ગૂંથણી તરીકે ઓળખાય છે જેમાં એક લાંબા પાતળા સોયાની આગળના ભાગે હૂક જેવી રચના બનાવેલી હોય છે, જેની મદદથી દોરાના આવર્તિત ગાળા બનાવી શકાય છે. આમાં પાતળા, વધુ વળ ચડાવેલા અને મજબૂત દોરાનો ઉપયોગ થાય છે. બે સોયા અથવા વધુ સોયાનો ઉપયોગ સામાન્ય રીતે ઊન કે માનવસર્જિત રેસામાંથી ગૂંથેલું કાપડ બનાવવામાં થાય છે. આ સોયા સાદા અણીવાળા હોય છે. તેમની જાડાઈ અને બનાવટમાં વાપરેલ દોરાની ગુણવત્તાના આધારે કાપડનું પોત અને ઘટ્ટતા બને છે. આ કળા હજુ પણ ગૃહઉદ્યોગ રૂપે ચાલે છે. હાથવણાટના ખાદીના કાપડની જેમ નાના પાયે ગૂંથણીનું કાર્ય પણ નાની મંડળીઓના રૂપમાં જ અસ્તિત્વ ધરાવે છે.
નિશ્ચિત સ્વરૂપમાં ગૂંથવાના યંત્રમાં એકસાથે આવર્તિત ગાળા ઉપસાવવામાં આવે છે. આ સાદી પદ્ધતિને આધુનિક યંત્રના પાયા રૂપે સ્વીકારીને તેમાં થોડાક ફેરફારો કરી ગૂંથણી માટેનાં અદ્યતન યંત્ર (highly sophisticated knitting machine) બનાવી શકાયાં છે.
ગૂંથણીના આવર્તન-ગાળામાં વપરાયેલ દોરાની લંબાઈ એ ટાંકાની લંબાઈ (stitch length) તરીકે ઓળખાય છે. સાદી ગૂંથણીના કાપડમાં એક ઇંચમાં આવેલ કોર્સની સંખ્યા, વૉલસની સંખ્યા ટાંકાની લંબાઈને સંબંધિત હોય છે.
ગૂંથેલા કાપડની સમતોલ સ્થિતિ (dimensional stability) માટે પાયાની બે સ્થિતિ ધ્યાનમાં રખાય છે : (1) કાપડને હવામાં કોઈ પણ પ્રકારના ખેંચાણ વગર મૂક્યા બાદની સ્થિતિ (dry relaxed), (2) પાણીમાં સ્થિર ડુબાડી રાખી ત્યારબાદ હવામાં કોઈ પણ ખેંચાણ વગર સૂકવીને મળતી સમતોલ સ્થિર સ્થિતિ (wet relaxed).
ગૂંથણ માટેનાં બધાં જ યંત્રોમાં સોય પ્રાથમિક સાધન છે. બે પ્રકારની સોય ઉપયોગમાં આવે છે : (1) અંકોડીવાળી (bearded), જે ઈ. સ. 1589માં અને (2) લૅચ (latch) પ્રકારની, જે ઈ. સ. 1847માં અસ્તિત્વમાં આવી હતી.
અંકોડીવાળી સોય : આ સોય પાતળા ધાતુના તારને એક છેડેથી વાળીને બનાવાય છે. આ છેડો કાર્યકારી હાથા (operating handle) તરીકે કામ કરે છે જ્યારે બીજા છેડાને આંકડાના રૂપમાં ફેરવીને તેમાં એક કાણું પાડવામાં આવે છે. ગૂંથણી દરમિયાન આ સોય ઉપરાંત બીજાં બે સાધન ઉપયોગમાં લેવાય છે. સોય અંદર જાય ત્યારે ગાળો બનાવવા માટે સિંકર (sinker) અને ગાળાને પકડી રાખવા માટે જોઈતું દબાણ સંચા વડે આપવામાં આવે છે. આથી સોય બીજો ગાળો બનાવવા માટે કાર્યરત બને છે. આ પ્રકારની સોય ઘણા પાતળા તારમાંથી બનાવીને ઝીણા પોતવાળું કાપડ બનાવવા માટે વાપરી શકાય છે.
લૅચ (latch) પ્રકારની સોય : આ પ્રકારની સોય આગળના ભાગે વાળેલા અને આધાર સાથે છૂટથી હલનચલન કરી શકે તેવા આંકડાના પ્રકારની હોય છે. ઘણી વખત તેને સ્વયંસંચાલિત સોય તરીકે ઓળખવામાં આવે છે, કારણ કે અહીં ગાળો બનાવવા માટે કોઈ પણ પ્રકારના દબાણની જરૂર હોતી નથી. તે દોરાના હૂક સાથેના ખેંચાણથી જ ગાળો બનાવે છે. જે પ્રકારના કાપડની જરૂર હોય તે પ્રમાણેની જાડાઈ(gauge)વાળી સોય ઉપયોગમાં લેવામાં આવે છે.
વેફ્ટ નિટિંગ : વેફ્ટ નિટિંગમાં વપરાતા ટાંકા કાપડના દેખાવ અને ગુણધર્મને અસરકર્તા હોય છે. સાદા (plain) અથવા જર્સી (jersey), પટ્ટી અથવા ધારીવાળા (rib) અને વેવી (purl-wavy) વગેરે પ્રકારના પાયાના ગૂંથણના વિભાગ પાડી શકાય છે. સાદા ટાંકામાં દરેક આવર્તનગાળો બીજામાંથી પસાર કરીને એક જ બાજુ ખેંચવામાં આવે છે. ધારીવાળા ટાંકામાં કોર્સના ગાળાને કાપડની બન્ને બાજુ ખેંચી ઉપસાવવામાં આવે છે. કાપડની સામસામે ગોઠવેલા સોયામાંથી એક જ દોરો પસાર કરીને ખેંચવામાં આવે છે.
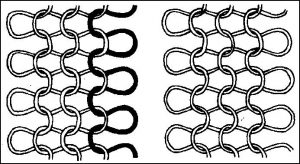
આકૃતિ 7 : ગૂંથણીના પ્રકાર
આથી દરેક સોયાથી તેના આનુષંગિક ભાગ સાથે ગૂંથાઈને એક વર્તુળ બનાવે છે અને પટ્ટી બને છે. 2 : 2 ધારીના ગૂંથણમાં બે સોયાની જોડનો ઉપયોગ કરવામાં આવે છે, જેમાં બે દોરા એકીસાથે ગૂંથાય છે. તરંગ (wavy-purl) પ્રકારના ગૂંથણમાં કાપડની વિરુદ્ધ દિશામાં ગાળા ખેંચાય છે, જેથી કાપડની બન્ને બાજુ સાદા વણાટ જેવા ટાંકા ઊપસી આવે છે. જૅકાર્ડ રચના પણ ગૂંથણીના યંત્ર સાથે જોડી શકાય, જેથી જુદી જુદી સોયોથી દરેક કોર્સ અથવા દરેક બે કોર્સને સમતોલ કરી શકાય છે. ગૂંચવણભરેલી ભાતવાળું ગૂંથણ કરી શકાય છે. ટક ટાંકા(tuck-stitch)માં સોય પર કેટલાક ટાંકા ભેગા થાય છે, જે દરેક કોર્સની ગૂંથણીમાં ગૂંથાતા નથી, પરંતુ થોડા અંતરે ગૂંથાઈને ભરાવદાર કાપડ ઉત્પન્ન કરે છે.
ગૂંથણ માટેનાં યંત્રોના પ્રકાર : ગૂંથવા માટેનાં યંત્રો બે પ્રકારનાં હોય છે : સપાટ અને વર્તુળાકાર. સપાટ યંત્રમાં તેની સોયો એક અથવા બે સપાટ પટ્ટીઓ કે જે એકબીજીને કાટખૂણે હોય છે તેની પર જડેલી હોય છે. આ દરેક પટ્ટી ક્ષિતિજ સાથે 45oના ખૂણે ગોઠવેલી હોય છે. ગૂંથાયેલી કાપડની પટ્ટીની ઉપરની ધારથી નીચે તરફ પસાર થાય છે. ગૂંથણીની પ્રક્રિયામાં સોયો, કૅમ(CAMS)ની રચના વડે ઉપર-નીચે થાય છે, જે દોરા વડે નિયંત્રિત થતી રચના સાથે જોડાયેલ હોય છે. તે યંત્રની પૂર્ણ લંબાઈ પર ફરી શકે છે. કાપડનો પનો વપરાતી સોયોને વધારી અથવા ઘટાડીને બદલી શકાય છે તથા જોઈએ તે પ્રમાણેના આકારવાળું કાપડ બનાવી શકાય છે, જેને સીવી નવી ફૅશનનાં કપડાં પણ બનાવી શકાય છે. આ પ્રકારનાં યંત્રો હાથથી ચલાવવા માટે ઉપયોગી છે; પરંતુ વ્યાપારી ધોરણે ઉત્પાદન કરવા માટે શક્તિસંચાલિત કરવામાં આવે છે. એક કરતાં વધારે રંગના દોરા વાપરી જૅકાર્ડ રચનાનો ઉપયોગ કરી જુદા જુદા ટાંકાના પ્રકાર વડે ઘણા પ્રકારનું વિવિધતાવાળું કાપડ ઉત્પન્ન કરી શકાય છે. સુતરાઉ દોરાના ઉપયોગથી ઝીણું ગૂંથણ કરી હોઝિયરીના ઉત્પાદનમાં સ્વયંસંચાલિત રચનાથી કાપડની બનાવટમાં વિવિધતા અને આકાર ઉત્પન્ન કરવામાં આવે છે.
વર્તુળાકાર યંત્રમાં સોયો નળાકારની દીવાલમાં ઘીસી પાડીને બેસાડવામાં આવે છે. કેટલાંક યંત્રોમાં મધ્યભાગમાં પણ સોય ધરાવતો નળાકાર હોય છે. ગૂંથણીની પ્રક્રિયા દરમિયાન કૅમની ધરીથી સોયના આધાર હાલે છે, જે ઉપર-નીચે થઈને દોરાનાં આવર્તન બનાવે છે અને ગાળાની શ્રેણીને ગૂંથણીમાં પરોવી આનુષંગિક ગાળાની શ્રેણી બનાવે છે. આ પ્રકારના ઓછા સંકુલ યંત્રમાં દોરો પૅકેજમાંથી પૂરો પાડવામાં આવે છે અને દરેક સોય નળાકારના એક ફેરા વખતે ગાળાના આવર્તન માટે જરૂરી દોરા ખેંચે છે. આધુનિક યંત્રની રચનામાં 100 જેટલાં પૂરણીસાધનો (feeders) હોય છે અને દરેક સોય નળાકારના એક ફેરામાં 100 જેટલા દોરા ઉપાડી શકે છે તેમજ અંકોડાવાળી અને લૅચ બન્ને પ્રકારની સોય વાપરવામાં આવે છે. મધ્યમ પોતવાળાં કાપડ બનાવવા માટે આધુનિક યંત્રમાં 90થી 100 પૂરણીસાધન હોય છે. નાની પટ્ટીરૂપ, પકડરચના બે સોયની વચ્ચે દાખલ કરવામાં આવે છે, જે સોયને પ્રવૃત્ત રાખે છે અને બનેલા કાપડને પકડી રાખે છે, જેથી નવા ટાંકાની રચના વખતે કાપડ ઊંચકાઈને ગૂંચવણ ઊભી ન કરે. યંત્રમાં પૅટર્ન (ભાત) માટે પૅટર્નચક્ર બેસાડવામાં આવે છે, જેથી ટક (tuck) પ્રકારનું કાપડ બનાવી શકાય છે. યંત્રથોભન(stop motion)ની ક્રિયા, દોરાના તૂટવા સાથે જરૂરી છે, કારણ કે દોરાના ખેંચાણ પર કાપડની રચના અને દેખાવનો આધાર છે. આથી દોરાના ખેંચાણ માટે જુદી જુદી પદ્ધતિઓ અપનાવાય છે. વૈકલ્પિક રચના તરીકે યંત્રમાં દોરાની પૂરણી અને દોરાની લંબાઈનું માપ એ બધું સંતોષકારક માનવામાં આવે છે. વર્તુળાકાર પટ્ટી-યંત્ર(circular rib machine)માં બહારની બાજુ ખાંચાઓ (slots) હોય તેવો એક ઊભો નળાકાર અને આડી (horizontal) વર્તુળાકાર પ્લેટ કે જેની ત્રિજ્યાને અનુરૂપ ખાંચાઓમાં સોયોના બે સેટ એકબીજાને કાટખૂણે રહે તેવી રચના કરેલ હોય છે. સાંધા વગરના નળાકાર (tubular) રૂપમાં હોઝિયરીનું કાપડ વર્તુળાકાર ગૂંથણીના યંત્ર પર બનાવવામાં આવે છે.
આધુનિક હોઝિયરીનાં યંત્ર જેવાં કે કૉમેટ(Komet)માં એક જ સપાટીમાં રહે તેવી રીતે એકબીજીની વિરુદ્ધ દિશામાં હલનચલન કરી શકે તેવી બે હૂક જેવી સોય ગોઠવવામાં આવે છે, જેથી પગ અને પગના પંજાના આકારનું પડ સળંગ રીતે ગૂંથી શકાય છે. યંત્રના ભાગને બીજા મશીન પર સિલાઈ કરી બંધ કરવામાં આવે છે. ગીતાઝ (Getaz) પ્રકારના યંત્રમાં સાંધો ઉપરના ભાગને બદલે તેની નીચેના ભાગમાં આવે છે.
ખાસ પ્રકારના ફૅશનવાળા કાપડના જાંઘિયા અને પાયજામા સિવાયનું કાપડ સામાન્ય રીતે વર્તુળાકાર ગૂંથણીના યંત્ર પર બનાવવામાં આવે છે. જાંઘિયા અને ગંજી પ્રકારની હોઝિયરીને નળાકાર કાપડમાંથી કાપી સીવી અને ચુસ્ત રહે તે રીતે બનાવવામાં આવે છે. આ પ્રકારનું કાપડ ખાસ યંત્ર પર બનાવવામાં આવે છે, જેમાં સામસામેના છેડા કપાઈને યોગ્ય રીતે સિવાઈને ચુસ્ત રહે તેવી રચના થાય છે. આ પ્રકારના તૈયાર કપડાની બનાવટમાં ખેંચી શકાય તેવા નાયલૉન સ્પૅનડેક્સ અને ટેક્સ્ચ્યુરાઇઝ્ડ દોરાઓના વિકાસથી કાપડની ઉપયોગી ગુણવત્તામાં સુધારો થયો છે.
મોટાભાગનાં હોઝિયરી કાપડ ધોલાઈ, શુષ્કન અને તૈયાર કપડાના માપ પ્રમાણેનાં ગરમ પાતળાં પતરાં અથવા લાકડાનાં પાટિયાં પર ઇસ્ત્રી થઈને તૈયાર થાય છે તેને બોર્ડિંગ પદ્ધતિ કહે છે. નાયલૉનના કાપડને પ્રીસેટિંગ પદ્ધતિ પછી રંગ કરીને પરિષ્કૃતિ (finishing) આપવામાં આવે છે જેથી કાપડ તેનો મૂળ આકાર જાળવી રાખે છે.
ગૂંથેલા કાપડમાં રુવાંટી (pile) ઉપસાવવા માટે કાર્ડેડ સ્લાઇવરનો ઉપયોગ કરવામાં આવે છે. રુવાંટી ઉપસાવવા માટે કાર્ડેડ સ્લાઇવરમાંથી છૂટા તાંતણાને V આકારના પટ્ટાની મદદથી કાપડમાં દાખલ કરવામાં આવે છે. રુવાંટીની લંબાઈ સ્લાઇવરમાં વપરાયેલ તાંતણાની લંબાઈ પર આધાર રાખે છે. જૅકાર્ડ રચના સાથેના વર્તુળાકાર ગૂંથવાના યંત્રમાં ઇલેક્ટ્રૉનિક રચનાનો ઉપયોગ કરી ગૂંથવા માટેનાં આધુનિક યંત્ર બનાવવામાં આવે છે.
તાણાનું ગૂંથણ (warp knitting) : તેના બે પ્રકાર છે : રાશલ અને ટ્રાઇકૉટ.
રાશલ : રાશલમાં સામાન્ય રીતે જાડા દોરા વપરાય છે. આધુનિક સંશોધન પ્રમાણે તેમાં તમામ પ્રકારના તાંતણા(staple yarn)નો ઉપયોગ કરવામાં આવે છે. આ પ્રકારના યંત્રમાં એક પ્લેટમાં સોય ઉપર-નીચે થાય છે જેને ટ્રિક પ્લેટ તરીકે ઓળખવામાં આવે છે. કાપડ આગળ ખેંચાય અને સોય અંદરના ભાગે ગાળા બનાવીને પાછી ફરે ત્યારે બનેલા ગાળાને ઉપરની બાજુ ઊંચકાઈ જતો રોકવામાં આવે છે. ગાઇડ બાર (guide bars) વડે સોયમાં દોરાની પૂરણી અને સંચાલનનું કાર્ય થાય છે. જ્યારે સોય સૌથી નીચેના ભાગમાં હોય છે ત્યારે ગૂંથણપ્રક્રિયા શરૂ થાય છે અને સોયની હૂક જેવી રચનાથી કાપડ સુધીના નવા ગાળા બને છે. જ્યારે સોયો ઉપર જાય છે ત્યારે દોરાના ગાળા લૅચો ખોલીને તેમની નીચે જઈ પૂર્ણ બને છે. સોયો વચ્ચેથી ગાઇડ બાર પસાર થાય છે અને આગળનો બાર સોયની જગાના પ્રમાણમાં આગળ ખસે છે. ગાઇડ બાર ખસીને મૂળ સ્થાને આવે છે ત્યારે આગળનો બાર સોયના હૂકમાં દોરાને ભરાવે છે, સોય નીચે આવે છે ત્યારે ગાળાને પકડી રાખવા લૅચ બંધ થાય છે અને જૂના ગાળા પૂર્ણ બનાવે છે. બીજા તાણાગૂંથણના પ્રકારના કાપડના પ્રમાણમાં રાશલ પદ્ધતિથી ગૂંથેલ કાપડ સામાન્ય રીતે જાડા દોરાનું અને ખુલ્લી ગૂંથણીવાળું હોય છે.
ટ્રાઇકૉટ : આ પ્રકારના તાણાગૂંથણમાં દોરાનાં બે પડ વડે ગૂંથણી કરવામાં આવે છે. કાપડની ઉપરની બાજુએ ઊભી અને કાપડની પાછળની બાજુ આડી પાતળી પટ્ટીના રૂપમાં તે જોવા મળે છે. આ પ્રકારના ગૂંથણનાં યંત્ર હલકાં કાપડ બનાવવા માટે ઉપયોગમાં લેવાય છે.
વણાટ કે ગૂંથણી વગરનું કાપડ (non-interlaced fabric) : ફેલ્ટ તથા વણાટ/ગૂંથણ વગરના કાપડનો વિકાસ પ્રાથમિક તબક્કામાં છે, જેની ચોક્કસ વ્યાખ્યા આપવી ઘણી અઘરી અને ચર્ચાસ્પદ છે. સામાન્ય સમજ પ્રમાણે આ પ્રકારનું કાપડ એટલે એવું કાપડ કે જેમાં તંતુઓ અવ્યવસ્થિત (randomly) અથવા વ્યવસ્થિત (oriented) રીતે પડમાં તંતુમય બંધારણ બનવાથી બને છે.
ફેલ્ટ : ફેલ્ટ એવા પ્રકારનું કાપડ છે જેમાં તંતુમય બંધારણ ઊન, ફર અથવા ખાસ પ્રકારના વાળને ગરમી, ભેજ અને દબાણથી એકબીજા સાથે એક જ સ્થિતિમાં ગોઠવીને તંતુમય પડના રૂપમાં ફેરવવામાં આવે છે. બીજા તંતુઓ એકલા ફેલ્ટમાં ફેરવાતા નથી. પરંતુ ઊનની હાજરી વાહક (carrier) તરીકે કાર્ય કરે છે. આ ગુણધર્મનો ઉપયોગ કરીને ઔદ્યોગિક રીતે જુદા જુદા પ્રકારનું કાપડ બનાવાય છે. જેવું કે ઊની કામળા તેમજ ફર અને ઊનમાંથી હૅટ અને વણાટવાળા ફેલ્ટ, જેમાં બિલિયર્ડ ટેબલના પાતળા કાપડથી માંડીને ઔદ્યોગિક વપરાશમાં આવતા પાણીના શોષક (dewatering) જાડા કાપડનો સમાવેશ થાય છે. ફેલ્ટને સૌપ્રથમ કાપડ તરીકે ગણી શકાય. તેના અસ્તિત્વ અને બનાવટના ઘણા ઉલ્લેખ પ્રાચીન ઇતિહાસમાં મળી આવેલ છે.
બૉન્ડિંગ : વણાટ વગરનું કાપડ બનાવવા માટે ઘણી પદ્ધતિઓ શોધવામાં આવી છે. હજુ પણ તેમાં વિકાસ થઈ રહ્યો છે. રસાયણ વડે ચોંટાડીને (adhesive bonding) કાપડ બનાવવા માટે તંતુઓના પડને રસાયણ છાંટીને સૂકવવામાં આવે છે. ત્યારબાદ તેને કાયમી બનાવવા માટે ઊંચા તાપમાને ક્યૉરિંગ કરવામાં આવે છે. આ પ્રકારના પડ (web) કાર્ડિગ મશીન પર કરવામાં આવે છે. એક કરતાં વધારે પડ યોગ્ય રીતે ગોઠવીને તેની જરૂરી જાડાઈ મેળવવામાં આવે છે.
કાપડમાં તંતુઓ જુદી જુદી રીતે એકબીજાને ચોંટીને વ્યવસ્થિત રૂપમાં ભેગા રહી શકે છે. આ કાપડને લેટેક્સ રબર, કુદરતી રબર, ઍક્રિલિક રસાયણો અથવા રેઝિન અને બીજા રસાયણના છંટકાવ કરીને અથવા તેમના દ્રાવણમાં બોળીને રોલ વચ્ચે દબાવીને તેમાંથી પસાર કરી તૈયાર કરવામાં આવે છે. ફીણ પદ્ધતિ અથવા રાસાયણિક ચૂર્ણ છાંટીને આસંજક રસાયણ એકસરખું લગાવીને તથા ગરમીથી ચોંટી જાય તેવા તંતુઓ(thermoplastic fibre)ને મિશ્રિત કરી ગરમ કરવાથી તંતુઓના સમૂહને મજબૂત અને કાયમી બનાવી શકાય છે.
યાંત્રિક રીતે સંયોજિત કાપડ વધુ પ્રમાણમાં દબાણ આપીને બનાવવામાં આવે છે. તે યાંત્રિક રીતે મજબૂતાઈ મેળવે છે. ઘણી વખત પડમાં ટેક્સ્ચ્યુરાઇઝ્ડ દોરા અથવા સૂતરના પાતળા દોરા તેની લંબાઈને સમાંતર વચ્ચેના ભાગે (બે પડની વચ્ચે) ગોઠવવામાં આવે છે. કંટકીય સોય (barbed needle) વડે કાણાં પાડીને ગંઠન કરવામાં આવે છે. આથી કાપડની મજબૂતાઈ વધે છે અને આકાર જળવાઈ રહે છે. આધુનિક સોય છિદ્રણ (needle punching) અથવા ફેલ્ટિંગ યંત્રમાં એક મિનિટમાં 900 જેટલાં ગંઠન થાય છે. ઉપરાંત કાપડમાં વપરાતા તંતુઓના પ્રકારના આધારે સોયની પસંદગી થાય છે.
આવરિત કાપડ (laminating) : ઘણાં વર્ષોથી સાદા વણાટના કાપડ સાથે કુદરતી રબરને સંયોજિત કરીને વરસાદી કાપડ (rain wear – rain coat) તૈયાર કરવામાં આવે છે. હાલમાં આવરિત કાપડ બનાવવા માટે સાદા કાપડ સાથે પૉલિયુરેથીન અથવા બીજા બહુલક રસાયણની પ્રક્રિયા કરવામાં આવે છે. કાપડનાં બંને પડને સળંગ પડ રૂપે અથવા જુદી જુદી જગ્યાએથી ફ્લેમ બૉન્ડિંગ કરીને અથવા સંયોજિત ચૂર્ણ વડે ચોંટાડવામાં આવે છે. આ આવરિત પ્રક્રિયા કાપડનાં બંને પડને ચોંટાડવાની પ્રક્રિયા સુધીની છે. આમાં વપરાતાં કાપડનાં પડ ઘણાં પાતળાં હોય છે અને કાપડ ઓછામાં ઓછું અક્કડ (stiff) બને તે રીતે સંયોજિત પદાર્થની પસંદગી કરવામાં આવે છે. આ પ્રકારનું કાપડ ઘણા ઉપયોગમાં આવે છે; દા.ત., જે કાપડનાં પડ પારિમાણિક (dimensionally) રીતે ર્દઢતાયુક્ત (stable) હોય તેને પારિમાણિક રીતે ઢતા વગરના કાપડના પડ સાથે સંયોજિત કરવાથી નવા બનતા કાપડમાં પારિમાણિક ઢતાવાળા આવરિત કાપડના જેવા ગુણધર્મો મેળવી શકાય છે. આવરિત કાપડ તરીકે એસિટેટ ફાઇબરમાંથી ગૂંથેલાં કાપડ ઘણી વાર વાપરવામાં આવે છે.
6. વસ્ત્રને પરિષ્કૃત કરનારી પ્રક્રિયાઓ (textile finishing processes)
મૂળભૂત પદ્ધતિઓ અને પ્રક્રિયાઓ : ઓપ આપવાની પદ્ધતિઓમાં રંગવાની પ્રક્રિયા સાથે સંકળાયેલ પ્રક્રિયાઓ સિવાયની ઔદ્યોગિક ધોરણે અપનાવવામાં આવતી યાંત્રિક અને રાસાયણિક પ્રકારની બધી જ પ્રક્રિયાઓનો સમાવેશ કરવામાં આવે છે. આ પ્રકારની પ્રક્રિયાઓનો હેતુ સાળ (loom) અથવા ગૂંથણયંત્ર (knitting) પર તૈયાર થયેલ કાપડની માગ વધારવાનો છે. પરિષ્કૃત કરતા પહેલાં કાપડ પર કેટલીક વધારાની પ્રક્રિયાઓ પણ કરવામાં આવે છે; દા.ત., રંગપ્રક્રિયાની પહેલાં સ્પર્શ સુધારવા, પ્રવાહી ચૂસી શકે તેવું બનાવવા તથા તેને સફેદ કરવા માટેની જરૂરી એવી કાંજી દૂર કરવાની (desizing), સ્કાવરિંગ (આલ્કલીની પ્રક્રિયા) અને વિરંજન (bleaching) પ્રક્રિયા કરવામાં આવે છે. કાપડના ગુણધર્મોમાં વધારો કરે તેવી પૂર્વસંકુચન (pre-shrinking) પ્રક્રિયા પણ કરવામાં આવે છે. કાપડ સામાન્ય રીતે મેલું, કડક અને દેખાવમાં અનાકર્ષક હોય છે. તેનું આંખને ગમે તેવા આકર્ષક કાપડમાં રૂપાંતર કરવા માટે કૌશલ્યપૂર્ણ પ્રક્રિયાની જરૂર પડે છે. આ પ્રક્રિયા કરતાં પહેલાંના કાપડને પાણકોરું (grey goods) અથવા રેશમી કાપડમાં ગંજીકાપડ (greige goods) કહે છે. પહેલાં કાપડ પરિષ્કૃત કરવા અંગેની સાદી પદ્ધતિઓ અખત્યાર થતી હતી. તે ઘણાં વર્ષોના અનુભવ પછી ઉદભવેલી અંગ્રેજ અને સ્કૉટિશ પરિષ્કૃત પદ્ધતિઓ તરીકે ઓળખાતી હતી. બ્રિટનનું ઘણું કાપડ તેની ઊંચી ગુણવત્તા અને પરિષ્કૃત કરવાની આવડતને આભારી હતું. આધુનિક ઓપ આપવાની પદ્ધતિઓનો વિકાસ અનેક શોધોને આભારી છે.
કાપડના પરિષ્કરણની પ્રાથમિક પ્રક્રિયાઓ (preparatory processes) : વણાયેલા કાપડ પર પરિષ્કરણ પ્રક્રિયા કરતા પહેલાં કેટલીક પ્રાથમિક પ્રક્રિયા કરવી પડે છે. કાપડની બનાવટને સરળ બનાવવા માટે કાપડના ઉત્પાદન પહેલાં તાણામાં ઉમેરવામાં આવેલ અને કાપડમાંના તંતુઓ અથવા તાંતણાઓમાં રહી ગયેલ અશુદ્ધિઓને દૂર કરવી પડે છે. વિરંજન પ્રક્રિયા કાપડને સફેદ બનાવવા અથવા રંગ કરવા માટે જરૂરી છે. કેટલીક ઉપયોગી પ્રક્રિયાઓનો ક્રમ અહીં દર્શાવેલ છે. આ ક્રમ યોગ્યતા મુજબ બદલી શકાય છે અથવા સરળતા પ્રમાણે ગોઠવવામાં આવે છે.
કોરા કાપડની ચકાસણી (mending) : આ પદ્ધતિ ખાસ કરીને ઊની કાપડમાં આવતી નુકસાની તપાસવા માટે વપરાતી હતી. પરંતુ હાલમાં દરેક પ્રકારના કાપડ માટે વાપરવામાં આવે છે. કાપડની બનાવટ વખતે રહી ગયેલી ખામીઓ અથવા થયેલ નેકસાનનો અંદાજ લેવામાં આવે છે તેમજ શક્ય હોય તેનું નિવારણ કરવામાં આવે છે. નુકસાની જેવી કે વધારાના દોરા, યંત્રનાં ઊંજણ તેમજ તૂટેલા કે નહિ નખાયેલ તાણા અથવા વાણા (missing warp or weft) વગેરેની નુકસાની ચકાસીને દૂર કરવામાં આવે છે.
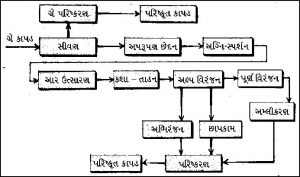
આકૃતિ 8 : આર્દ્ર પ્રક્રિયાઓનો ક્રમ
કાંજી દૂર કરવાની પદ્ધતિ (desizing) : કાપડમાંના તાણા પર વણાટની સુગમતા માટે કાંજી કરેલ હોય છે જેને આ પદ્ધતિ દ્વારા દૂર કરવામાં આવે છે. કાંજીમાં મોટાભાગે કાર્બોદિત પદાર્થો (સ્ટાર્ચ, સી.એમ.સી. વગેરે) વપરાય છે. આ પદાર્થો સામાન્ય રીતે સૂક્ષ્મ જીવાણુ દ્વારા અથવા માલ્ટેઝ પ્રકારના ઉત્સેચક (desizing agents) વડે વિભાજિત કરીને અથવા ઉપચયન(oxidation)થી વિભાજિત કરીને પાણીમાં દ્રાવ્ય સ્થિતિમાં લાવી દૂર કરવામાં આવે છે. જો કાપડમાં રાસાયણિક પદાર્થો(જેવા કે પૉલિવાઇનિલ આલ્કોહૉલ, ઍક્રિલિક વગેરે)નાં જુદાં જુદાં સંયોજનો વાપરવામાં આવેલ હોય તો વપરાયેલા પદાર્થને અનુરૂપ યોગ્ય પ્રક્રિયા દ્વારા દૂર કરવામાં આવે છે. રેશમ માટે ગુંદર દૂર કરવાની (degumming) અને ઊન માટે અપસ્નેહન (degreasing) પ્રક્રિયા તરીકે ઓળખવામાં આવે છે.
કુદરતી તથા કૃત્રિમ અશુદ્ધિઓ દૂર કરવા માટેની અભિમાર્જન (scouring) પ્રક્રિયા : સુતરાઉ કાપડમાં રહેલ કુદરતી અશુદ્ધિઓ જેવી કે કપાસનાં છોડાં, બીજના ટુકડા, પાંદડાંના અવશેષ તથા મીણ જેવા પદાર્થો અને કૃત્રિમ રીતે કાંતણ અને વણાટપ્રક્રિયા વખતે ઉમેરેલ કાંતણતેલ (spinning oil), સાઇઝિંગ પદાર્થો, યંત્રના ઊંજણના ડાઘા વગેરે દૂર કરવા માટે સુતરાઉ કાપડને ભઠ્ઠામાં ભરવામાં આવે છે, જેને ભઠ્ઠાની પ્રક્રિયા (kiering process) તરીકે ઓળખવામાં આવે છે. જો સુતરાઉ કાપડના વણાટમાં રંગીન દોરા વાપરવામાં આવેલ હોય તો તેમાં વપરાયેલ રંગને અનુરૂપ આ પદ્ધતિમાં ફેરફાર કરવામાં આવે છે. (રંગ પણ યોગ્ય પ્રકારના હોય તે પ્રાથમિક જરૂરિયાત છે.)
સૂતર અને માનવસર્જિત રેસાઓના મિશ્રણથી અથવા માનવસર્જિત રેસાઓમાંથી બનાવેલ કાપડ માટે આ પ્રક્રિયા ઓછા સમય સુધી અને નીચા તાપમાને તથા રાસાયણિક પદાર્થોની ઓછી સાંદ્રતાએ કરવામાં આવે છે. માનવસર્જિત રેસાઓમાં સુતરાઉ કાપડમાં દર્શાવેલ અશુદ્ધિઓ હોતી નથી તેથી આ પ્રક્રિયા ઘણુંખરું કરવામાં આવતી નથી.
વિરંજન પ્રક્રિયા : વિરંજન પ્રક્રિયાથી કુદરતી તથા કૃત્રિમ રંગજન્ય પદાર્થો દૂર કરી કાપડને સફેદ બનાવવામાં આવે છે. આ પ્રક્રિયામાં ઉપચયન અથવા અપચયનકર્તા વાપરી રંગને દૂર કરવામાં આવે છે. આ માટે કાપડમાં વપરાયેલા તંતુઓના ગુણધર્મો પ્રમાણે રસાયણ વાપરવામાં આવે છે. સામાન્ય રીતે સોડિયમ હાઇપૉક્લોરાઇડ અને આલ્કેલાઇન હાઇડ્રોજન પૅરૉક્સાઇડથી સુતરાઉ અને સુતરાઉ તથા માનવસર્જિત રેસાઓના મિશ્રણથી બનાવેલ કાપડ, સલ્ફર ડાયૉક્સાઇડથી ઊન અને પ્રાણીજન્ય રેસાઓને વિરંજિત કરવામાં આવે છે. માનવસર્જિત રેસાને સફેદ કાપડ તરીકે તૈયાર કરવાનું હોય તો સોડિયમ ક્લોરાઇટ અથવા તેના બંધારણમાં વપરાયેલ રસાયણને આધારે પ્રક્રિયા કરવામાં આવે છે. કાંજી દૂર કરવાની પ્રક્રિયાથી કાપડને સફેદ બનાવવાની વિરંજન પ્રક્રિયા સુધીની પ્રક્રિયાઓને વિરંજન પ્રક્રિયા તરીકે ઓળખવામાં આવે છે. આ બધી પ્રક્રિયાઓ તૂટક તૂટક તથા સળંગ રૂપમાં થઈ શકે છે. આ પ્રક્રિયાઓને નીચે પ્રમાણે દર્શાવવામાં આવે છે : (1) ભઠ્ઠાની પ્રક્રિયા અથવા ઘાણ પ્રમાણે વહેંચાયેલ પ્રક્રિયા (batchwise process), (2) સળંગ પ્રક્રિયા અથવા સતત પ્રક્રિયા (continuous process), (2અ) ખુલ્લા પના(open width)ની સતત પ્રક્રિયા, (2બ) દોરડાના રૂપ(rope form)માં સતત પ્રક્રિયા, (3) અર્ધસતત પ્રક્રિયા (semi continuous process).
મર્સરાઇઝેશન : કૉસ્ટિક સોડાના લગભગ 24 %ના સાંદ્ર દ્રાવણમાં દોરા અથવા કાપડને ખેંચાણમાં રાખી બોળવામાં આવે છે. ત્યારબાદ પાણીથી ધોઈ ઍસિડથી તટસ્થ કરવામાં આવે છે. આ પ્રક્રિયામાં સૂતરના તાંતણા કાયમી રીતે કદમાં ફૂલે છે. આ પ્રક્રિયાને મર્સરાઇઝેશન કહેવામાં આવે છે. આ પ્રક્રિયાથી સૂતરનાં ચળકાટ, દેખાવ, મજબૂતાઈ અને રંગ પ્રત્યેનું આકર્ષણ વધે છે. દોરાનું તથા કાપડનું મર્સરાઇઝેશન કરવા માટે અલગ અલગ યંત્રો હોય છે. આ પ્રક્રિયાથી કાપડમાં માત્ર ભૌમિતિક ફેરફાર જ થાય છે. આધુનિક મત પ્રમાણે કૉસ્ટિક સોડાની જગ્યાએ લિકર એમોનિયા પણ વાપરી શકાય. આ પ્રક્રિયામાં વપરાયેલ રસાયણ ભેગું કરી ફરીવાર વાપરવા યોગ્ય બનાવી શકાય છે.
કાપડ સૂકવવાની પદ્ધતિ (drying process) : કાપડ ઉપર પ્રક્રિયા કરવા માટે પાણીનો ઉપયોગ કરવામાં આવે છે. જે પાણી પ્રક્રિયા દરમિયાન કાપડમાં રહે છે તેને દૂર કરવું જરૂરી છે. આ પાણી વરાળસ્વરૂપે ઉડાડીને દૂર કરવું ઘણું ખર્ચાળ હોય છે. કાપડને સૂકવવા માટે પ્રથમ કાપડમાંથી યાંત્રિક રીતે પાણી દૂર કરવામાં આવે છે. કાપડને બે રબરના રોલરમાંથી પસાર કરીને (નિચોવવાની પ્રક્રિયા – squeezing), સેન્ટ્રિફ્યુઝ દ્વારા, વૅક્યુમ સક્શન પટ્ટી દ્વારા અથવા ખાસ પ્રકારના છિદ્રાળુ સપાટીવાળા રોબરટો રોલ અથવા કાગળના રોલ વગેરેનો ઉપયોગ કરી તંતુઓ વચ્ચેનું પાણી દૂર કરવામાં આવે છે. બાકી રહેલા પાણીને ડ્રાયર્સ વડે દૂર કરવામાં આવે છે. જો કાપડ વધારે પડતું સુકાઈ જાય તો અક્કડ સ્પર્શ(harsh hand)વાળું બને છે. આથી ડ્રાયર્સનું ઉષ્ણતામાન, સૂકવવા માટેનો સમય તથા કાપડની ભેજગ્રાહિતા(moisture regain)ને ધ્યાનમાં રાખી કાપડને સૂકવવું જરૂરી બને છે.
કાપડના દેખાવમાં વધારો કરવા વપરાતી પરિષ્કરણ પ્રક્રિયાઓ (shearing and cropping process) : આ પ્રક્રિયા દરેક પ્રકારના તંતુરુવાંમાંથી બનાવેલ કાપડ પર કરવામાં આવે છે. તેમાં કાપડની રુવાંટી (pile) તથા ઊંચા રહેલા ટૂંકા તંતુઓ કાપડને સમાંતર એકસરખી રીતે ગોળ ફરતા નળાકાર, કે જે ધારદાર પાતળા વાયરથી ઢંકાયેલ હોય છે, તેની પરથી પસાર કરતાં કપાઈ જાય છે તથા છૂટા તાંતણા ઊંચકાઈ જાય છે. આ પ્રક્રિયા બાદ તુરત જ બ્રશ જેવા રોલ પરથી કાપડ પસાર થાય છે અને કપાયેલ તથા છૂટા પડેલા તંતુઓ કે તાંતણાઓને કાપડની સપાટી પરથી દૂર કરવામાં આવે છે, જેને બ્રશિંગ અથવા ક્રૉપિંગ તરીકે ઓળખવામાં આવે છે.
સિંજિંગ : દોરા અથવા કાપડને જ્વાળા (gas flame) અથવા ગરમ કરેલા તાંબા કે બીજી ધાતુના પતરા પરથી કે ખૂબ ગરમ વાતાવરણમાંથી ઝડપથી પસાર કરવાની પ્રક્રિયા, જેમાં માત્ર ટૂંકા તંતુઓ જ બળે અને દોરા અથવા કાપડને નુકસાન ન થાય. આ પ્રક્રિયા દોરા તથા કાપડ એમ બંને માટે વાપરવામાં આવે છે. આથી દોરા અથવા કાપડ પરના ટૂંકા તંતુઓ (protruding fibres) અને રૂંવાંપણું (fuzziness) દૂર થાય છે અને કાપડની સપાટી એકસરખી (uniform) બને છે. ત્યારબાદ સામાન્ય રીતે તેમને ભેજવાળી સપાટી પરથી અથવા પાણીમાંથી પસાર કરવામાં આવે છે. આમ કરવાથી ધૂંધવાવાની સ્થિતિ બંધ થાય અને આગ જેવા અકસ્માતથી બચી શકાય.
ટેન્ટરિંગ – ક્રૅબિંગ અને હીટસેટિંગ પ્રક્રિયાઓ : આ પ્રક્રિયાઓમાં વણાટવાળા કાપડના તાણા અને વાણાને ખેંચીને એકબીજાથી 90oના ખૂણે લાવવામાં આવે છે તેમજ કાપડનાં છેવટનાં પરિમાણો વ્યવસ્થિત કરવામાં આવે છે. ટેન્ટરિંગમાં ટેન્ટરફ્રેમ વડે કાપડનો પનો (વાણાઓને) ખેંચવામાં આવે છે. આ ટેન્ટરફ્રેમ સાંકળની બનેલી હોય છે, જેમાં ચાંપ (clips) અને ટાંકણી (pins) લગાડેલી હોય છે, જે કાપડની કિનારીને પકડી રાખે છે, તથા કાપડની સાથે તેના પાટા પર સરકે છે. કાપડ ગરમ કરેલ ઓરડામાંથી પસાર થાય છે, તેમ તેની પરના સળ અને કરચલીઓ (creases and wrinkles) દૂર થાય છે. કાપડ સપાટ બને છે. પ્રક્રિયાના અંતે તેના મૂળ પરિમાણ સાથે સુકાય છે. ભીના ઊની કાપડને આ પ્રક્રિયામાંથી પસાર કરવામાં આવે છે ત્યારે તે પ્રક્રિયા ક્રૅબિંગ અને માનવસર્જિત રેસાઓ માટે વાપરવામાં આવે ત્યારે તેને હીટસેટિંગ કહેવામાં આવે છે. હીટસેટિંગ કાયમી સળ પાડવા માટે અથવા અમુક પ્રકારની ખાસ કાયમી અસર ઉપજાવવા માટે પણ વાપરવામાં આવે છે. રાસાયણિક પદાર્થમાંથી બનાવેલ માનવસર્જિત રેસાઓ હીટસેટિંગ પ્રક્રિયા કરવાથી ભૌમિતિક પરિમાણ (dimensional stability) મેળવે છે અને યોગ્યતા મુજબના ગુણધર્મો કાયમી સ્થિતિમાં જાળવી શકે છે.
પ્રકાશિત ચળકાટ – વધુ સફેદાઈ માટેની પ્રક્રિયા (optical brightening) : પ્રતિદીપ્ત રંગવિહીન રંગ (ટીનોપલ-પ્રકારનો) વાપરી કાપડને વધુ ચળકાટ આપવાની પ્રક્રિયા. તે પારજાંબલી કિરણો(ultraviolet rays)ને વાદળી પ્રકાશમાં રૂપાંતરિત કરીને પરાવર્તિત કરે છે. આ પ્રકારની સફેદી રસાયણ પોતાની શક્તિ ધરાવે ત્યાં સુધી રહે છે; ત્યારબાદ નવી પ્રક્રિયા કરવામાં આવે છે. આ પ્રક્રિયા ઘરમાં વપરાતાં સફેદ વસ્ત્રો પર પણ ધોલાઈ વખતે કરી શકાય છે.
કૅલેન્ડરિંગ : ગરમ કરેલા સિલિન્ડર(rollers)ની વચ્ચેથી કાપડને દબાણ આપી પસાર કરવામાં આવે છે. પરિષ્કૃત કાપડ બનાવવા માટેની આ અંતિમ પ્રક્રિયા છે. એ દરમિયાન કાપડની સપાટી લીસી, ચળકાટવાળી અને સુંવાળી બને છે. ચળકાટ ગરમી અને દબાણ વધારવાની સાથે વધે છે. સુતરાઉ, લિનન, રેશમી અને માનવસર્જિત રેસામાંથી બનાવેલ કાપડને સુંવાળી અને લીસી સપાટીવાળું બનાવવા આ પ્રક્રિયાનો (પદ્ધતિનો) ઉપયોગ કરાય છે. સામાન્ય રીતે આ પ્રક્રિયા કાયમી સ્વરૂપની નથી.
સ્પર્શજન્ય ગુણ આપનાર પ્રક્રિયાઓ (finish enhancing tactile qualities) : આ પ્રકારની પ્રક્રિયાઓ માલની ગુણવત્તા પર થોડી અસર કરે છે. તેનાથી કાપડની કુમાશ (feel), અક્કડતા (drape) અને દેખાવમાં સુધારો થાય છે. આ ગુણ થોડા સમય પૂરતો જ કાપડમાં રહે છે જે ધોવાની સાથે જ અથવા થોડા સમયમાં દૂર થઈ જાય છે. આ પ્રક્રિયા કાયમી ગુણ આપનાર નથી, જેમાં સામાન્ય રીતે રસાયણો તરીકે કાંજી, સૉફનર અને વજન વધારનાર પદાર્થો વપરાય છે.
કાંજી (starch finish) : સ્ટાર્ચ, જિલેટીન, ગ્લ્યુ, કેસીન અને ક્લે જે દોરા અથવા તંતુઓ પર પાતળું પડ બનાવે છે, જેથી વણાયેલા કાપડનું કરકરાપણું (crispness), ચળકાટ તથા વજન વધે છે.
સુંવાળપવર્ધક (softening) પ્રક્રિયા : ડૅક્સટ્રીન ગ્લિસરીન, સ્લફોનેટેડ ઑઇલ, સ્લફેટેડ ટેલો અને સ્લફેટેડ આલ્કોહૉલ જેવા રાસાયણિક પદાર્થોનો ઉપયોગ આ પ્રક્રિયા માટે કરવામાં આવે છે. આથી કાપડમાં ભેજગ્રાહિતા, સુંવાળપ, ચળકાટ અને કુમાશ મેળવી શકાય છે.
વજન વધારનાર પ્રક્રિયા : સામાન્ય રીતે રેશમી કાપડની બનાવટમાં વજન વધારનાર ખનિજ પદાર્થો ઉમેરવામાં આવે છે. આથી કાપડની ઘટ્ટતા વધે છે. આ પ્રક્રિયા કાયમી નથી, પરંતુ થોડા વખત બાદ ફરી કરી શકાય છે. એને ગમિંગ પ્રક્રિયા તરીકે ઓળખવામાં આવે છે.
મિલિંગ અથવા ફેલ્ટિંગ : આ પ્રક્રિયાથી ઊની કાપડની ઘટ્ટતા અને જાડાઈ વધારવામાં આવે છે. આમાં ભેજ, દબાણ, ગરમી અને બે નળાકાર રોલરની વચ્ચેથી પસાર કરતાં મળતાં ઘર્ષણ અને દબાણથી ઘટ્ટતા વધે છે. દસથી પચીસ ટકા સુધી તાણા અને વાણામાં સંકોચન (shrinkage) આપવાથી કાપડની ઘટ્ટતા અને સુંવાળાપણું વધારે સારી રીતે ઉપસાવી શકાય છે.
કાપડની ગુણવત્તામાં વધારો કરનાર પરિષ્કરણ પ્રક્રિયાઓ (finishes improving performance) : કાપડની ગુણવત્તા એ આધુનિક બજાર માટે જરૂરી પ્રક્રિયા છે. નવા સંશોધન પ્રમાણે કાપડની સંકોચનશક્તિ રેઝિન, ફિનિશ અને ગરમીની પ્રક્રિયા વડે નિયંત્રિત કરી શકાય છે. માનવસર્જિત રેસાઓ સામે ટકી શકે તે માટે સુતરાઉ કાપડને પણ રેઝિન જેવા રાસાયણિક પદાર્થોની પ્રક્રિયા કરવાથી માનવસર્જિત રેસાને મળતા આવતા ગુણધર્મમાં મેળવી શકાય છે.
સંકોચન–નિયંત્રણ (shrinkage control) : આ પ્રક્રિયાઓમાં દબાણ-સંકોચન દ્વારા અથવા રેઝિન જેવાં રસાયણો વડે તથા હીટસેટિંગ(ગરમીની પ્રક્રિયા)થી સંકોચન નિયંત્રિત કરવામાં આવે છે.
દબાણથી (compressive) અથવા દબાણરહિત (relaxed) સ્થિતિમાં સંકોચન : આ પ્રક્રિયા સુતરાઉ તથા ચોક્કસ સૂતર મિશ્રિત કાપડની બનાવટ માટે વાપરવામાં આવે છે. કાપડના વણાટ તેમજ બીજી પ્રક્રિયાઓ દરમિયાન કાપડ પર થયેલા દબાણ અને ખેંચાણને લીધે તેની લંબાઈ તથા તાણાવાણામાં આવેલી વિકૃતિ (distortion) ઓછી કરી શકાય છે. આ પ્રક્રિયામાં કાપડને પાણી વડે ભીંજવી પાણીની વરાળથી ગરમ કરેલા નળાકાર (roll) અને છેડા વગરના રબરના અથવા જાડા ઊનના પટ્ટાની વચ્ચેથી પસાર કરીને કાયમી સ્થિતિમાં અને સંકોચન ઘટે તે રીતે ફેરવવામાં આવે છે. આ પ્રક્રિયા બાદ ઓછામાં ઓછી સંકોચનશક્તિ (residual shrinkage) કેટલી છે તે દરેક કાપડની સાથે ફરજિયાત દર્શાવવામાં આવે છે. આ પ્રક્રિયાથી દર ચોરસ સેમી.માં કાપડમાં રહેલા તાણા અને વાણાની સંખ્યા વધે છે. આથી કાપડનું ટકાઉપણું, ઘટ્ટતા, સુંવાળપ, ચળકાટ અને સંકોચનપ્રતિકારક શક્તિ જેવા ગુણધર્મો વધે છે.
રેયૉન અને રેયૉનમિશ્રિત કાપડ રેઝિન જેવા રાસાયણિક પદાર્થોની પ્રક્રિયા બાદ સંકોચનપ્રતિકારક શક્તિ પ્રાપ્ત કરે છે.
ઉષ્માની અસર થાય તેવા પૉલિયેસ્ટર અને નાયલૉન જેવા માનવસર્જિત રેસાઓને પરિષ્કૃત કરવાની પ્રક્રિયાઓ દરમિયાન હીટસેટિંગ કરી કાયમી સ્થિતિ(permanently stabilized)માં લાવવામાં આવે છે.
ઊની કાપડને ક્લોરિન પ્રક્રિયા તથા રેઝિન પ્રક્રિયા વડે સંકોચન-પ્રતિરોધક બનાવવામાં આવે છે.
દબાણથી કાયમી પરિષ્કૃતિ (durable press finishing) : આ પ્રક્રિયા તૈયાર પોશાક તથા કાપડ બંને પર કરી શકાય છે. આ પ્રક્રિયાથી કાપડના ગુણધર્મો જેવા કે આકાર જળવાઈ રહેવો, કાયમી સળ પડવા, સીવણના સળ તથા કરચલીઓ વગરનું કાપડ વગેરે મળી શકે છે. આથી કાપડ ઇસ્ત્રી વગર વાપરવાયોગ્ય બને છે. આવા પ્રકારનું કાપડ સલામત રીતે યંત્રથી ધોઈ અને સૂકવી શકાય છે. આ પ્રક્રિયામાં રેઝિન જેવાં રસાયણો વાપરી ઉપર મુજબના ગુણધર્મો મેળવી શકાય છે. આ માટે કાપડમાં ઇચ્છા અનુસાર પરિણામ મેળવવા માટે તેમાં વપરાયેલ તંતુની સંમિશ્રિત સ્થિતિ પ્રમાણે કાપડ પર પ્રક્રિયા કરવામાં આવે છે. કાપડને પ્રથમ રેઝિનના દ્રાવણમાં બોળી સૂકવી ઊંચા તાપમાને કાયમી કરવામાં આવે છે. તેને ક્યૉરિંગ કહે છે. બીજી રીતમાં કાપડને રેઝિનના દ્રાવણમાં બોળી સૂકવી, તેમાંથી કપડાં (garments) બનાવી દબાવી અને પછી ક્યૉરિંગ કરી કાયમી સ્થિતિમાં સળ રહે તે રીતે તૈયાર કરવામાં આવે છે.
ધુઓ અને પહેરો (wash and ware) : આ પ્રક્રિયા રેઝિન પરિષ્કરણ પ્રક્રિયા તરીકે પહેલાં જાણીતી હતી. તેમાં કાપડને રેઝિનના દ્રાવણમાં બોળી સૂકવી ક્યૉરિંગ (બેકિંગ) કરીને સુઘડ સ્થિતિમાં મેળવવામાં આવે છે. આ પ્રક્રિયાથી બનેલ કાપડનાં વસ્ત્ર યંત્ર અથવા ઘરેલુ ધોલાઈ બાદ પણ ઇસ્ત્રી વગર અથવા આછી ઇસ્ત્રી કરવાથી ઉપયોગમાં લઈ શકાય છે અને કાયમી સ્થિતિમાં જળવાઈ રહે છે.
ધૂળ–પ્રતિકારક પ્રક્રિયા (soil release) : આ પ્રકારની પરિષ્કરણ પ્રક્રિયાથી પૉલિયેસ્ટર અને પૉલિયેસ્ટર સુતરાઉ મિશ્રિત તથા ડ્યુરેબલ પ્રેસની પ્રક્રિયા કરેલા કાપડ પર પાણી, પરસેવા તથા તૈલી પદાર્થથી પડતા ડાઘ ઓછા પડે અથવા જલદીથી ધોઈ શકાય તે સ્થિતિ સર્જી શકાય છે. સામાન્ય ધોલાઈથી આ પ્રકારના ડાઘ નીકળી જઈ શકે છે.
સ્થિતવીજ–પ્રતિરોધક પ્રક્રિયા (antistatic finishes) : આ પ્રક્રિયા સામાન્ય રીતે માનવસર્જિત રેસાઓને આપવામાં આવે છે. આ રેસાઓનો ગુણધર્મ છે કે તેઓ તેમના વપરાશ દરમિયાન સ્થિતવીજ (static charge) ઉત્પન્ન કરે છે. આથી આ તંતુઓ અથવા રેસામાંથી બનાવેલ કાપડ વપરાશમાં સુગમ નથી. દોરા તેમજ કાપડના ઉત્પાદનમાં પણ સ્થિતવીજ ઉત્પન્ન થવાથી ક્ષતિ ઊભી થાય છે. આ પ્રક્રિયા માનવસર્જિત તંતુ પર કરવાથી, ઉત્પાદનમાં થતી ક્ષતિ દૂર થાય છે. કાયમી રીતે સ્થાયી રહે તેવાં સ્થિતવીજ-પ્રતિરોધક રસાયણોની પ્રક્રિયા કાપડ ઉપર કરવાથી કાપડ વપરાશ માટે સુગમ બને છે.
જીવાણુ–પ્રતિરોધક પ્રક્રિયા (antibacterial and antifungus finish) : આ પ્રકારની કાપડ પરિષ્કૃત કરવાની પ્રક્રિયા વડે પરસેવાથી તથા વપરાશથી ઉત્પન્ન થયેલ ગંધ તેમજ જીવાણુના પ્રતિરોધવાળું કાપડ બનાવી શકાય છે. આ પ્રક્રિયામાં સ્વાસ્થ્યને હાનિ ન કરે તેવા પરંતુ જીવાણુના પ્રતિરોધ માટે ઉપયોગી એવા રાસાયણિક પદાર્થ વાપરવામાં આવે છે.
ઊન અને રેશમી કાપડના વપરાશ તથા સંગ્રહ દરમિયાન જીવાણુ ઉત્પન્ન થાય છે, જે કાપડને નુકસાનકારક છે. વળી આ પ્રકારના કાપડને જંતુઓથી પણ સાચવવું પડે છે. આ પ્રકારના પ્રતિરોધ માટે રંગપ્રક્રિયા અથવા ઓપ આપવાની પ્રક્રિયા દરમિયાન ખાસ પ્રકારનાં રાસાયણિક સંયોજન વાપરવામાં આવે છે. આથી તેમાં જીવાણુ ઉત્પન્ન થતા નથી કે નાના જંતુ નુકસાન કરી શકતા નથી અને કાપડ લાંબા વખત સુધી ઉપયોગમાં લઈ શકાય છે.
પાણી–અવરોધક અને પાણી–પ્રતિરોધક પ્રક્રિયા (waterproofing and water-repellency) : પાણી-અવરોધક પરિષ્કરણની પ્રક્રિયા એ રેઇન કોટ અને છત્રીના કાપડ માટે કરવામાં આવે છે. આ પ્રક્રિયામાં કાપડનાં છિદ્રો પુરાઈ જાય તેવા રાસાયણિક પદાર્થ (જેવા કે અદ્રાવ્ય ધાતુનાં સંયોજનો, તૈલી પદાર્થો, મીણ, રબર લેટેક્સ વગેરે) ઉપયોગમાં લેવામાં આવે છે. આ રીતે તૈયાર કરેલું કાપડ પરિધાન માટે અનુકૂળ નથી.
પાણીપ્રતિરોધક પ્રક્રિયા દોરા અથવા તંતુની સપાટી પરની પ્રક્રિયા છે. આથી કાપડનાં છિદ્રો પુરાઈ જતાં નથી અને કાપડ પાણીપ્રતિરોધક બને છે. કાપડને પરિષ્કૃત કરવા માટે ઍલ્યુમિનિયમ ધાતુના ક્ષાર, સિલિકોન, ફ્લોરો સંયોજનો અને રેઝિન જેવાં રસાયણોનો ઉપયોગ થાય છે. આ પ્રક્રિયાથી બનતું કાપડ પરિધાન માટે અનુકૂળ હોય છે.
જ્વાળા–પ્રતિરોધક, આગ–પ્રતિરોધક અને આગ–અવરોધક પરિષ્કરણ પ્રક્રિયા (flameproof, fireproof and fire-resistant finishing) : જ્વાળા-પ્રતિરોધક કાપડ ઊંચા તાપમાન સામે અથવા જ્વાળામાં મૂકવામાં આવે તો તેનો પ્રતિકાર કરવાનો ગુણધર્મ ધરાવે છે. આ ગુણધર્મ કાપડ પર આપવામાં આવેલ જુદી જુદી પરિષ્કરણ પ્રક્રિયા પર આધારિત છે, જેને લીધે જ્વાળાથી કાપડમાં ઉત્પન્ન થતા ધુમાડાથી કાપડ સળગતું બંધ થઈ જાય છે. આવી પ્રક્રિયા કામચલાઉ અથવા કાયમી હોઈ શકે છે. કામચલાઉ પ્રક્રિયાવાળા કાપડને ધોવાથી તેને આપેલો ઓપ નીકળી જાય છે. બોરોનનાં સંયોજનો કામચલાઉ પ્રક્રિયા માટે ઉપયોગમાં લેવાય છે, જ્યારે કાયમી ઓપ માટે મોટાભાગે ફૉસ્ફરસનાં સંયોજનો વાપરવામાં આવે છે.
આગપ્રતિરોધક પ્રક્રિયામાં વપરાયેલ પરિષ્કરણ માટેનાં રસાયણોને લીધે કાપડ જ્યારે સળગે ત્યારે આગને મળતો ઑક્સિજન બંધ થઈ જાય છે. આથી આગ બુઝાઈ જાય છે. તેને આગપ્રતિરોધક પરિષ્કૃત કાપડ પર ફેલાતી રોકે છે. નાનાં બાળકો માટેના પોશાક, રસોડામાં વપરાતા તથા વિમાનના પડદા, બેઠકો અને આગરક્ષક દળ(fire brigade)માં વપરાતા પોશાક પર આ પ્રકારની પરિષ્કૃત પ્રક્રિયા કરવામાં આવે છે.
7. રંગાટીકામ ને છાપકામ
રંગવા અને છાપવાની પ્રક્રિયાઓ : કાપડને રંગવાથી તેનો દેખાવ વધુ આકર્ષક બને છે. રંગવાની પ્રક્રિયાને (1) રંગકામ અને (2) છાપકામ એમ બે પ્રક્રિયામાં વિભાજિત કરી શકાય છે.
રંગાટીકામ (dyeing) : આ પ્રક્રિયા કાપડ-બનાવટમાં વપરાતા તંતુઓ, દોરા તથા સફેદ તૈયાર કાપડ પર કરી શકાય છે. સારી જાતના ઊની કાપડ માટે તેના તંતુઓને રંગવામાં આવે છે. કાપડ પર રંગ ચડાવવાથી બજારની માગ મુજબના રંગ વાપરી માલ બજારમાં વેચવા માટે મૂકી શકાય છે અને વધુ પડતા માલભરાવાની પરિસ્થિતિમાંથી મુક્ત રહી શકાય છે.
રંગકામમાં વાપરવામાં આવતા રંગ તંતુઓના પ્રકાર અને તેમની વિશિષ્ટ જરૂરિયાત તથા પ્રક્રિયા-ખર્ચ અને રંગની ક્ષમતા પર આધાર રાખે છે. સામાન્ય રીતે રંગની ક્ષમતા માટે પ્રકાશ-પ્રતિરોધકતા (light fastness), ધોવાણ-પ્રતિરોધકતા (washing fastness), ઘર્ષણ-પ્રતિરોધકતા (rubbing fastness) વગેરે પર ભાર મૂકવામાં આવે છે. રંગકામ માટે તંતુઓ, દોરા અથવા કાપડને ઉપર વર્ણવ્યા મુજબ તૈયાર કરવાં જરૂરી છે.
રંગના પ્રકાર : કાર્બનિક રસાયણમાં થયેલા સંશોધનના આધારે બજારમાં વિશાળ પ્રમાણમાં સંશ્લેષિત રંગ ઉપલબ્ધ બન્યા છે. તંતુ માટે રંગ અને તેની પદ્ધતિ સામાન્ય સંજોગોમાં (પૃ. 385 ઉપરના) સારણી 1માં દર્શાવ્યા પ્રમાણે અનુસરવામાં આવે છે. પ્રતિકૂળ સંજોગોમાં રંગપ્રક્રિયા પ્રમાણે યોગ્ય યંત્ર અને પ્રક્રિયા ઉપયોગમાં લેવામાં આવે છે.
સામાન્ય રીતે ઊન, રેશમ અને નાયલૉન માટે ઍસિડ રંગ તથા સૂતરના તંતુઓ માટે આકર્ષણ ધરાવતા મૂળ (direct) રંગ, ક્રિયાશીલ વૅટ, ઍઝોઇક વગેરે રંગ વાપરવામાં આવે છે. તંતુઓને મૉરડન્ટ રંગથી રંગવા માટે તેની પ્રક્રિયા દરમિયાન કેટલાંક રસાયણ ઉમેરીને તેનું તંતુ પ્રત્યેનું આકર્ષણ વધારવામાં આવે છે, જેથી રંગકામ પૂર્ણ બને છે. ધાતુક્ષારની પ્રક્રિયા કરવાથી રંગની ક્ષમતામાં વધારો થાય છે.
સલ્ફર રંગ સૂતર માટે વાપરવામાં આવે છે. તે સોંઘા છે પણ ઘેરા અને ચળકાટ વગરના હોય છે. સલ્ફર રંગથી રંગેલા કાપડના લાંબા વપરાશ અને સંગ્રહ વખતે રંગમાંથી ઉત્પન્ન થતા તેજાબથી સૂતરની મજબૂતાઈ ઘટી જાય છે. ઍઝોઇક રંગ એ અદ્રાવ્ય રંગકણો છે, જે તંતુઓ પર રાસાયણિક સંયોજનથી બનાવવામાં આવે છે. આ માટે નૅપ્થૉલને કૉસ્ટિક સોડાના પાણીમાં દ્રાવ્ય સ્વરૂપે કાપડ પર ચડાવીને ડાઇઍઝોટાઇઝ્ડ રસાયણના દ્રાવ્ય સંયોજન સાથે પ્રક્રિયા કરવાથી તંતુ પર અદ્રાવ્ય સ્વરૂપના રંગકણ બને છે, જે તંતુને રંગ આપે છે. ડાયઍઝો પ્રક્રિયા શૂન્યથી 5o સે. તાપમાને કરવામાં આવતી હોવાથી આ પ્રકારના રંગને બરફના રંગ (ice colour) તરીકે ઓળખવામાં આવે છે. આ રંગ ખાસ કરીને સૂતરના તંતુ માટે જ વાપરવામાં આવે છે.
વૅટ રંગ : એ ઘણા પ્રાચીન સમયથી જાણીતા છે. પ્રાથમિક રંગ તરીકે ગળી(indigo)નો ઉપયોગ કરવામાં આવતો હતો. ગળી મૂળ તો ભારતની પેદાશ હતી. ગળી ઉપર લાકડાના મોટા વાસણમાં અપચયન પ્રક્રિયા વડે રંગને દ્રાવ્ય સ્થિતિમાં લાવવાની પ્રક્રિયા કરવામાં આવતી હતી. આથી આ પ્રકારના રંગ વૅટ રંગ તરીકે જાણીતા થયા અને આ પ્રકારના બીજા સંશ્લેષિત રંગ પણ વૅટ રંગ તરીકે ઓળખાયા. વૅટ રંગ પાણીમાં અદ્રાવ્ય હોવાથી તંતુઓને રંગવા માટે પ્રથમ કૉસ્ટિક સોડા અને સોડિયમ હાઇડ્રૉસલ્ફાઇટ વડે અપચયન કરી રંગને દ્રાવ્ય સ્થિતિમાં લાવી તંતુઓ પર રંગપ્રક્રિયા કર્યા બાદ ઉપચયન વડે ફરી વાર મૂળ અદ્રાવ્ય સ્વરૂપમાં ફેરવવામાં આવે છે. આ પ્રકારના રંગ ઘણા પ્રકારની ક્ષમતા ધરાવે છે.
ક્રિયાશીલ રંગો (reactive dyes) : આને સંયોજિત રંગ તરીકે પણ વર્ણવી શકાય છે. આ પ્રકારના રંગ તંતુઓ સાથે સંયોજાઈને તંતુઓને રંગ આપે છે તથા ઉચ્ચ કોટિનો ટકાઉ ગુણ ધરાવે છે. 1950ના દાયકાના મધ્ય ભાગમાં સૂતર માટે આ પ્રકારના રંગ બજારમાં અસ્તિત્વમાં આવ્યા. આજે ઘણા પ્રકારના તંતુઓ માટે આ પ્રકારના રંગ ઉપલબ્ધ છે. સૂતર માટેના રંગ આર્થિક રીતે અને પ્રક્રિયાની પદ્ધતિ મુજબ વધુ અનુકૂળ હોવાથી, થોડા સમયમાં બહોળા વપરાશમાં આવ્યા છે.
પૉલિયેસ્ટર, નાયલૉન અને સૅલ્યુલોઝ એસિટેટ જેવા જલ-પ્રતિકારક (hydrophobic) પ્રકારના તંતુઓ માટે સંશ્લેષિત રંગ(organic pigments)માંના ડિસ્પર્સ રંગ વાપરવામાં આવે છે. આ રંગ પાણીમાં અદ્રાવ્ય હોય છે. પરંતુ રંગકણની પરિમાણકતા(size)થી મળતી તારક સ્થિતિને કારણે પાણીમાં દ્રાવ્ય સ્વરૂપમાં રહે છે. આ માટે ‘ડિસ્પર્સિંગ એજન્ટ’નો ઉપયોગ કરવામાં આવે છે.
પ્રક્રિયાપદ્ધતિ : રંગના દ્રાવણથી તંતુ પર રંગપ્રક્રિયા કરવામાં આવે છે. સામાન્ય રીતે પાણી દ્રાવક તરીકે વાપરવામાં આવે છે. રંગના દ્રાવણને ‘ડાય લિકર’ અને ભરવામાં આવેલ પાત્રને ‘ડાય બાથ’ કહે છે. રંગપ્રક્રિયામાં રંગના કણ તંતુની સપાટીમાં ભેગા થઈને મોટા સ્વરૂપે જકડાઈ રહે છે. રંગપ્રક્રિયાની પૂર્ણતા માટે રંગ સહેલાઈથી ધોવાઈ ન જવો જોઈએ અથવા પાણીમાં બોળવાથી નીકળી જવો ન જોઈએ. રંગ માટે પ્રકાશ-પ્રતિરોધકતાનો ગુણધર્મ જરૂરી છે.
એમ માનવામાં આવે છે કે નીચે પ્રમાણેના ચાર પ્રકારના બંધ (bond) વડે રંગકણો તંતુઓ સાથે બંધાયેલા રહે છે અને જરૂરી કાર્યક્ષમતા મેળવે છે :
(1) હાઇડ્રોજન બંધ, (2) વાન્ડર-વૉલ બંધ, (3) આયોનિક બંધ, (4) સહ-સંયોજક બંધ.
ઊન, રેશમ અને માનવસર્જિત તંતુઓની રંગપ્રક્રિયામાં હાઇડ્રોજન બંધ એઝો (Azo); ઍમિનો (Amino); આલ્કાઇલ ઍમિનો (Alkyl amino); ઍમિડો (-CO-NH) વગેરે સમૂહો વચ્ચે અસ્તિત્વ ધરાવે છે. વાન્ડર-વૉલ બંધ એટલે બે પદાર્થના પરમાણુઓ અથવા અણુઓના ખેંચાણના કારણે અસ્તિત્વમાં આવતા બંધ. આ પ્રકારનું આકર્ષણ સૂતર અને પ્રત્યક્ષ રંગ વચ્ચે અસ્તિત્વ ધરાવે છે એમ માનવામાં આવે છે. આયોનિક બંધ ઊન અને રંગકણ વચ્ચે અસ્તિત્વ ધરાવે છે. ઊનમાં પ્રોટીન હોય છે, જે જુદા જુદા 20 આલ્કા ઍમિનો ઍસિડનું બનેલ છે. ઊનની રંગપ્રક્રિયામાં સલ્ફ્યુરિક ઍસિડ વાપરવામાં આવે છે, જે પ્રોટીનના ઍમિનો સમૂહ સાથે અને રંગકણ સાથે આયોનિક બંધ બનાવવામાં ઉપયોગી બને છે. આ પ્રકારના બંધ સૂતર અને રિઍક્ટિવ રંગની વચ્ચે અસ્તિત્વ ધરાવે છે. તંતુઓ ને રંગ વચ્ચે ડાય બાથમાં થતી પ્રક્રિયા રાસાયણિક છે. રંગકણના રાસાયણિક સમૂહ અને સૂતરના હાઇડ્રૉક્સી સમૂહ વચ્ચે આલ્કલીની હાજરીમાં આ બંધ અસ્તિત્વમાં આવે છે. તેથી રિઍક્ટિવ પ્રકારના રંગ વડે સૂતરને રંગી શકાય છે.
સારણી 1 : તંતુઓ માટે સામાન્ય રીતે વપરાતા રંગ અને તેની પદ્ધતિઓ
તંતુના પ્રકાર | રંગના પ્રકાર | રંગકામ માટે વપરાતાં સ્વરૂપ | રંગકામ માટે વપરાતી પદ્ધતિ | |||||||
1 | 2 | 3 | 4 | |||||||
ડાઇંગ | તંતુ | દોરા | કાપડ | પૅડિંગ | જીગર | કેટલ | જેટ | ઑટો ક્લેવ- બીમ | કન્ટિ-ન્યુઅસ
રેન્જ |
|
કુદરતી તંતુઓ પ્રાણીજન્ય ઊન |
ઍસિડ, બેઝિક, મૉરડન્ટ ? રિઍ-ક્ટિવ (સોલ્યુબિલા-ઇઝ્ડ વૅટ) ? | √ | √ | √ | √ | L | ||||
સંમિશ્રિત ઊન (ઊન અને સૂતર) ઊન અને વિસ્કોસ રેશમ |
ઍસિડ, ડાયરેક્ટ, મૉરડન્ટ રિઍક્ટિવ ઍસિડ, બેઝિક, ડાયરેક્ટ, મૉરડન્ટ, (રિઍક્ટિવ સોલ્યુબિલાઇઝ્ડ વૅટ) |
√ | √
√ |
√
√ |
||||||
વનસ્પતિજન્ય સૂતર (કૉટન) |
ઍઝોઇક, બેઝિક, ડાયરેક્ટ, મૉરડન્ટ, વૅટ, રિઍક્ટિવ, સલ્ફર, પિગમેન્ટ, સોલ્યુબિલાઇઝ્ડ વૅટ |
√ | √ | √ | √ | √ | √ | √ | √ | √ |
બાસ્ટ (લિનન, ફ્લૅક્સ, હૅમ્પ, જ્યૂટ, રેમી) |
ઍસિડ, ડાયરેક્ટ, રિઍક્ટિવ, વૅટ, સોલ્યુબિલાઇઝ્ડ વૅટ, (ડિસ્પર્સ) ? |
√ | √ | √ | √ | |||||
માનવસર્જિત રેસા વિસ્કોસ |
ડાયરેક્ટ, મૉરડન્ટ, પિગમેન્ટ, રિઍક્ટિવ, સલ્ફર, વૅટ, સૉલ્યુબિલાઇઝ્ડ વૅટ |
√D | √ | √ | √ | √ | √ | √ | √ | √ |
સેકન્ડરી એસિટેટ |
ડિસ્પર્સ | √D | √ | √ | A | √ | √ | |||
ટ્રાય એસિટેટ | ડિસ્પર્સ | √D | √ | √ | A | √ | √ | |||
પૉલિઍમાઇડ (નાયલૉન, પરલોન, રેસિલીન) |
ઍસિડ, ડિસ્પર્સ, મૉરડન્ટ, પિગમેન્ટ |
√D | √ | √ | √ | √ | √ | √ | √ | |
પૉલિયેસ્ટર | ડિસ્પર્સ, પિગમેન્ટ | √D | √ | √ | √ | √ | √ | √ | √T | |
પૉલિઍક્રિલો-નાઇટ્રાઇલ (ઓરલોન, ઍક્રિલોન, કેશ્મિલોન) |
બેઝિક, ડિસ્પર્સ, પિગમેન્ટ |
√D | √ | √ | √ | √ | √ | √ | ||
પૉલિવાઇનલ ક્લોરાઇડ (એનવિલોન, થરમૉબાઇલ) |
બેઝિક, ડિસ્પર્સ | |||||||||
પૉલિ ઑલિફિન્સ ઇલેસ્ટૉમર્સ (Glospan, Lyeraete) |
ડિસ્પર્સ ઍસિડ ડિસ્પર્સ રિઍક્ટિવ વૅટ (વૂલ) |
D | √ | √ | √ | |||||
D = Dop dyeing, A = Tensionless condition, L = Low temp., T = Thermosol dyeing process. |
રંગક્રિયામાં ગરમી આપવી જરૂરી છે. આ ગરમી અથવા ઊર્જાથી દ્રાવણમાંના તંતુઓના કદમાં તત્કાળ પૂરતો વધારો શક્ય બને છે, જેથી દ્રાવ્ય રંગકણ દ્રાવણમાંથી ખેંચાઈને સહેલાઈથી તંતુ પર સ્થિત થાય છે. આ ફેરબદલીને પારિભાષિક રીતે ‘એક્ઝોશન’ તરીકે ઓળખવામાં આવે છે.
તંતુ, દોરા કે કાપડ માટે, પછી તે કુદરતી રેસા હોય કે માનવસર્જિત હોય, સપ્રમાણ રંગપ્રક્રિયા એ અગત્યનો અને પાયાનો ગુણધર્મ છે. આ માટે પદાર્થ અને રંગનાં દ્રાવણ એકબીજાના ગાઢ અને સતત સંપર્કમાં રહે તે જરૂરી છે. પ્રક્રિયાની ભૌતિક અને રાસાયણિક સ્થિતિ (જેવી કે પૂરતાં રસાયણ, ઉદ્દીપકની સ્થિતિ, પ્રક્રિયાક્રમ વગેરે) નિયંત્રિત કરવી જરૂરી બને છે.
આધુનિક મત અનુસાર પાણી દ્વારા રંગપ્રક્રિયા કરવામાં પર્યાવરણ દૂષિત થાય છે. તેને અટકાવવા માટે કાર્બનિક પ્રવાહી વડે પ્રક્રિયા કરવાનું શરૂ કરવામાં આવેલ. તેના કેટલાક ફાયદા છે, જેવા કે, (1) પ્રદૂષણ ઘટાડી શકાય છે, (2) પ્રક્રિયાની ઝડપ વધે છે, (3) શક્તિસંચય થાય છે, (4) પ્રક્રિયાની કિંમતમાં ઘટાડો શક્ય બને છે, પરંતુ વ્યવહારમાં આ પદ્ધતિ ઉપયોગમાં લઈ શકાતી નથી. થોડાક પ્રમાણમાં તેનો ઉપયોગ થાય છે.
રંગરેજ (dyer) તંતુઓના પ્રકાર, સંમિશ્રણ અને રંગપ્રક્રિયાની પદ્ધતિના આધારે રંગની પસંદગી કરે છે. દરેક રંગમાં યોગ્ય રંગમિશ્રણ પણ વાપરવામાં આવે છે. સામાન્ય રીતે રંગનું નિત્યતા(fastness)નું ધોરણ જેમ ઊંચું તેમ પ્રક્રિયા-ખર્ચ વધારે આવે છે. આ માટે રંગ તથા પ્રક્રિયા જરૂરી રંગની નિત્યતા સાથે યોગ્ય પ્રમાણમાં નક્કી કરવામાં આવે છે.
રંગની નિત્યતા-ચકાસણી(fastness test)ની રીત અને ધોરણ નીચે દર્શાવેલ સંસ્થા દ્વારા સંયુક્ત રીતે અથવા અલગ અલગ રીતે નક્કી કરવામાં આવે છે : અમેરિકન ઍસોસિયેશન ઑવ્ ટેક્ષ્ટાઇલ કેમિસ્ટ્સ અને કલરિસ્ટ્સ (AATCC), યુરોપીય કૉન્ટિનેન્ટલ ઇથેટ્સ કન્વેન્શન (ECE), સોસાયટી ઑવ્ ડાયર્સ અને કલરિસ્ટ્સ (SDS); ઇન્ટરનેશનલ ઑર્ગેનાઇઝેશન ફૉર સ્ટાન્ડર્ડ્ઝ (ISO). ભારત સરકારે પણ આઈ.એસ.ઓ. તથા બીજી સંસ્થાઓનાં અનુભવ અને સૂચનો પર આધારિત ઇન્ડિયન બ્યૂરો ઑવ્ સ્ટાન્ડર્ડ્ઝ (IBS) નામની સંસ્થા દ્વારા યોગ્ય પદ્ધતિઓ અને ધોરણો નક્કી કરેલાં છે.
પ્રકાશ-પ્રતિરોધકતા આઠ અંક સુધી માપવામાં આવે છે. એક અંક નબળી પ્રતિરોધકતા દર્શાવે છે. આઠ અંક ઉચ્ચ પ્રતિરોધકતા દર્શાવે છે. વિરંજિત (bleaching) દ્રાવણ, ઍસિડ, આલ્કલી, સાબુ અથવા પ્રક્ષાલકોનાં દ્રાવણ અને પરસેવા સામેની પ્રતિરોધકતા પાંચ અંક સુધી માપવામાં આવે છે.
રંગ સામાન્ય રીતે સંમિશ્રિત સ્થિતિમાં વાપરવામાં આવે છે, જેથી રંગની યોગ્ય ઝાંય (hue) મળે અને બજારની માગ સંતોષી શકાય. કાપડ એક જ પ્રકારના તંતુઓનું બનેલ હોય તો રંગનું મિશ્રણ એક જ પ્રકારના રંગમાંથી નક્કી કરવામાં આવે છે. કાપડ એક કરતાં વધારે મિશ્ર તંતુમાંથી બનેલ હોય તો તે રંગપ્રક્રિયાના જુદા જુદા ગુણધર્મ ધરાવે છે. તેથી રંગપ્રક્રિયા માટે જુદા જુદા પ્રકારનાં રંગમિશ્રણ અને પદ્ધતિનું સંયોજન ઉપયોગમાં લેવામાં આવે છે.
રંગપ્રક્રિયા માટે તંતુઓનાં સ્વરૂપો : તાંતણા સ્વરૂપે ઊન અથવા રૂના તંતુઓ જથ્થામાં અવ્યવસ્થિત રીતે ગોઠવાયેલા હોય છે. આ જ સ્થિતિમાં ગોઠવાયેલા માનવસર્જિત તંતુ માટે ‘ટો’ શબ્દ વપરાય છે. પૂણી વ્યવસ્થિત રીતે ગોઠવાયેલા તંતુઓનો સમૂહ છે અને કાંતણપ્રક્રિયા માટે યોગ્ય રૂપ ધરાવે છે. 30.48 સેમી. વ્યાસવાળા પોચા દડા અથવા આંટીના સ્વરૂપે તેને રંગપ્રક્રિયા માટે વાપરવામાં આવે છે.
દોરાને આંટી અથવા પૅકેજના સ્વરૂપે રંગવા માટે ઉપયોગમાં લેવામાં આવે છે. આકાર પ્રમાણે તેને કોન, ચીઝ, કેક, બીમ વગેરે નામથી ઓળખવામાં આવે છે. ગૂંથેલું કાપડ સામાન્ય રીતે નળાકાર સ્વરૂપે અને વણાયેલું કાપડ સપાટ કાપડ તરીકે પ્રક્રિયા માટે વાપરવામાં આવે છે. પ્રક્રિયા દરમિયાન વણાયેલું કાપડ દોરડા સ્વરૂપે અથવા ખુલ્લા સપાટ કાપડ તરીકે પણ વાપરી શકાય છે.
રંગપ્રક્રિયા માટેનાં યંત્ર : રંગપ્રક્રિયા માટેની આધુનિક યંત્રસામગ્રી ઍસિડ-પ્રતિકારક સ્ટીલમાંથી બનાવવામાં આવે છે. સામાન્ય રીતે 4 % Mo ધાતુનું સંયોજન ધરાવતું સ્ટીલ આ ગુણધર્મ ધરાવે છે. રંગપ્રક્રિયા માટેનું યંત્ર રંગનું દ્રાવણ ભરવા માટેનું પાત્ર, કાપડ અને રંગનું દ્રાવણ પસાર કરવા તથા દ્રાવણને ગરમ કે ઠંડું કરવાની વ્યવસ્થા અને રંગ અને કાપડ એકબીજાના સંપર્કમાં રહે તેવી વ્યવસ્થા વગેરે જેવી સગવડ ધરાવતું હોય તે જરૂરી છે. તંતુના પ્રકાર પ્રમાણે રંગ કરવા માટેનાં યંત્ર વાપરવામાં આવે છે. મજૂરી અને ઊર્જાની કિંમત રંગપ્રક્રિયાની કુલ કિંમતના પ્રમાણમાં વધારે આવે છે. રંગરેજનો હેતુ પ્રક્રિયાનો સમય ટૂંકાવી ઓછી ઊર્જા (વરાળ અને વીજશક્તિ) વાપરી, માલના ઓછા બગાડ સાથે ઉચ્ચતમ ગુણવત્તાવાળી પ્રક્રિયા કરવાનો હોય છે.
લૂઝ સ્ટોક : તંતુ સ્વરૂપને રંગવા માટે શંકુ આકારનું યંત્ર વધારે પ્રમાણમાં વાપરવામાં આવે છે. તંતુઓને પાત્રની અંદર મૂકીને રંગનું દ્રાવણ યાંત્રિક પંપ દ્વારા પસાર કરવામાં આવે છે. તંતુઓ ઉપરના ભાગે દબાઈને એકસરખા રંગના દ્રાવણનો ફેલાવો કરવામાં મદદરૂપ થાય છે. આ પ્રકારના રંગકામમાં એકસરખી રંગપ્રક્રિયા થવી તે અતિ મહત્વનું નથી, કારણ કે રંગકામ પછી તેને મિશ્રિત કરીને દોરાના સ્વરૂપમાં ફેરવવામાં આવે છે, જ્યાં રંગનું એકસરખાપણું ઊપસી આવે છે.
દોરાના રંગકામ માટે હ્યુસંગ યંત્ર ઘણા સમયથી જાણીતું છે. લંબચોરસ ટાંકીમાં રંગનું દ્રાવણ ભરવામાં આવે છે. વાંસ અથવા બીજી યોગ્ય વસ્તુના ચોકઠા (frame) ઉપર વીંટાળેલી આંટીઓ ગોઠવીને તેમાં બોળવામાં આવે છે. તેના તળિયાના ભાગે છિદ્રોવાળી રચના હોય છે, જેથી દ્રાવણ વરાળના ઉપયોગથી ગરમ કરી શકાય છે. પંપ દ્વારા દ્રાવણને ફેરવવામાં આવે છે. પહેલાંના સમયનાં યંત્રોમાં અસમાન ગરમી ને દ્રાવણના સંપર્કના કારણે આંટી પર અસમાન રંગ લાગતો હતો. આધુનિક યંત્રમાં ખામીરહિત માલ ઉત્પન્ન કરી શકાય છે.
પૅકેજ ડાઇંગ મશીનમાં દોરાને યોગ્ય આકાર અને ઘનતાવાળા પૅકેજ સ્વરૂપમાં યંત્રમાં રાખેલ વ્યવસ્થા મુજબ ગોઠવવામાં આવે છે. પંપ દ્વારા રંગનું દ્રાવણ યંત્રમાં ફેરવવામાં આવે છે. પૅકેજના મધ્ય ભાગમાંની ત્રાકમાંથી પૅકેજમાં થઈ રંગનું દ્રાવણ બહાર આવે છે, જેને અંદરથી બહાર (in-to-out) વ્યવસ્થા કહે છે. તેની વિરુદ્ધ દિશામાં પૅકેજની બહારની બાજુથી પૅકેજમાં દાખલ થઈ કાણાવાળી ત્રાકમાંથી પસાર થાય છે, જેને બહારથી અંદર (out-to-in) વ્યવસ્થા કહે છે. યોગ્ય સમય મુજબ બન્ને રીતે રંગના દ્રાવણને ફેરવવામાં આવે છે, જેથી સમગ્ર પૅકેજને એકસરખું રંગવાની પાયાની જરૂરિયાત પૂર્ણ થાય છે. પાણીમાં અદ્રાવ્ય રંગકણનું અસ્તિત્વ હિતાવહ નથી. ડિસ્પર્સ રંગ દ્રાવણમાં દ્રાવ્ય રૂપ કરતાં અદ્રાવ્ય રૂપમાં રહે છે અને પૉલિયેસ્ટરના દોરાને રંગે છે. તેના માટે પણ મોટા એકત્રિત થયેલા કણનું અસ્તિત્વ હિતાવહ નથી, કારણ કે તે પૅકેજની અંદર કે બહારની સપાટી પર ચોંટીને દોરામાં રંગનાં ધાબાં ઉત્પન્ન કરે છે. પૉલિયેસ્ટરને રંગવા માટે પૅકેજ ડાઇંગ મશીનમાં ભારે દબાણની વરાળથી 130o સે. સુધીનું તાપમાન મેળવવામાં આવે છે.
વિંચ (winch) યંત્ર એ કાપડના રંગકામ માટેનું જૂનામાં જૂનું યંત્ર છે. તેનું નામ તેમાં મૂકવામાં આવેલ લાકડાની પાતળી પટ્ટીઓવાળા રોલર પરથી પાડવામાં આવ્યું છે. આ રોલર પૂરા પનાના છેડા વગરના ગોળાકાર સ્વરૂપના કાપડને દ્રાવણમાં એકથી બીજા છેડા સુધી ફેરવવામાં મદદરૂપ બને છે. આ યંત્રમાં તળિયાના ભાગેથી વરાળ પસાર કરી દ્રાવણ ગરમ કરવાની વ્યવસ્થા હોય છે. જેટ ડાઇંગ મશીન, વિંચ યંત્રના સિદ્ધાંત પર તૈયાર થયેલ છે. આ યંત્ર બંધ નળાકાર આકારનું હોય છે. તેમાં કાપડ અને રંગનું દ્રાવણ ભરવામાં આવે છે. જરૂરી ઊંચું દબાણ અને તાપમાન મેળવી શકાય છે. આ યંત્રમાં કાપડ અને દ્રાવણ એકબીજાના ગાઢ સંપર્કમાં રહે તે માટે બેમાંથી એક અથવા બન્ને સામસામી દિશામાં ફેરવી શકાય તેવી વ્યવસ્થા પણ હોય છે. આ યંત્ર પૉલિયેસ્ટર કે બીજા માનવસર્જિત રેસા માટે અથવા સંમિશ્રિત કાપડ માટે વાપરવામાં આવે છે.
જીગર ડાઇંગ મશીન અંગ્રેજી ‘V’ આકારનું હોય છે. તેમાં તળિયાના ભાગમાં રંગનું દ્રાવણ ભરવામાં આવે છે. તેને ગરમ કરવા માટે વરાળનો ઉપયોગ થાય છે. તેમાં બે નળાકાર રોલ આવેલા હોય છે, જેનાથી કાપડ યોગ્ય દિશામાં, બહારના ભાગમાં આવેલ લૅચિંગ રોલ પર વીંટાઈ શકે છે. બે લૅચિંગ રોલ પર કાપડ વારાફરતી ફેરવવામાં આવે છે અને કાપડને નક્કી સમય અને ઝડપ પ્રમાણે દ્રાવણમાંથી પસાર કરી યોગ્ય પ્રક્રિયા પૂર્ણ કરી શકાય છે. આધુનિક યંત્ર કાર્યક્રમ પ્રમાણે સ્વયંનિયંત્રિત કાર્ય કરે છે. આ યંત્રનો ઉપયોગ બીજી પ્રક્રિયાઓ માટે પણ કરી શકાય છે. પ્રક્રિયા મુજબ તેમાં દ્રાવણ ભરવામાં આવે છે.
પૅડિંગ મશીન રંગકામની સતત અથવા અર્ધસતત પ્રક્રિયા માટે અગત્યનું છે. બે, ત્રણ અથવા ચાર રોલ પાસે પાસે યોગ્ય રીતે ગોઠવેલા હોય છે અને કાપડ તેમાંથી પસાર કરવામાં આવે છે. સામાન્ય રીતે બે અથવા ત્રણ રોલવાળું યંત્ર વધુ ઉપયોગમાં લેવામાં આવે છે. યંત્રના આગળના ભાગમાં દ્રાવણ ભરવા માટેની ને તેમાંથી કાપડ પસાર કરવાની વ્યવસ્થા હોય છે. રોલ ઉપર યાંત્રિક રીતે અથવા હવા વડે યોગ્ય દબાણ આપી શકાય છે, જેથી દ્રાવણ કાપડમાં પૂરતા પ્રમાણમાં ઊતરી શકે છે. રંગને ઉપસાવવા અને કાયમી કરવા માટે કાપડને તેની સાથે જોડેલા કે જુદા જુદા યંત્રમાંથી પસાર કરતાં, પ્રક્રિયા અનુસાર રંગ કાયમી બને છે.
છાપકામ (printing) : છાપકામ એ કાપડને રંગ વડે મનપસંદ ભાત (pattern) પ્રમાણે શણગારવાની પ્રક્રિયા છે. છાપકામનો ઉદભવ પ્રાચીન કાળની ચિત્રકામની કળામાંથી થયો છે. ઈ. પૂ. ચોથી સદીમાં ભારતમાં બીબાં વડે છાપકામ થતું હતું. ઇજિપ્તમાં ખોદકામ કરતાં ત્રીજી સદીના છાપકામ વિશેના પુરાવાઓ મળ્યા છે. કાપડના છાપકામની પ્રક્રિયામાં કલાકાર (છાપનાર કસબી) અને ચિત્રકાર(designer)ની ઊંચી બુદ્ધિમત્તા વડે ઉચ્ચ ગુણવત્તા પ્રાપ્ત કરવામાં આવી છે.
છાપકામની પ્રક્રિયા (1) બીબાં (block), (2) સ્ક્રીન (screen) છપાઈ (3) રોલર છાપકામ અને (4) ઉષ્મા-વિનિમય (heat transfer) — એમ ચાર પદ્ધતિથી થઈ શકે છે.
સામાન્ય રીતે દરેક પદ્ધતિમાં છાપકામ કરવા માટે રંગની ઘટ્ટ લાહી (paste) વડે રંગ કાપડ પર લગાડી, વરાળ વડે અથવા ગરમીથી તેને કાયમી કરીને વધારાના રંગને દૂર કરવા માટે ધોવાની પ્રક્રિયા કરવામાં આવે છે. બીજા સ્વરૂપે જોઈએ તો છાપકામ એટલે કાપડ પર નિશ્ચિત જગ્યાએ સ્થાયી સ્વરૂપમાં રંગની ભાત ઉપસાવવાની પ્રક્રિયા. તે કાપડ પર સીધું છાપકામ કરવાની પ્રક્રિયા (direct printing), ભાત પ્રમાણે રંગ ઉડાડવાની પ્રક્રિયા (discharge printing) અને ભાત પ્રમાણે રંગ અવરોધવાની પ્રક્રિયા (resist printing) – એમ ત્રણ પ્રકારે જાણીતી છે. સીધા છાપકામ પ્રકારમાં રંગ સીધો જ કાપડ પર લગાડવામાં આવે છે. ડિસ્ચાર્જ પ્રકારમાં રંગેલા કાપડ પર રંગ માટેના અપચયિત પદાર્થ અથવા યોગ્ય રસાયણયુક્ત લાહી વાપરી છાપકામવાળા ભાગમાંથી રંગ વિભાજિત કરીને ‘વ્હાઇટ ડિસ્ચાર્જ પ્રક્રિયા’ વડે સફેદી મેળવવામાં આવે છે. જો આ પ્રકારની લાહીમાં નૉન-ડિસ્ચાર્જેબલ પ્રકારના રંગ વાપરવામાં આવે તો કલર ડિસ્ચાર્જની અસર મેળવી શકાય છે. ‘રેઝિસ્ટ સ્ટાઇલ’માં યોગ્ય રાસાયણિક બંધારણવાળી લાહીથી છાપકામ કરવામાં આવે છે. ત્યારબાદ તેના પર રંગપ્રક્રિયા કરવામાં આવે છે, જેથી છાપેલા ભાગ ઉપર રંગ લાગતો નથી અને સફેદ અથવા યોગ્ય પ્રકારની લાહી સાથે મિશ્રણ કરેલ રંગ મેળવી શકાય છે.
બીબા છાપકામ (block printing) : આ પદ્ધતિ છાપકામ માટેની શરૂઆતની પદ્ધતિ છે. લાકડાના ટુકડામાં કોતરણી કરીને જરૂરી ભાત ઉપસાવવામાં આવે છે. આ પ્રકારના બીબામાં ખાલી જગ્યા અથવા ખાડાવાળી જગ્યાએ ભાતમાં રંગ વગરની જગ્યા ઉપસાવે છે. ઘણી વાર પાતળી તાંબાની ચીપ વડે પણ આકૃતિઓ ઉપસાવીને બીબું તૈયાર કરવામાં આવે છે. રંગવાળી લાહીનો ઉપયોગ છાપકામમાં કરવામાં આવે છે. મેજને ઘણા જાડા કાપડ અથવા ઊનના ફેલ્ટ, રેક્ઝિન અથવા રબરના પડ વડે મઢીને છાપકામ માટે જરૂરી કુમાશ તૈયાર કરવામાં આવે છે. આ સ્તર પર કાપડને ગુંદર અથવા ટાંકણીઓ વડે ચોંટાડવામાં આવે છે.
બીબાને રંગમાં બોળીને કાપડ પર વ્યવસ્થિત ગોઠવી વજન આપીને અથવા હળવા હાથે ઠોકીને રંગને કાપડ પર પ્રસરાવવામાં આવે છે. જેટલા રંગ ઉપસાવવાના હોય તેટલાં બીબાં વાપરવામાં આવે છે. આ પદ્ધતિ ઘણી મજૂરી અને આવડત માગે છે. આ પદ્ધતિ ખર્ચાળ છે અને ઓછી ઉત્પાદકતા આપે છે. ઘણાં ઐતિહાસિક સુંદર ચિત્રો આ પ્રકારે જ તૈયાર કરવામાં આવેલ છે.
સૌપ્રથમ રોલર પ્રિન્ટિંગ મશીન ઈ. સ. 1783માં અસ્તિત્વમાં આવેલ. યંત્રની રચનામાં લોખંડના એક નળાકાર ફરતે, છેડા વગરનો રબરનો પટ્ટો (blanket) લગાડેલો હોય છે. આ પટ્ટા અને છાપકામ માટેના કાપડની વચ્ચે એક જાડું કાપડ (back grey) પસાર કરવામાં આવેલ હોય છે. તેનું કાર્ય છાપકામ દરમિયાન વપરાયેલા વધારાના રંગને ચૂસી લેવાનું હોય છે. છાપકામ માટે ચોકસાઈપૂર્વક કોતરેલી ભાતવાળા, ક્રોમિયમનો ઢોળ ચડાવેલા તાંબાના નળાકારનો ઉપયોગ કરવામાં આવે છે. કોતરણીવાળા નળાકારની સાથે બે પટ્ટીઓ ગોઠવવામાં આવે છે. એકને ડૉક્ટર બ્લેડ કહે છે, જે તીક્ષ્ણ ધારવાળી હોય છે અને વધારાની રંગયુક્ત લાહીને નળાકાર પરથી પાછી ધકેલવાનું કાર્ય કરે છે. બીજી પટ્ટી કે જે લિંટ બ્લેડ(lint blade) તરીકે ઓળખાય છે તે રોલર પર ચોંટેલા કાપડના દોરા અથવા રુવાંટીને દૂર કરવાનું કાર્ય કરે છે. આધુનિક યંત્રમાં રંગના પાત્રમાં બ્રશ લગાડવામાં આવે છે, જેથી યોગ્ય પ્રમાણમાં રંગ ધાતુના ભાતવાળા નળાકાર પર લાગે છે. છપાયેલા કાપડને સૂકવવા માટે અને રંગને કાયમી કરવા માટેનાં જરૂરી યંત્ર પણ જોડવામાં આવે છે. આ પદ્ધતિમાં છાપકામની ગુણવત્તા તેમાં વપરાયેલ રંગની લાહીની ઘટ્ટતા, ભાતની કોતરણી અને તેની ઊંડાઈ, કાપડની શોષકઊર્જા (absorbency), ભાતવાળા નળાકાર અને કાપડના સંપર્ક અને દબાણ પર આધારિત હોય છે. આ રીતે કાપડની એક બાજુ પર છાપકામ કરવામાં આવે છે. ઘણાં યંત્રમાં જરૂરી ફેરફાર વડે કાપડની બંને બાજુ છાપી શકાય તેવી વ્યવસ્થા કરવામાં આવે છે. આ રીતે એક જ પ્રકારની ભાતવાળું વધારે લંબાઈનું કાપડ છાપી શકાય છે. આધુનિક યંત્રમાં વીજળીથી ચાલતી મોટર, હવા કે પાણી દ્વારા સંચાલિત દબાણ આપવાની પદ્ધતિ (pneumatic or hydraulic pressure devices) અને બીજી યાંત્રિક રચનાઓનો સમાવેશ કરવામાં આવે છે.
છાપા (stencils) પર રંગ છાંટીને કોતરેલી આકૃતિ ઉપસાવવામાં આવે છે. તે ઘણા મર્યાદિત પ્રમાણમાં ભારતમાં પ્રસંગોપાત્ત, ઉપયોગમાં લેવામાં આવે છે.
સ્ક્રીન પ્રિન્ટિંગ (screen printing) : સ્ક્રીન પ્રિન્ટિંગ હાથ વડે અથવા યંત્રની મદદથી કરી શકાય છે. કાપડને મેજ પર અથવા યંત્રના અંદરના ભાગમાં ગુંદર અથવા ટાંકણીઓ વડે ચોંટાડવામાં આવે છે, ને તેની ઉપર છાપકામ કરવામાં આવે છે. રેશમ અથવા નાયલૉનની જાળીવાળા કાપડને ધાતુ કે લાકડાની યોગ્ય આકારની ફ્રેમમાં ખેંચીને, જડીને સ્ક્રીન તૈયાર કરવામાં આવે છે. સ્ક્રીનના કાપડ ઉપર ભાતને હાથથી રંગીને અથવા યંત્રની મદદથી યોગ્ય પ્રકારનો ફોટો-સેન્સિટિવ લૅકર (photo sensitive lacquer) વાપરી ઉપસાવવામાં આવે છે. સ્ક્રીન ઉપર ભાત ઉપસાવવાની પદ્ધતિ ફોટોગ્રાફિક પદ્ધતિને અનુરૂપ હોય છે.
છાપકામ કરવા માટે સ્ક્રીન કાપડ ઉપર મૂકી તેમાં રંગની લાહી રેડીને રબરની સ્ક્વીઝ (squeeze) વડે રંગને પ્રસરાવી બીજી બાજુ ખેંચવાથી કાપડ પર ભાત ઊપસી આવે છે. એક રંગ વડે વારંવાર પ્રક્રિયા કરવાથી જરૂરી લંબાઈનું કાપડ છાપીને તૈયાર કરી શકાય છે. બીજા રંગ માટે આકૃતિ અને ભાતને અનુરૂપ યોગ્ય ગોઠવણી પ્રમાણે કાપડ પર છાપકામ કરવામાં આવે છે અને મનગમતા રંગોમાં ભાત ઉપસાવવામાં આવે છે. સ્ક્રીન પ્રિન્ટિંગના વધુ ઉપયોગ સાથે તેને યંત્રવિદ્યા વડે ઝડપી અને ઊંચી ગુણવત્તાવાળી છાપકામની પદ્ધતિ તરીકે વિકસાવવામાં આવી છે, પરંતુ પાયાના સિદ્ધાંતો ઉપર વર્ણવ્યા પ્રમાણે જ છે. ફ્લૅટબેડ પ્રિન્ટિંગ મશીન, રોટરી સ્ક્રીન પ્રિન્ટિંગ મશીન વગેરે આધુનિક યંત્રો ઉપયોગમાં લેવાય છે.
ફ્લૅટબેડમાં ખુલ્લા સપાટ સ્ક્રીન વપરાય છે. રોટરી સ્ક્રીન પ્રિન્ટિંગમાં ગોળ નળાકાર પ્રકારના સ્ક્રીન વાપરવામાં આવે છે. તે છિદ્રોવાળા નિકલ ધાતુના બનેલા હોય છે. તેની ઉપર સાદા કાપડના સ્ક્રીનની જેમ જ ભાત ઉપસાવવામાં આવે છે. આ પ્રકારના સ્ક્રીનમાં લાહી તેની અંદરના ભાગમાં રેડવામાં આવે છે અને તેમાં જ ધાતુના સળિયારૂપ અથવા પાતળી પટ્ટીરૂપ સ્ક્વીઝ યોગ્ય રીતે વાપરવામાં આવે છે, જેથી સ્ક્રીન ગોળ ફરે ત્યારે લાહી બહાર નીકળે છે અને કાપડ પર રંગીન ભાત ઊપસી આવે છે.
ઉષ્મા વિનિમય છાપકામ (heat transfer printing) : ગરમી વડે રંગની ફેરબદલીથી થતું છાપકામ. માનવસર્જિત કાપડની લોકપ્રિયતાને કારણે આ નવા પ્રકારની પદ્ધતિનો વિકાસ થયો છે. ઊર્ધ્વપાતી રંગ (sublime colours) વડે ખાસ પ્રકારના (wax coated) કાગળ પર ભાત છાપવામાં આવે છે. આ પ્રકારના ભાતવાળા કાગળ અને કાપડને ઉપરાઉપરી ગોઠવી ગરમ કરેલા રોલમાંથી પસાર કરવામાં આવે છે. રોલની ગરમી અને તેના દબાણથી કાગળ પરના ઊર્ધ્વપાતી રંગ કાપડ પર લાગે છે. આમ, કાગળ પરની ભાત કાપડ પર છપાય છે. આ પદ્ધતિને આધારે અર્ધરંગ છાંય (half-tone effect) પ્રકારની અસર કાપડ પર મેળવવામાં આવે છે.
બધા જ પ્રકારના કાપડના છાપકામ માટે કાપડની ગુણવત્તા અને ખાસ રંગયુક્ત લાહીની ઘટ્ટતા મહત્ત્વનાં છે. લાહીની બનાવટમાં વાપરવામાં આવતો ગુંદર, રંગ અને રંગને અનુરૂપ જરૂરી રસાયણો યોગ્ય પ્રકારના ગુણધર્મ ધરાવતાં હોય તે જરૂરી છે. સામાન્ય રીતે મેંદો, ગમ, ટ્રેગાકાન્થ, સોડિયમ આલ્જિનેટ, ગુવાર ગમ, મિથાઇલ સૅલ્યુલોઝ ઈથર અને સોડિયમ કાર્બૉક્સી મિથાઇલ સૅલ્યુલોઝ (CMC) વગેરે લાહી બનાવવા માટે ગુંદર તરીકે વાપરવામાં આવે છે. ડાયરેક્ટ, વૅટ, ક્રિયાશીલ, ડિસ્પર્સ તથા પિગમેન્ટ રંગકો છાપકામ માટે વાપરી શકાય છે. ગરમી અથવા પાણીની વરાળ વડે (steaming) પ્રક્રિયા કરવાથી રંગને કાયમી કરી શકાય છે. છાપકામની અને કાયમી કરવાની પ્રક્રિયાઓ કાપડના જથ્થામાં અથવા સતત સ્વરૂપે કરી શકાય છે. રંગને કાયમી કર્યા બાદ કાપડને ધોઈને છાપકામમાં વપરાયેલ ગુંદર અને વધારાના રંગને દૂર કરવામાં આવે છે.
ઊની કાપડને સામાન્ય રીતે ક્લોરિન વડે પ્રક્રિયા કર્યા બાદ છાપકામ માટે ઉપયોગમાં લેવામાં આવે છે. ઊનના ટૉપ (tops) પટ્ટી રૂપે રંગીને મિશ્રિત અસર ઉપસાવવામાં આવે છે. ઊનના તાંતણાને રંગીને ઝાંયની અસર ઉપસાવવામાં આવે છે.
8. કાપડની વપરાશ (textile consumption)
કાપડનો મુખ્ય ઉપયોગ વસ્ત્રપરિધાન તથા સામાન્ય સજાવટમાં થાય છે. કુલ ઉત્પાદનનો ઘણો મોટો ભાગ ઉપર દર્શાવેલ હેતુઓ માટે વપરાય છે.
આધુનિક શોધોના કારણે કાપડમાં ઘણા ફેરફારો થયા છે. જેમ કે ઊનના ઊંચી જાતના તથા ભરાવદાર ગૂંથેલા કાપડને બદલે હલકા અને કુદરતી રેસા તથા માનવસર્જિત રેસાઓમાંથી તેમજ બંનેના મિશ્રણમાંથી વણાટ કરી બનાવેલ કાપડનો ઉપયોગ વસ્ત્રોમાં થાય છે. સ્થિતિસ્થાપક (elastomeric) રેસાઓની શોધથી તૈયાર પોશાકના ઉદ્યોગમાં પાયાના ફેરફાર સાથે ઝડપી પ્રગતિ સધાઈ છે. ખેંચાઈ શકે તેવા દોરા(stretch yarn)માંથી બનાવેલ કાપડ શરીરને ચુસ્ત રહે છે તેમજ પહેરવામાં ઘણું જ અનુકૂળ હોય છે.
આંતરિક આધાર સાથેનું કાપડ (interlining) : શરૂઆતમાં તૈયાર પોશાક બનાવવા માટે, આંતરિક આધાર તરીકે કાપડ માટે ઘોડાના વાળનો ઉપયોગ થતો હતો. થોડાક સમય પછી તેની જગ્યાએ ઘેટાં-બકરાંના વાળનો ઉપયોગ થવા લાગ્યો અને પછી રાસાયણિક પ્રક્રિયા કરી બનાવેલ વિસ્કોઝ (viscose rayon) વપરાતું હતું. હાલમાં ધોઈ શકાય તેવા કૃત્રિમ રેસાઓમાંથી બનાવેલ કાપડ વપરાય છે. પોશાકની ગુણવત્તાનો આધાર તે માટે સીવવામાં ઉપયોગમાં લીધેલ દોરાની ગુણવત્તા પર રહે છે.
વસ્ત્ર માટેની જરૂરી સંભાળ તેમાં વપરાયેલ રેસાઓ તથા તેના પર કરવામાં આવેલ રાસાયણિક પ્રક્રિયાઓ – એમ બંને પર ઘણો જ આધાર રાખે છે. ઈ. સ. 1972ની સાલમાં યુનાઇટેડ સ્ટેટ ફેડરલ ટ્રેડ કમિશન (United State Federal Trade Commission) દ્વારા સૌપ્રથમ નિયમ ઘડવામાં આવ્યો કે કાપડ પર તેની કાયમી વપરાશ માટે નિર્દેશિત સૂચનાઓ લગાવવી, જેનો ઉપયોગ નિકાસી માલ તથા ઊંચી ગુણવત્તાઓ ધરાવતાં વસ્ત્રો માટે પણ કરવામાં આવે છે.
ગૃહવપરાશ માટેનું કાપડ (household textiles) : જે કાપડનો ગૃહવપરાશમાં વારંવાર ઉપયોગ થાય છે, તેની ઘરવપરાશ માટેના નરમ કાપડ તરીકે ગણના થાય છે. આ નરમ કાપડ સામાન્ય રીતે સ્નાનગૃહમાં ટુવાલ તરીકે, રસોઈઘરમાં ભીનાં વાસણોને સૂકાં કરવા, સૂવાના ઓરડામાં ઓશીકાં-રજાઈ-કામળા તથા પાથરણાંના આવરણમાં, પડદાઓ તથા ઘરના ફર્નિચરની સજાવટમાં ઉપયોગમાં લેવાય છે. આ કાપડ ઘરવપરાશ ઉપરાંત ધર્મશાળા, મનોરંજન માટેનાં સ્થળો પર, ઉપાહારગૃહોમાં, દુકાનોમાં, કાર્યાલયોમાં, જાહેરાતો માટે ધંધા-રોજગારનાં સ્થળો પર તથા સુશોભન માટેનાં સાધનોમાં વપરાય છે.
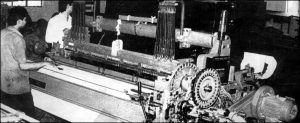
અદ્યતન હાથસાળ કાપડ-ઉદ્યોગ
ઔદ્યોગિક કાપડ (industrial fabric) : આ કાપડને નીચે પ્રમાણે ત્રણ ભાગમાં વહેંચી શકાય :
1. પ્રક્રિયાનિર્મિત કાપડની બનાવટમાં (composition products)
2. પ્રક્રિયામાં વાપરવા માટેનું કાપડ (processing fabrics)
3. સીધી વપરાશ માટેનું કાપડ (direct use fabric)
(1) પ્રક્રિયાનિર્મિત કાપડની બનાવટમાં : આ પ્રકારના કાપડને રબર, પ્લાસ્ટિક જેવા પદાર્થના સંયોજિત મિશ્રણના પ્રવાહીનો થર (coating) કરીને કે તેમાં બોળીને અથવા તો પ્રવાહીનો છંટકાવ કરીને ટકાઉ બનાવવામાં આવે છે. આ પ્રકારના કાપડનો ઉપયોગ પૈડાં (tyres), પટ્ટાઓ (belts), નળીઓ (tubes) તથા હવાથી ફુલાવી શકાય તેવી (inflatable) વસ્તુઓ, ટાઇપરાઇટરની પટ્ટી, ઇલેક્ટ્રિક કેબલ, ટેલિફોનના વાયર વગેરેની બનાવટમાં થાય છે.
(2) પ્રક્રિયામાં વાપરવા માટેનું કાપડ : ઔદ્યોગિક પ્રક્રિયા જેવી કે ગાળણ (filter), સ્ક્રીનિંગ (bolting & screening) છાપકામ દરમિયાન વપરાતા બૅક ગ્રે (back grey) વગેરે માટે વપરાય છે.
(3) સીધી વપરાશ માટેનું કાપડ : તાડપત્રી, તંબૂ, છત્રીનું કાપડ, કૅન્વાસ, પગરખાં, થેલા વગેરેની બનાવટમાં વપરાતું કાપડ આ પ્રકારનું હોય છે.
સંરક્ષણાત્મક કાપડ (fabric for protective coating) : સૈન્યના ઉપયોગ માટેનું કાપડ વિવિધ પરિસ્થિતિમાંથી પસાર થઈ શકે તેવું હોવું જરૂરી છે. ઠંડા અને ગરમ વાતાવરણ સામે, પાણી અને આગ સામે, જીવાણુઓ સામે ટકી શકે તેવું હોવું જરૂરી છે. આ જાતનું કાપડ પટ્ટા, પટ્ટી અને દોરડાના રૂપમાં, તંબૂ માટે, હવાઈ છત્રીના, જાકીટ વગેરેની બનાવટમાં ઉપયોગી છે. હવાઈ છત્રીનું કાપડ નક્કી કરેલ ધોરણ પ્રમાણેનું અને નિયમ મુજબની છિદ્રતાવાળું હોવું જોઈએ. અવકાશી સફર માટે નવા પ્રકારનું કાપડ બનાવવામાં આવે છે.
સારણી 2 : ભારત : કાપડ–ઉત્પાદન (લાખ ચો. મીટરમાં)
ક્ષેત્ર | 1950-51 | 1970-71 | 1990-91 | 1999-2000 | |
(1) | સુતરાઉ કાપડ (ક) મિલો (ખ) વિકેન્દ્રિત ક્ષેત્ર |
34,010 (81) 8,140 (19) |
40,550 (53) 34,570 (47) |
19,780 (15) 1,14,210 (85) |
11,050 (6) 1,78,840 (94) |
કુલ | 42,150 (100) | 76,020 (100) | 1,33,990 (100) | 1,89,890 (100) | |
(2) | મિશ્ર કાપડ | ||||
(ક) મિલો | NA | 1,070 (63) | 7,380 (35) | 3,790 (7) | |
(ખ) વિકેન્દ્રિત ક્ષેત્ર | NA | 630 (37) | 13,800 (65) | 55,340 (93) | |
કુલ | 1,700 (100) | 21,180 (100) | 59,130 (100) | ||
(3) | માનવસર્જિત રેસા (ક) મિલો (ખ) વિકેન્દ્રિત ક્ષેત્ર |
130 (4) 2,870 (96) |
20 (0.02) 9,490 (99.8) |
40 (0.01) 48,330 (99.9) |
2,300 (2) 1,34,950 (98) |
કુલ | 3,000 (100) | 9,510 (100) | 48,370 (100) | 1,37,250 (100) | |
કુલ ઉત્પાદન | 45,150 | 87,230 | 2,03,540 | 3,86,270 |
પર્યાપ્ત : ભારતીય આર્થિક સર્વેક્ષણ : 2002-03 નોંધ : કૌંસમાં ટકાવારી દર્શાવેલ છે.
આધુનિક જીવનપદ્ધતિમાં બધા જ સ્તરે કાપડનો ઉપયોગ અનિવાર્ય છે. આમ છતાં, કાગળ અને પ્લાસ્ટિકના ઉપયોગથી ઘણી જગ્યાએ કાપડના વપરાશ માટેની શક્યતા ઘટી છે. હાલના સંજોગો પ્રમાણે કાપડ અને પ્લાસ્ટિકના ઉપયોગની ચોક્કસ મર્યાદાઓ છે, જે સંશોધન દ્વારા દૂર થઈ શકે એમ છે. આથી, કાપડ-ઉદ્યોગકારોએ કાપડ-ઉદ્યોગ જાળવી રાખવા માટે અને વપરાશ વધારવા માટે સંશોધનને પ્રોત્સાહન આપવું જરૂરી બને છે.
ભારતનો કાપડ-ઉદ્યોગ આશરે 3,000થી પણ વધુ વર્ષો પુરાણો છે. ભારતનું કાપડ ખાસ કરીને મલમલ યુરોપ, આરબ દેશો, પૂર્વ આફ્રિકા, દૂર પૂર્વના દેશો, ચીન વગેરેમાં ખૂબ પ્રચલિત રહ્યું હતું. યુરોપની ઔદ્યોગિક ક્રાંતિને અનુસરીને અંગ્રેજોએ પોતાના કાપડ-ઉદ્યોગને ઉત્તેજન આપવા માટે ભારતના ઉદ્યોગ પર ક્રમશ: નિયંત્રણો મૂકી તેની અવગતિ માટે પૂરતા પ્રયત્નો કર્યા, જેને પરિણામે દેશનો કાપડ-ઉદ્યોગ ત્યારે મુશ્કેલીમાં મુકાઈ ગયો. તેમ છતાં પણ સ્વદેશપ્રેમી ઉદ્યોગ-સાહસિકોએ પોતાની મિલોની સ્થાપના કરી સ્થાનિક કાપડનું ઉત્પાદન જાળવી રાખ્યું હતું. 1931-32 દરમિયાન ભારતમાં 77.50 લાખ મીટર કાપડની આયાત ઉદ્યોગનું વાસ્તવિક ચિત્ર રજૂ કરે છે. બીજા વિશ્વયુદ્ધ દરમિયાન કાપડની, ખાસ કરીને લશ્કરી માગમાં ગણનાપાત્ર વૃદ્ધિએ ભારતની મિલોને ઉત્પાદન વધારવાનું પ્રોત્સાહન પૂરું પાડ્યું હતું. તેમાં સ્વતંત્ર ભારતની સરકારે ઉત્તેજન આપી વધારો કર્યો હતો.
1950-51માં ભારતમાં સંગઠિત ક્ષેત્રે 107 કાંતણ તથા 276 સંયુક્ત મિલો અસ્તિત્વમાં હતી. વળી વિકેન્દ્રિત ક્ષેત્રમાં યંત્રસાળો અને હાથસાળો પણ હતી. તે વર્ષમાં કાપડનું ઉત્પાદન સંગઠિત ક્ષેત્રના 34,140 લાખ ચોરસ મીટર અને વિકેન્દ્રિત ક્ષેત્રના 11,010 લાખ ચોરસ મીટર મળીને કુલ 45,150 લાખ ચોરસ મીટર થયું હતું. તેમાં સંગઠિત ક્ષેત્રનો ફાળો આશરે 70 ટકા જેટલો હતો. ભારત તાર તથા કાપડની નિર્યાત કરતો અગ્રણી દેશ ગણાતો હતો. 1971માં ઇંગ્લૅન્ડે જકાતમુક્ત આયાતનીતિ રદ કરતાં ભારતનો ઉદ્યોગ મુશ્કેલીમાં મુકાયો હતો. વિકસિત દેશો સાથે સ્પર્ધા માટે આવશ્યક ગુણવત્તા અને કિફાયત કિંમતવાળું કાપડ બનાવવા માટે જૂનીપુરાણી યંત્રસામગ્રી અક્ષમ નીવડી હતી. તેમાં કાચા માલની અછત, બળતણ-ખર્ચમાં વૃદ્ધિ, વિવિધ સ્તરે જકાતવેરા, નીચી ઉત્પાદકતા વગેરેએ મુશ્કેલીઓમાં વધારો કર્યો હતો. સરકારે યંત્રસાળ અને હાથસાળ ક્ષેત્રોને પ્રોત્સાહન આપવાની અને સંગઠિત મિલોને વિકેન્દ્રિત ક્ષેત્રો માટે તારનું ઉત્પાદન અનામત રાખવાની નીતિ અપનાવી હતી. વળી જનતા માટે 45 ટકા જાડા તેમજ મધ્યમ કાપડનું ઉત્પાદન અનામત રાખી તેના પર ભાવનિયંત્રણ લાદવામાં આવ્યું હતું. માનવસર્જિત રેસાના કાપડે સ્પર્ધામાં વૃદ્ધિ કરી હતી. જેને પરિણામે સંગઠિત ક્ષેત્રની મિલો અર્થક્ષમતા ગુમાવી બેઠી હતી. ઉદ્યોગપતિઓ આ સંજોગોમાં મિલોના આધુનિકીકરણ પ્રત્યે નિરુત્સાહી રહ્યા હતા. તેમાં મજૂર મહાજનોએ કામદારોની છટણી થવાના અંદેશાથી વિરોધ કર્યો હતો, જેના પરિણામરૂપ ગુજરાતમાં 63, મહારાષ્ટ્રમાં 16 અને મધ્યપ્રદેશમાં 10 મિલો સહિત સંગઠિત ક્ષેત્રમાં કુલ 126 સંયુક્ત મિલો બંધ પડી હતી. તેવી જ રીતે તામિલનાડુમાં 81, આંધ્રપ્રદેશમાં 35, ઉત્તરપ્રદેશમાં 30 અને ગુજરાતની 28 સહિત સંગઠિત ક્ષેત્રમાં કુલ 295 કાંતણમિલો બંધ થઈ હતી. 1985માં નિમાયેલ રાષ્ટ્રીય કાપડ નિગમે 125 મિલોનો વહીવટ સંભાળ્યો હતો. તેમાં આશરે રૂ. 1,000 કરોડનો ખર્ચ કરી અંશત: આધુનિકીકરણ તેમજ પુનર્ગઠન કરવા છતાં મિલોની કામગીરી નબળી રહી હતી. નિગમે આશરે રૂ. 99 કરોડની ખોટ બતાવી હતી. સરકાર મિલોની જમીન-મિલકતો વેચીને કેટલીક મિલોને પુન: સજીવન કરવાની વિચારણા કરી રહી છે; તેમ છતાં વિકેન્દ્રિત ક્ષેત્રના ઉત્પાદને ગણનાપાત્ર વૃદ્ધિ કરી હતી. 1991માં કેન્દ્ર સરકારે લાદેલાં નિયંત્રણો દૂર થતાં કાપડ-ઉદ્યોગને પ્રોત્સાહન મળ્યું હતું. ઉત્પાદનમાં ગણનાપાત્ર વૃદ્ધિ મેળવાઈ હતી તે સારણી 2માં બતાવી છે.
સારણી 2 દર્શાવે છે કે 1950-51માં ભારતનું કાપડનું કુલ ઉત્પાદન 45,150 લાખ ચોરસ મીટર હતું.
1999-2000માં તે વધીને 3,86,270 લાખ ચોરસ મીટર (આશરે 8.5 ગણું) થયું હતું. 1951માં સંગઠિત ક્ષેત્રનો સુતરાઉ કાપડના ઉત્પાદનમાં 81 ટકા હિસ્સો અને વિકેન્દ્રિત ક્ષેત્રનો 19 ટકા હતો. 1999-2000માં સંગઠિત ક્ષેત્રનો હિસ્સો 5 ટકા અને વિકેન્દ્રિત ક્ષેત્રનો 95 ટકા હતો. 1951માં મિશ્ર કાપડનું ઉત્પાદન નહિવત્ હતું; જ્યારે 1999-2000માં તે 59,130 લાખ મીટરે પહોંચ્યું હતું. જ્યારે માનવસર્જિત રેસાના કાપડનું ઉત્પાદન 1,37,250 લાખ ચો. મીટર હતું. 1999-2000માં કાપડના કુલ ઉત્પાદનમાં સુતરાઉ કાપડનો હિસ્સો 49 ટકા અને મિશ્ર તેમજ માનવસર્જિત રેસાના કાપડનો 51 ટકા હતો. માનવસર્જિત રેસાના કાપડની પસંદગી તેનું ટકાઉપણું તેમજ ધોલાઈ અને ઇસ્ત્રી કરવાની સરળતાને આભારી છે.
1960-61ની ભારતની રૂ. 73 કરોડની નિર્યાત સામે 1999-2000માં રૂ. 44,178 કરોડની નિકાસ કરી હતી. તે જ સમયગાળા દરમિયાન સૂતરના તારની નિર્યાત રૂ. 65 કરોડથી વધીને રૂ. 13,388 કરોડે પહોંચી હતી. 2002-03માં તેની નિકાસ રૂ. 16,217 કરોડ હતી.
ભારતમાં કપાસનું વિપુલ પ્રમાણમાં ઉત્પાદન થાય છે. તેનો કાંતણ-ઉદ્યોગ પણ ઠીક ઠીક વિકાસ પામેલો છે, તેથી ભારતમાં તારનું ઉત્પાદન વિકેન્દ્રિત ક્ષેત્રોને કાચો માલ પૂરો પાડવા માટે તેમજ નિકાસ માટે કરવામાં આવે છે. ભારતના કાંતણ-ઉદ્યોગનું ઉત્પાદન નીચેની સારણી 3માં આપ્યું છે.
સારણી 3 : કાપડ–ઉદ્યોગ – તારનું ઉત્પાદન (લાખ કિલોગ્રામમાં)
કપાસ(રૂ)ના તાર (cottonyarn) |
સંમિશ્રિત તાર (mixed/ Blended yarn) |
100 % માનવ-સર્જિત તાર |
કુલ |
|
1950-51 | 5,330 | N.A. | 110 | 5,440 |
1990-91 | 15,100 | 2,070 | 1,070 | 18,240 |
1999-2000 | 22,040 | 6,120 | 2,210 | 30,370 |
1950-51માં ભારતનો કાપડનો માથાદીઠ વપરાશ 14.4 મીટર સુતરાઉ અને 1.2 મીટર મિશ્ર કાપડ મળીને કુલ 15 મીટર હતો. 2001-02માં 14.8 મીટર સુતરાઉ કાપડ અને 17.2 મીટર મિશ્ર તેમજ માનવસર્જિત કાપડ મળીને કુલ 32 મીટર વપરાશ અંદાજવામાં આવ્યો છે.
વિશ્વ-વ્યાપાર સંગઠને (World Trade Organisation) નક્કી કર્યા પ્રમાણે 1 જાન્યુઆરી, 2005થી મુક્ત વ્યાપારપ્રક્રિયા અમલમાં મુકાઈ છે. વિશ્વના દેશો તેમનાં કુદરતી પરિબળો, ઉત્પાદનક્ષમતા તેમજ કૌશલ્યનો ઉપયોગ કરી નિર્યાતમાં વૃદ્ધિ કરવા સક્ષમ બને. ભારત પાસે વિપુલ પ્રમાણમાં કપાસનું ઉત્પાદન તેમજ સસ્તી મજૂરી ઉપલબ્ધ છે. તેનો લાભ લઈ તે વિશ્વબજારમાં અગ્રણી સ્થાન પ્રાપ્ત કરે તેવી શક્યતાઓને અવગણી શકાય તેમ નથી. તે સિદ્ધ કરવા માટે નીચેની નબળાઈઓ દૂર કરવી આવશ્યક છે.
(1) ભારતમાં હેક્ટરદીઠ કપાસનું ઉત્પાદન 328 કિલોગ્રામ છે, જ્યારે ઑસ્ટ્રેલિયાનું 1,585, ચીનનું 884, અમેરિકાનું 792 અને પાકિસ્તાનનું 513 કિલોગ્રામ અંદાજવામાં આવે છે. વળી ભારતનો કપાસ અશુદ્ધ અને અસમાન હોય છે. નિકાસમાં વૃદ્ધિ મેળવવા કપાસની ગુણવત્તામાં સુધારો તેમજ ઉત્પાદનમાં વૃદ્ધિ આવશ્યક છે. (2) ઉત્પાદન માટે આવશ્યક બળતણો જેવાં કે વીજળી, કોલસો, ગૅસ વગેરે બીજા દેશોની સરખામણીમાં મોંઘાં છે. વળી પુરવઠો પણ અનિયમિત મળે છે. તેમાં સુધારો કરવાની જરૂરિયાત છે. (3) ઉદ્યોગ પર વિવિધ સ્તરે જકાતો અને સરકારી નિયંત્રણો વહીવટમાં મુશ્કેલીઓ ઊભી કરે છે. તેને માટે લાંબા ગાળાની સરળ પદ્ધતિ દાખલ કરવી આવશ્યક છે. (4) જૂની ઘસાઈ ગયેલી યંત્રસામગ્રીને સ્થાને આધુનિક સ્વયંસંચાલિત યંત્રસામગ્રી તેમજ કામદારોનું પુનર્ગઠન ઉદ્યોગને અર્થક્ષમ બનાવવા માટે જરૂરી છે. ઉત્પાદનવૃદ્ધિ કરી કિફાયત કિંમતે માલ વેચવાની સ્પર્ધાત્મક ક્ષમતા જ નિર્યાતમાં વૃદ્ધિ કરી આપશે. (5) ભારતમાં કાયદાથી નિર્ધારિત વેતન બીજા દેશોની સરખામણીમાં નીચું ગણાય છે, તો તેની ઉત્પાદકતા પણ નીચી છે. તેમાં સુધારો કરવાની, તેમને તાલીમ આપવાની જરૂર દેખાય છે. (6) ઉચ્ચ ગુણવત્તા અને વિવિધતાવાળા કાપડનું વિપુલ જથ્થામાં ઉત્પાદન જ વિશ્વના બજારમાં ભારતને અગ્રણી સ્થાન અપાવી શકે.
સૂર્યકાન્ત ત્રિવેદી
આર. આર. શુક્લ
એ. એમ. પટેલ
જિગીશ દેરાસરી